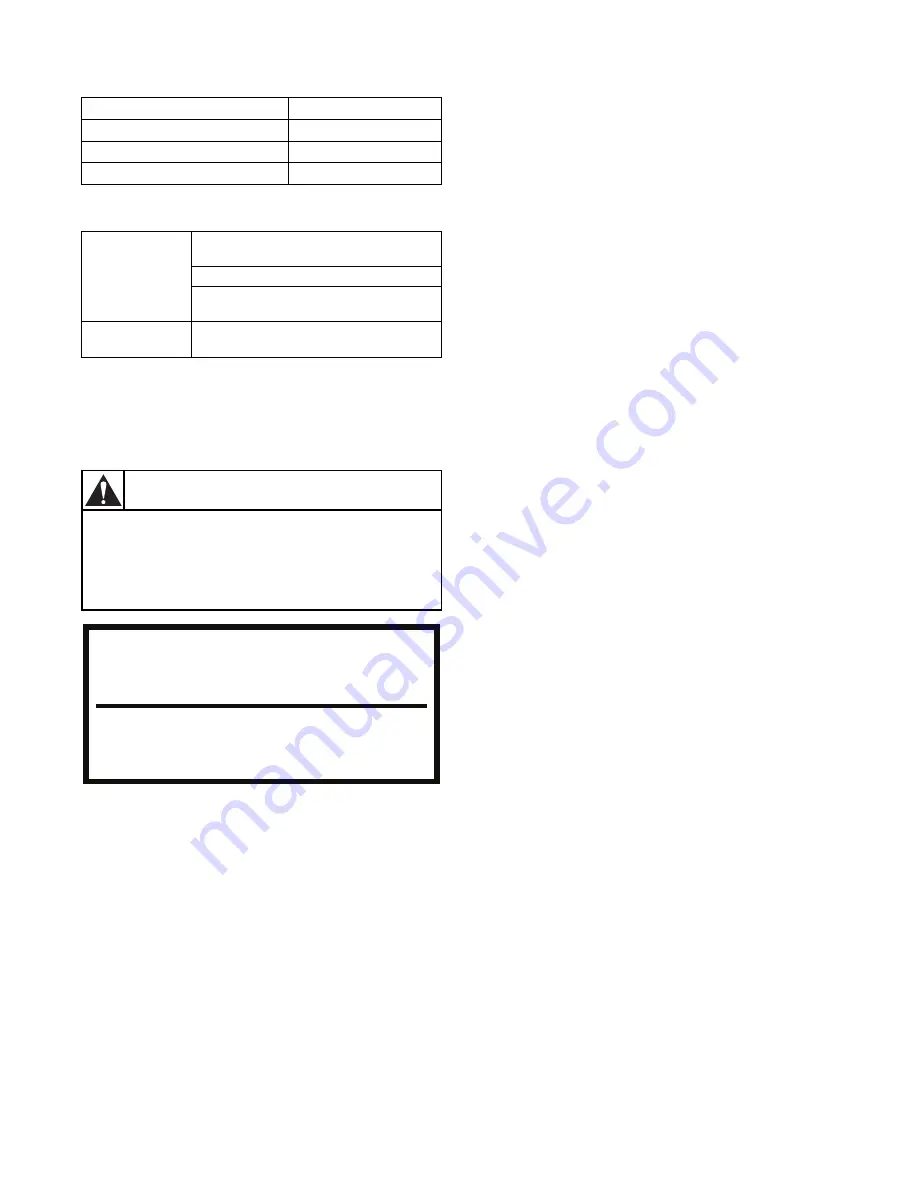
© Copyright, Alliance Laundry Systems LLC – DO NOT COPY or TRANSMIT
Installation
1300003 (EN)
12
Required Materials
IMPORTANT: Keep finisher area clear and free
from combustible materials, gasoline, and other
flammable vapors and liquids.
Location Requirements
IMPORTANT: Transport finisher on skid until
near area of desired installation. Reasonable care
should be taken during installation.
Finisher is shipped with manual crank located on tray.
Be certain to keep manual crank near machine for easy
access.
NOTE: With its trays removed, the finisher will fit
through a 32 inch (813 mm) wide door.
.
To assure compliance, consult and adhere to building
code requirements and comply with the following:
•
The finisher must be installed in a very well
ventilated room (especially when using gas
heating) with correct lighting and an ambient
temperature in the range from 32°F (0
o
C) to
+ 104°F (40
o
C).
•
Leveling should be carried out correctly on a
hard and stable floor surface, capable of
supporting the weight of the finisher. The floor
must at least be able to support 150 lbs./ft
2
(732 kg/m
2
) for the installation of the finisher.
•
The finisher MUST NOT be installed or stored in
an area where it will be exposed to water and/or
weather.
IMPORTANT: DO NOT block the airflow at the
rear of the finisher with laundry or other articles.
Doing so would prevent adequate air supply to the
combustion chamber of the finisher.
Sufficient space must be left around the finisher to
allow for its correct functioning.
•
Allow at least 4 inches (102 mm) in the back to
allow for ventilation.
•
Allow 32 inches (813 mm) on each side for
upkeep and maintenance.
•
Allow sufficient space in front so that the
operator can work efficiently and safely.
Lifting the Finisher
The finisher should be moved with a forklift as close
as possible to the area where it will be installed. Use a
forklift of sufficient capacity to lift the packaged unit
according to the following procedures.
IMPORTANT: DO NOT lift finisher with slings.
1. Position the forklift arms beneath the center of
the unit (NOT toward either end) to lift the
finisher at its center of gravity.
IMPORTANT: Lifting the finisher from either side
could cause misalignment and/or damage to the
finisher.
2. Adjust the forklift arms to their maximum length
and width and insert them all the way under the
center of the skid. Refer to
Figure 3
.
Model
Weight
UD13F063
1320 lbs. (599 kg)
UD13F078 and UD13F079
1474 lbs. (669 kg)
UD13F126
2094 lbs. (950 kg)
All Models
One fused disconnect switch or branch
circuit breaker (obtain locally)
Pry bar
Three 3.5 inch (89 mm) to
4 inch (102 mm) rollers or pipes
Gas Models
One gas shut-off valve for gas service line
to each finisher (obtain locally)
To prevent fire, explosion, or personal
injury, this finisher may only be installed,
adjusted, and started up by a team of
qualified technicians.
W543
WARNING
This machine must be installed in compliance with all local regulations and used
only in a room with adequate ventilation air. Important, read manuals before
installing, operating, servicing or cleaning machine.
Min clearance from both combustible and noncombustible
Construction; 4" from back, 20" from side.
Cet appareil doit être installé conformemént aux réglementations en vigueur et
utilisé seulement dans un endroit bien aéré.
Lire les notices avant d'installer, utiliser, entretenir ou nettoyer la machine.
Espace mini entre machine et matière combustible ou non- combustible:
arrière: 4", côté :20"
FWF141N
FWF141N