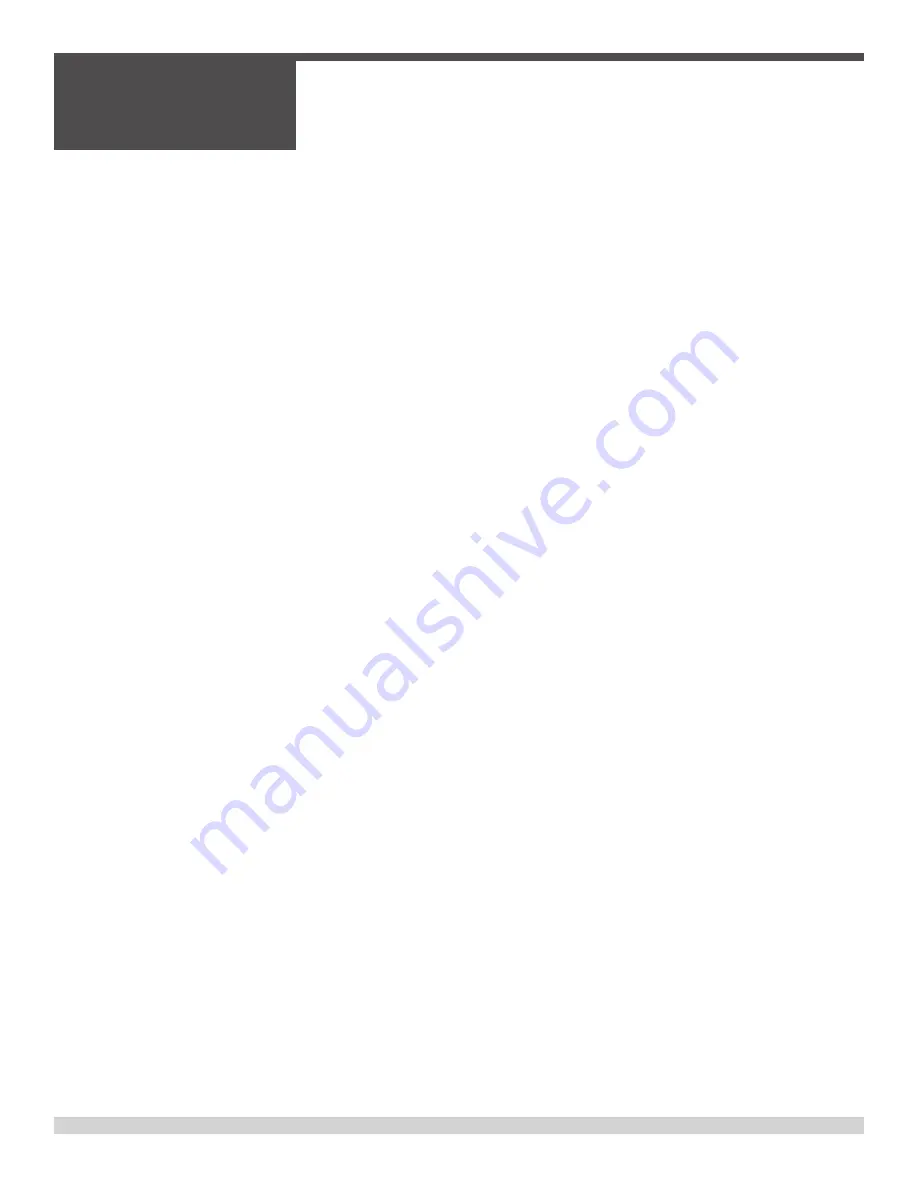
275 - 09/2018
Page 42
SECTION 1
SAFETY
Transportation Safety (cont’d)
Lifting
What needs to be examined depends on the professional judgment of the competent person undertaking the examination.
For most common lifting equipment and accessories, there are standard procedures and criteria. Methods include a visual
examination and functional checks, measurements of wear, traditional non-destructive testing and load testing.
Where an examination scheme has been drawn up, this should identify and specify the parts to be thoroughly examined, the
methods of examination and testing and the intervals for examination (and testing of the different parts, where appropriate).
General Requirements
A. Manufacturer’s labels, e.g. operating instructions, hazard warnings, and rated load capacities, shall not be defaced.
B. Guards and other safety devices shall be in place and operable before any lifting device is used.
C. All personnel performing work on behalf of USPL have the responsibility and authority to stop any lifting operation they
consider to be unsafe.
D. People shall not stand, pass, or work directly under a suspended load.
E. The operator shall always stop the engine(s) on any mobile crane before leaving it unattended.
F. Wherever a lift could endanger personnel, a horn or similar warning device shall be sounded to warn personnel in the
area that a lift is taking place.
G. Any crane or mechanical equipment capable of having parts of its structure elevated near energized overhead electrical
lines shall be operated so that a clearance of 20 feet is maintained or a Critical Lift Permit is required.
H. While making lifts, cranes equipped with outriggers shall have them deployed according to the manufacturer’s instruc
-
tions.
I. On truck-mounted cranes, no loads shall be lifted over the front area except as approved by the crane manufacturer.
J. Signal Persons shall be utilized in the following situations:
1. The Lift Operator cannot see the load.
2. The Lift Operator cannot see the path of travel of either the load or the crane.
3. The Lift Operator cannot see the load landing area.
4. The Lift Operator is too far from the load to judge distance accurately.
5. The lifting device is working within 20 feet of live power lines or equipment.
K. Signal Persons or Riggers shall control access to lift areas when lifts could endan
-
ger personnel. No one, except those directly involved with performing the lift, is permitted to en
-
ter the area without notifying and receiving acknowledgment from the Signal Person or Rigger.
