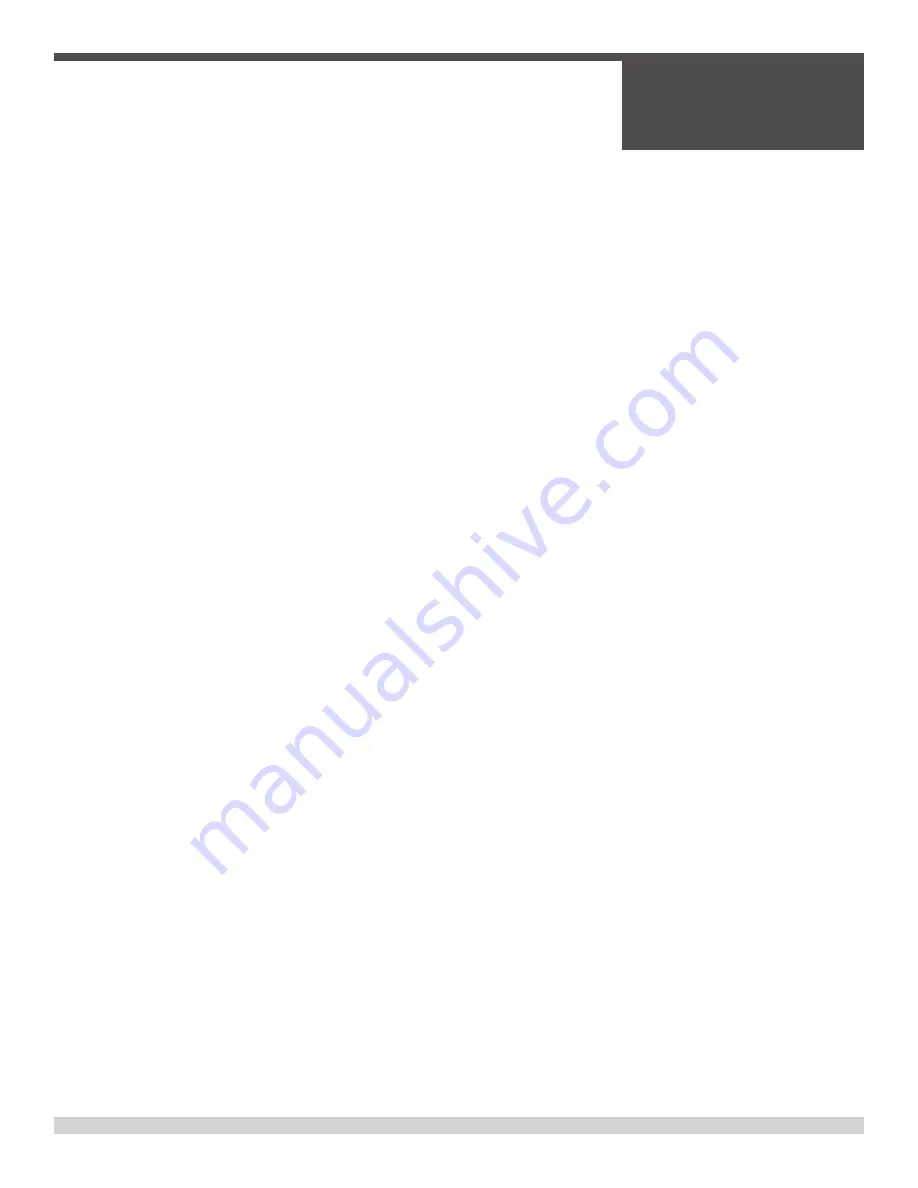
09/2018 - 275
Page 41
SECTION 1
SAFETY
Transportation Safety (cont’d)
Lifting
Before using mobile lifting equipment the following safety precautions should be taken:
• The working environment: Routes should be leveled, marked and planned in such a way as to avoid potential hazards
such as overhead power lines and steeply sloping ground. Where possible a one-way system should be used. Speed limits
should be required and clearly displayed, they should be reduced for adverse site conditions and for areas near work in
progress. The working environment should be kept clean and tidy, with floors and access routes clear of obstacles. Good
lighting levels are needed to ensure that all potential hazards, e.g. obstructions and spills can be clearly seen. All stairs,
ramps and other level changes should be clearly visible and slip resistant; safety signs should be used where appropriate.
• Check machines on fuel, oil, and water levels, water, fuel, and hydraulic lines for leaks, the condition of the tracks or tires,
the condition of attachment cutting edges and teeth, visibility from the cab, windows, mirrors and lights, worn or slippery
surfaces, etc.
• If vehicles drive backwards when the driver’s rear view is obscured, the help of another worker is required. If no one is
available, the driver must walk round to the rear of the vehicle themselves to see that all is clear and give a sound signal
before starting to reverse. Additionally, these vehicles should use an audible warning device such as a horn when driving
in reverse.
• A crane operator should always move loads according to the established code of signals, and use a signaler. Hand signals
are preferred and commonly used. A signaler may be required by law if the operator’s view of the intended path of travel is
obstructed. The assistance of a trained and authorized signaler should be available when the view of the driver or operator
is restricted. The signaler must be in clear view of the operator, have a clear view of the load and equipment and keep other
persons out of the machine’s operating area.
• An unattended vehicle should have the engine switched off, and unless the vehicle is on a marked incline the gear should
be left in neutral and the handbrake on; on sloping ground the wheels should also be chocked. Tipping bodies should be
lowered when the machine is unattended, but if it is occasionally necessary to leave them in the raised position they should
be blocked to prevent their fall.
