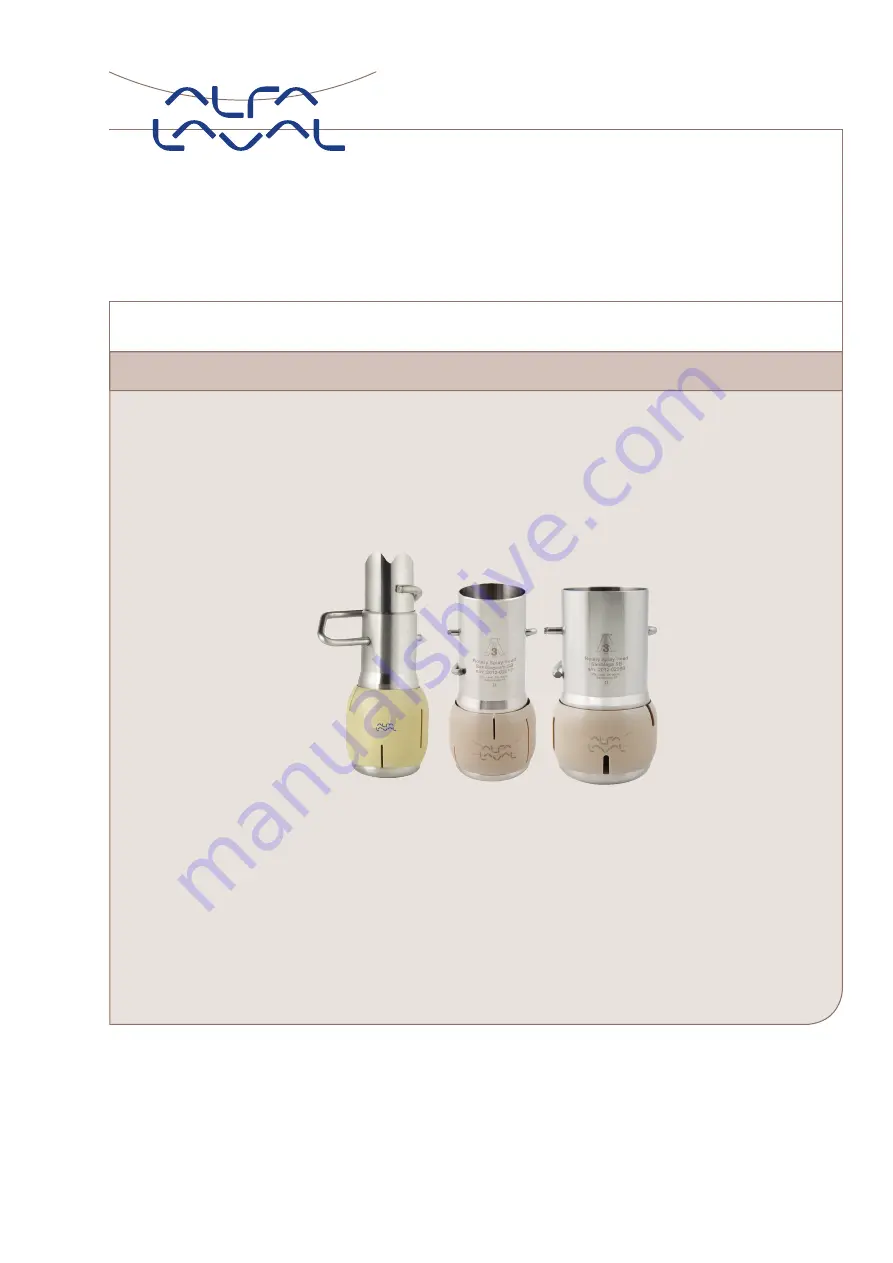
Covering: Standard machines
3-A standard version (clip-on & weld-on). UltraPure standard version (clip-on & weld-on)
Machines delivered with ATEX/IECEx Certification in accordance with Directive 2014/34/EU
Q-doc - Equipment Doc (3.1 Inspection Certificate - EN 10204)
Q-doc - Qualification Doc (Qualification Documentation, FAT/SAT)
First published: 2009-09
ESE01844-EN10
2019-11
Original manual
Instruction Manual
Alfa Laval Toftejorg™ SaniMidget SB, SaniMagnum SB & SaniMega SB