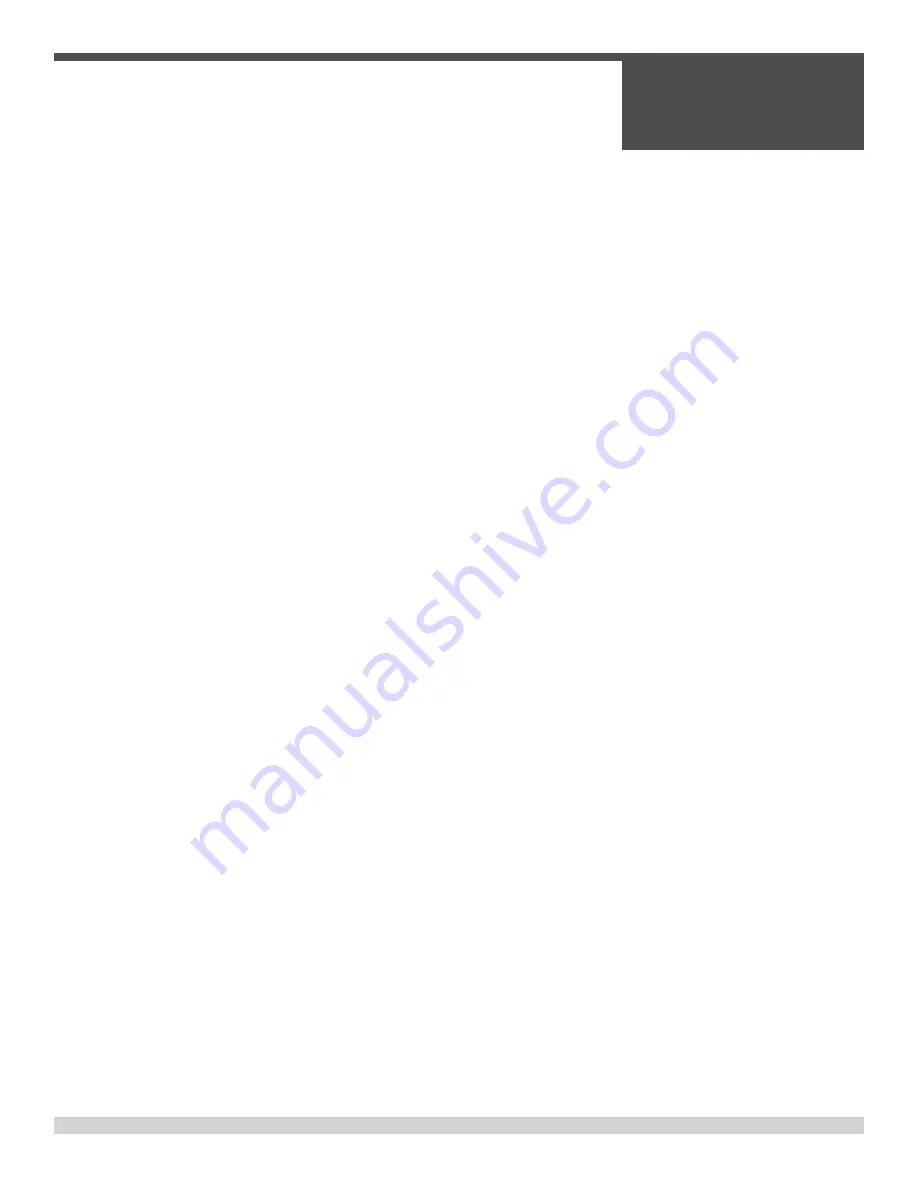
09/2018 - 275
Page 45
SECTION 1
SAFETY
Transportation Safety (cont’d)
Lifting
4. Plan for swing. The counterweight and boom travel within a specific arc that’s called the swing radius. It’s important to
ensure that the area within that radius is barricaded off, and to establish a control zone for those authorized to work in the
immediate area. Also check the area every day to ensure that there are no objects the boom might strike, such as power
lines. If such obstacles exist, be sure that the operator and other workers are aware of the plan for avoiding them.
5. Use cranes properly. Cranes are engineered for vertical lifting. That doesn’t stop some crews from trying to use them for
side loading or other improper activities. Using a crane to drag something across the ground or from under an obstacle puts
extreme stress on the boom, the turntable, and all the structural members. It could potentially weaken key components and
lead to their failure. If someone on the site has used a crane improperly, be sure to inspect it thoroughly to ensure that its
integrity has not been impaired.
6. Stay in touch. Whether you use radios, air horns, or hand signals, there needs to be clear communication between the
operator and the other workers. That’s especially critical when a crane is making a lift in which the operator cannot see
the load, such as when air handling equipment is being delivered through an opening on another side of a structure. Don’t
assume that everyone knows how instructions will be communicated. Follow OSHA’s specific guidelines, and make sure
that everyone on the site knows exactly what each signal means.
7. Pay attention. Everyone associated with a crane needs to stay alert and focused on the job at hand – especially on critical
or difficult lifts.
8. Avoid man-baskets. Sometimes it looks like the easiest way to put employees where they’re needed is to lift a man-bas
-
ket to the work area. However, that approach creates hazards that must be tested and addressed before work begins, such
as providing proper fall protection, verifying basket capacity, and checking that the basket is properly attached. In addition,
the safety of the employees in the basket is entirely dependent on the skill of the operator, and a simple mistake could have
tragic consequences. Before using a man-basket, consider whether an articulating boom lift or a scissor lift might provide
a safer alternative.