• Drivers and their assistants should wear safety shoes during loading and unloading.
Maintenance and inspection
Accidents may happen because lifting equipment is not inspected and maintained regularly. All equipment should be thor
-
oughly examined prior to it being put into service and after there has been any major alteration that could affect its opera
-
tion. Lifting equipment may need to be thoroughly examined at intervals laid down in an examination scheme drawn up by
a competent person, taking into account the manufacturer’s recommendations. If equipment is intended to carry people, a
thorough examination must be undertaken every six months. Lifting equipment for all other purposes should be tested at
least every twelve months unless a specific inspection regime is implemented by the examining engineer. Lifting accesso
-
ries do not normally need formal inspection, provided that proper pre-use checks are made and they undergo their standard
thorough examination. All examinations must be undertaken by a competent person who is sufficiently independent and
impartial in order that an objective decision can be made.
Summary of Contents for TRTP275
Page 2: ...INTENTIONALLY BLANK ...
Page 14: ...275 09 2018 Page 14 Engine Specifications ...
Page 15: ...09 2018 275 Page 15 Engine Specifications cont d ...
Page 16: ...275 09 2018 Page 16 Engine Specifications cont d ...
Page 17: ...09 2018 275 Page 17 Engine Specifications cont d ...
Page 18: ...275 09 2018 Page 18 Engine Specifications cont d ...
Page 19: ...09 2018 275 Page 19 Engine Specifications cont d ...
Page 20: ...275 09 2018 Page 20 Sound and Vibration Testing IN PROCESS ...
Page 21: ...09 2018 275 Page 21 Declaration of Conformity IN PROCESS ...
Page 22: ...275 09 2018 Page 22 Declaration of Conformity Hatz Engine ...
Page 23: ...09 2018 275 Page 23 INTENTIONALLY BLANK ...
Page 24: ...275 09 2018 Page 24 SECTION 1 SAFETY State Regulations Proposition 65 Warning ...
Page 25: ...09 2018 275 Page 25 SECTION 1 SAFETY Federal Regulations Respiratory Hazards ...
Page 33: ...09 2018 275 Page 33 SECTION 1 SAFETY Safety Labels and Decals cont d ...
Page 34: ...275 09 2018 Page 34 SECTION 1 SAFETY Safety Labels and Decals cont d ...
Page 46: ...275 09 2018 Page 46 SECTION 1 SAFETY Transportation Safety cont d Rigging ...
Page 47: ...09 2018 275 Page 47 SECTION 1 SAFETY Transportation Safety cont d Rigging ...
Page 48: ...275 09 2018 Page 48 SECTION 1 SAFETY Transportation Safety cont d Rigging ...
Page 49: ...09 2018 275 Page 49 SECTION 1 SAFETY Transportation Safety cont d Rigging ...
Page 50: ...275 09 2018 Page 50 SECTION 1 SAFETY Transportation Safety cont d Rigging ...
Page 51: ...09 2018 275 Page 51 SECTION 1 SAFETY Transportation Safety cont d Rigging ...
Page 65: ...09 2018 275 Page 65 SECTION 2 OPERATIONS Operating Instructions cont d ...
Page 68: ...275 09 2018 Page 68 SECTION 3 SERVICE TRTP Maintenance Schedule ...
Page 73: ...09 2018 275 Page 73 SECTION 3 SERVICE Filter Replacement Cont d Air Filter ...
Page 88: ...275 09 2018 Page 88 SECTION 4 PARTS Engine Assembly Illustration 067770 5 8 10 7 11 4 1 3 2 6 ...
Page 90: ...275 09 2018 Page 90 SECTION 4 PARTS Engine Assembly Illustration 067770 Cont d 9 10 12 ...
Page 106: ...275 09 2018 Page 106 SECTION 4 PARTS 1 4 2 6 3 5 Spray Nozzle Assembly Illustration 044914 ...
Page 155: ...09 2018 275 Page 155 SECTION 4 PARTS ...
Page 156: ...275 09 2018 Page 156 SECTION 4 PARTS Electrical Schematics Plug 20 18 14S 6 ...
Page 157: ...09 2018 275 Page 157 SECTION 4 PARTS Electrical Schematics Cont d Plug 28 12 Part 1 ...
Page 158: ...275 09 2018 Page 158 SECTION 4 PARTS Electrical Schematics Cont d Plug 28 12 Part 2 ...
Page 159: ...09 2018 275 Page 159 SECTION 4 PARTS Electrical Schematics Cont d ...
Page 160: ...275 09 2018 Page 160 SECTION 4 PARTS Electrical Schematics Cont d ...
Page 161: ...09 2018 275 Page 161 SECTION 4 PARTS Hydraulic Schematics 30 34 UNITS ...
Page 162: ...275 09 2018 Page 162 SECTION 4 PARTS Hydraulic Schematics Cont d 30 34 UNITS ...
Page 163: ...09 2018 275 Page 163 SECTION 4 PARTS Hydraulic Schematics Cont 14 28 UNITS ...
Page 166: ...275 09 2018 Page 166 SECTION 4 PARTS Hydraulic Schematics Cont d Block and Hose Diagram ...
Page 167: ...09 2018 275 Page 167 SECTION 4 PARTS Hydraulic Schematics Cont Block and Hose Diagram ...
Page 169: ...09 2018 275 Page 169 SECTION 4 PARTS Spray System Schematic ...