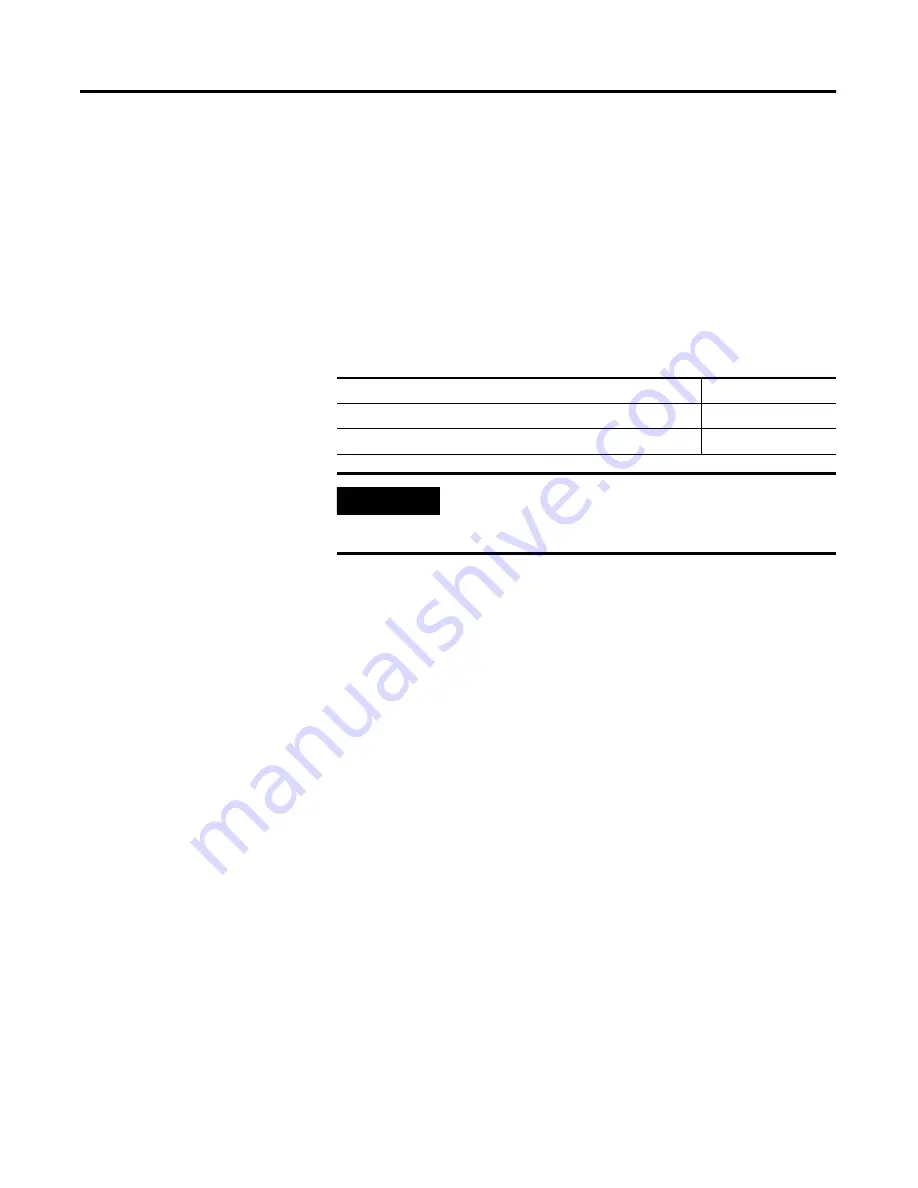
117
Publication 1756-UM001G-EN-P - January 2007
Chapter
10
SIL 2 Certification
Introduction
This chapter explains how ControlLogix system components are
type-approved and certified for use in SIL 2 applications, according to
IEC 61508 and AK4 applications in line with DIN V19250. SIL
requirements are based on the standards current at the time of
certification.
SIL 2 Overview
A Safety Integration Level (SIL) is a numeric designator assigned to a
safety system that indicates that system’s ability to perform its safety
function. The SIL 2 TYPE certification of ControlLogix products by
TUV, an internationally recognized and accredited test laboratory
certification center, assures the suitability of ControlLogix products for
use in up to a SIL 2 safety application. TUV certification is based
primarily on compliance with IEC 61508 Functional Safety of
Electrical/Electronic/Programmable Electronic Safety-Related Systems
requirements. It also includes a number of application-independent
standards, DIN V 19250 and VDE 0801, application-dependent
standards, prEN 50156 for ESD applications, DIN EN 54 for fire and
gas application, and environmental and electrical safety standards, IEC
61131-2, EN 50178, EN 50081-2, and EN 61000-2:2000.
These requirements consist of mean time between failures (MTBF),
probability of failure, failure rates, diagnostic coverage and safe failure
fractions that fulfill SIL 2 criteria. The results make the ControlLogix
system suitable up to, and including, SIL 2. When the ControlLogix
system is in maintenance or programming mode, the user is
responsible for maintaining a safe state.
For support in the creation of programs, the PADT (Programming and
Debugging Tool) is required. The PADT for ControlLogix is RSLogix
5000 programming software, per IEC 61131-3, and this Safety
Reference Manual.
Topic
Page
IMPORTANT
For a list of ControlLogix system components that meet SIL 2
requirements, see Using ControlLogix in Sil 2 Applications
Reference Manual
,
publication 1765-RM001
Summary of Contents for controllogix 1756-L55M12
Page 4: ...Publication 1756 UM001G EN P January 2007 Summary of Changes 4 Notes...
Page 10: ...Publication 1756 UM001G EN P January 2007 10 Notes...
Page 66: ...Publication 1756 UM001G EN P January 2007 66 Place Configure and Monitor I O Modules Notes...
Page 82: ...Publication 1756 UM001G EN P January 2007 82 Develop Applications Notes...
Page 122: ...Publication 1756 UM001G EN P January 2007 122 Maintain Nonvolatile Memory Notes...
Page 130: ...Publication 1756 UM001G EN P January 2007 130 Maintain the Battery Notes...
Page 134: ...Publication 1756 UM001G EN P January 2007 134 LED Indicators Notes...