9. Don’t use cranes for storage. In areas where site security is a concern, it’s not unusual to see laborers end the workday
by attaching a compressor or similar piece of equipment to the crane and suspending it for safekeeping. It’s a common
practice, but one that’s very risky. In addition to the danger that someone could walk beneath it, a strong wind could cause
the load to sway – perhaps to the point of toppling the crane. But an even better reason not to do this is that most of today’s
newer cranes are hydraulically-operated. A small leak anywhere in the system will eventually reduce the hydraulic pressure
to the point where the boom will drop, and the suspended load will fall on whatever is below it – maybe a more expensive
piece of equipment.
10. Start with a plan. Each lift is different from another, and it’s important to review load weight capacities, the integrity of
the equipment, the possible effect of wind, and other factors. The operator, riggers, and other workers involved with the lift
should be part of that planning process.
Summary of Contents for TRTP275
Page 2: ...INTENTIONALLY BLANK ...
Page 14: ...275 09 2018 Page 14 Engine Specifications ...
Page 15: ...09 2018 275 Page 15 Engine Specifications cont d ...
Page 16: ...275 09 2018 Page 16 Engine Specifications cont d ...
Page 17: ...09 2018 275 Page 17 Engine Specifications cont d ...
Page 18: ...275 09 2018 Page 18 Engine Specifications cont d ...
Page 19: ...09 2018 275 Page 19 Engine Specifications cont d ...
Page 20: ...275 09 2018 Page 20 Sound and Vibration Testing IN PROCESS ...
Page 21: ...09 2018 275 Page 21 Declaration of Conformity IN PROCESS ...
Page 22: ...275 09 2018 Page 22 Declaration of Conformity Hatz Engine ...
Page 23: ...09 2018 275 Page 23 INTENTIONALLY BLANK ...
Page 24: ...275 09 2018 Page 24 SECTION 1 SAFETY State Regulations Proposition 65 Warning ...
Page 25: ...09 2018 275 Page 25 SECTION 1 SAFETY Federal Regulations Respiratory Hazards ...
Page 33: ...09 2018 275 Page 33 SECTION 1 SAFETY Safety Labels and Decals cont d ...
Page 34: ...275 09 2018 Page 34 SECTION 1 SAFETY Safety Labels and Decals cont d ...
Page 46: ...275 09 2018 Page 46 SECTION 1 SAFETY Transportation Safety cont d Rigging ...
Page 47: ...09 2018 275 Page 47 SECTION 1 SAFETY Transportation Safety cont d Rigging ...
Page 48: ...275 09 2018 Page 48 SECTION 1 SAFETY Transportation Safety cont d Rigging ...
Page 49: ...09 2018 275 Page 49 SECTION 1 SAFETY Transportation Safety cont d Rigging ...
Page 50: ...275 09 2018 Page 50 SECTION 1 SAFETY Transportation Safety cont d Rigging ...
Page 51: ...09 2018 275 Page 51 SECTION 1 SAFETY Transportation Safety cont d Rigging ...
Page 65: ...09 2018 275 Page 65 SECTION 2 OPERATIONS Operating Instructions cont d ...
Page 68: ...275 09 2018 Page 68 SECTION 3 SERVICE TRTP Maintenance Schedule ...
Page 73: ...09 2018 275 Page 73 SECTION 3 SERVICE Filter Replacement Cont d Air Filter ...
Page 88: ...275 09 2018 Page 88 SECTION 4 PARTS Engine Assembly Illustration 067770 5 8 10 7 11 4 1 3 2 6 ...
Page 90: ...275 09 2018 Page 90 SECTION 4 PARTS Engine Assembly Illustration 067770 Cont d 9 10 12 ...
Page 106: ...275 09 2018 Page 106 SECTION 4 PARTS 1 4 2 6 3 5 Spray Nozzle Assembly Illustration 044914 ...
Page 155: ...09 2018 275 Page 155 SECTION 4 PARTS ...
Page 156: ...275 09 2018 Page 156 SECTION 4 PARTS Electrical Schematics Plug 20 18 14S 6 ...
Page 157: ...09 2018 275 Page 157 SECTION 4 PARTS Electrical Schematics Cont d Plug 28 12 Part 1 ...
Page 158: ...275 09 2018 Page 158 SECTION 4 PARTS Electrical Schematics Cont d Plug 28 12 Part 2 ...
Page 159: ...09 2018 275 Page 159 SECTION 4 PARTS Electrical Schematics Cont d ...
Page 160: ...275 09 2018 Page 160 SECTION 4 PARTS Electrical Schematics Cont d ...
Page 161: ...09 2018 275 Page 161 SECTION 4 PARTS Hydraulic Schematics 30 34 UNITS ...
Page 162: ...275 09 2018 Page 162 SECTION 4 PARTS Hydraulic Schematics Cont d 30 34 UNITS ...
Page 163: ...09 2018 275 Page 163 SECTION 4 PARTS Hydraulic Schematics Cont 14 28 UNITS ...
Page 166: ...275 09 2018 Page 166 SECTION 4 PARTS Hydraulic Schematics Cont d Block and Hose Diagram ...
Page 167: ...09 2018 275 Page 167 SECTION 4 PARTS Hydraulic Schematics Cont Block and Hose Diagram ...
Page 169: ...09 2018 275 Page 169 SECTION 4 PARTS Spray System Schematic ...