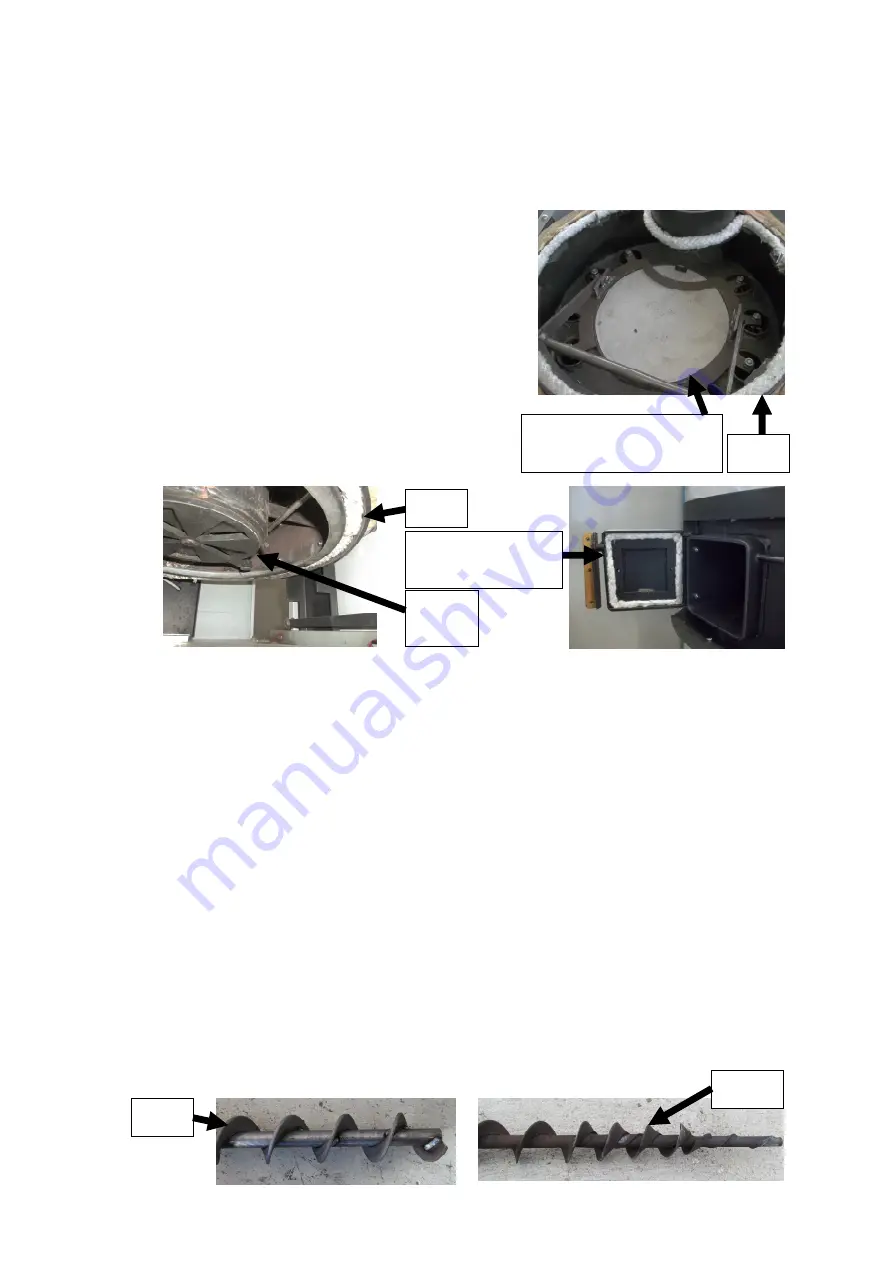
F:\C - E\ECOMAX\COAL BOILER\Instructions and Manuals\Coal Boiler Manual Rev 6.doc
Page
25
of 36
Yearly Maintenance
Yearly maintenance should be carried out before the start of the heating season to
allow time to rectify any issues.
•
Remove the top and clean out all the fly ash
in the top of the Combustion Chamber.
Remove the plate at the top of the
Combustion Chamber so you can see the
Burn Pot and scrape all soot build up from the
internal walls.
•
Check the door seals are intact, do not have
gaps and are not excessively frayed on the:
Combustion Chamber Door
Ash Pan
Top Plate
•
Visually check the electrical wiring for any signs of damage.
•
Check the condition of the Ash Pan. It should not be excessively warped, and it
should slide easily into place. It must seal well against the bottom of the
Combustion Chamber. Replace if necessary.
•
Check the Burn Pot for signs of deformation and wear. If the air ports are
deforming or enlarging, or the burn pot is splitting it will need to be replaced.
•
Disconnect the Blower from the boiler and thoroughly clean it. Lubricate the
fan cage by putting a few drops of oil on the motor shaft.
•
Check the colour and level of the gearbox oil. It should be light and
transparent.
•
Check the Coal Feed Screw has not worn and can turn freely in the Coal Feed
Screw Pipe. The flights should be a consistent thickness, diameter and pitch all
the way along the shaft. If the flights are thin or the welds are broken, the Coal
Feed Screw will need to be replaced.
Seal
Combustion Chamber
underneath this plate
Seal
Ash
Valve
Combustion
Chamber Door
New
Worn