L. When Signal Persons use hand signals, the hand signals shall be those prescribed by the applicable ANSI standard, and
an illustration shall be posted at the job site.
1. The crane operator shall provide and post the hand signal chart.
M. When Signal Persons are used with operators of lift devices other than cranes, the Lift Operator and Signal Person shall
agree on the type of hand signals or verbal commands to be used. If a movement is to take place for which a signal or
command has not been discussed prior to the operation, the lift shall stop and the appropriate signal or command shall be
agreed upon before the lifting operations may resume.
N. When traveling or rotating a crane with a load, a tag or restraint line shall be used if swinging of the load is hazardous,
e.g. the load could contact another object or swing out beyond the radius at which it can be controlled. When used near
electrical equipment, tag lines shall be a nonconductive type.
O. When other mobile equipment is used for lifting, commercially available or built from an approved
engineering design attachment devices shall be used.
Summary of Contents for TRTP275
Page 2: ...INTENTIONALLY BLANK ...
Page 14: ...275 09 2018 Page 14 Engine Specifications ...
Page 15: ...09 2018 275 Page 15 Engine Specifications cont d ...
Page 16: ...275 09 2018 Page 16 Engine Specifications cont d ...
Page 17: ...09 2018 275 Page 17 Engine Specifications cont d ...
Page 18: ...275 09 2018 Page 18 Engine Specifications cont d ...
Page 19: ...09 2018 275 Page 19 Engine Specifications cont d ...
Page 20: ...275 09 2018 Page 20 Sound and Vibration Testing IN PROCESS ...
Page 21: ...09 2018 275 Page 21 Declaration of Conformity IN PROCESS ...
Page 22: ...275 09 2018 Page 22 Declaration of Conformity Hatz Engine ...
Page 23: ...09 2018 275 Page 23 INTENTIONALLY BLANK ...
Page 24: ...275 09 2018 Page 24 SECTION 1 SAFETY State Regulations Proposition 65 Warning ...
Page 25: ...09 2018 275 Page 25 SECTION 1 SAFETY Federal Regulations Respiratory Hazards ...
Page 33: ...09 2018 275 Page 33 SECTION 1 SAFETY Safety Labels and Decals cont d ...
Page 34: ...275 09 2018 Page 34 SECTION 1 SAFETY Safety Labels and Decals cont d ...
Page 46: ...275 09 2018 Page 46 SECTION 1 SAFETY Transportation Safety cont d Rigging ...
Page 47: ...09 2018 275 Page 47 SECTION 1 SAFETY Transportation Safety cont d Rigging ...
Page 48: ...275 09 2018 Page 48 SECTION 1 SAFETY Transportation Safety cont d Rigging ...
Page 49: ...09 2018 275 Page 49 SECTION 1 SAFETY Transportation Safety cont d Rigging ...
Page 50: ...275 09 2018 Page 50 SECTION 1 SAFETY Transportation Safety cont d Rigging ...
Page 51: ...09 2018 275 Page 51 SECTION 1 SAFETY Transportation Safety cont d Rigging ...
Page 65: ...09 2018 275 Page 65 SECTION 2 OPERATIONS Operating Instructions cont d ...
Page 68: ...275 09 2018 Page 68 SECTION 3 SERVICE TRTP Maintenance Schedule ...
Page 73: ...09 2018 275 Page 73 SECTION 3 SERVICE Filter Replacement Cont d Air Filter ...
Page 88: ...275 09 2018 Page 88 SECTION 4 PARTS Engine Assembly Illustration 067770 5 8 10 7 11 4 1 3 2 6 ...
Page 90: ...275 09 2018 Page 90 SECTION 4 PARTS Engine Assembly Illustration 067770 Cont d 9 10 12 ...
Page 106: ...275 09 2018 Page 106 SECTION 4 PARTS 1 4 2 6 3 5 Spray Nozzle Assembly Illustration 044914 ...
Page 155: ...09 2018 275 Page 155 SECTION 4 PARTS ...
Page 156: ...275 09 2018 Page 156 SECTION 4 PARTS Electrical Schematics Plug 20 18 14S 6 ...
Page 157: ...09 2018 275 Page 157 SECTION 4 PARTS Electrical Schematics Cont d Plug 28 12 Part 1 ...
Page 158: ...275 09 2018 Page 158 SECTION 4 PARTS Electrical Schematics Cont d Plug 28 12 Part 2 ...
Page 159: ...09 2018 275 Page 159 SECTION 4 PARTS Electrical Schematics Cont d ...
Page 160: ...275 09 2018 Page 160 SECTION 4 PARTS Electrical Schematics Cont d ...
Page 161: ...09 2018 275 Page 161 SECTION 4 PARTS Hydraulic Schematics 30 34 UNITS ...
Page 162: ...275 09 2018 Page 162 SECTION 4 PARTS Hydraulic Schematics Cont d 30 34 UNITS ...
Page 163: ...09 2018 275 Page 163 SECTION 4 PARTS Hydraulic Schematics Cont 14 28 UNITS ...
Page 166: ...275 09 2018 Page 166 SECTION 4 PARTS Hydraulic Schematics Cont d Block and Hose Diagram ...
Page 167: ...09 2018 275 Page 167 SECTION 4 PARTS Hydraulic Schematics Cont Block and Hose Diagram ...
Page 169: ...09 2018 275 Page 169 SECTION 4 PARTS Spray System Schematic ...