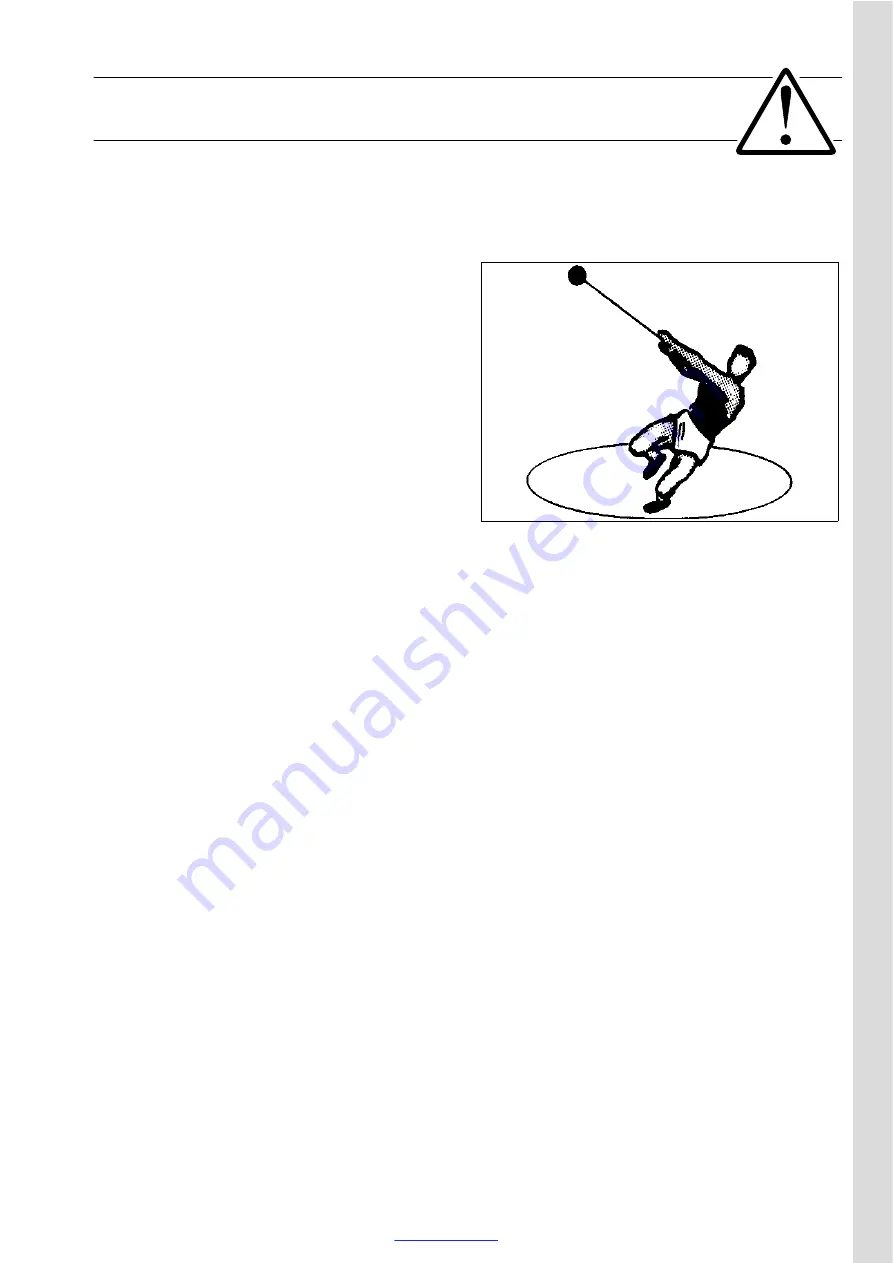
[email protected]
Movil:959440045
9
2
Safety Instructions
The centrifugal separator includes parts that
rotate at high speed. This means that:
•
Kinetic energy is high
•
Great forces are generated
•
Stopping time is long
Manufacturing tolerances are extremely fine.
Rotating parts are carefully balanced to reduce
undesired vibrations that can cause a breakdown.
Material properties have been considered
carefully during design to withstand stress and
fatigue.
The separator is designed and supplied for a
specific separation duty (type of liquid, rotational
speed, temperature, density etc.) and must not be
used for any other purpose.
Incorrect operation and maintenance can result in
unbalance due to build-up of sediment, reduction
of material strength, etc., that subsequently could
lead to serious damage and/or injury.
The following basic safety instructions therefore
apply:
•
Use the separator only for the purpose
and parameter range specified by
Alfa Laval.
•
Strictly follow the instructions for
installation, operation and maintenance.
•
Ensure that personnel are competent and
have sufficient knowledge of maintenance
and operation, especially concerning
emergency stopping procedures.
•
Use only Alfa Laval genuine spare parts
and the special tools supplied.
G
0
01
04
1
1
www.fdm.com.pe
Summary of Contents for MMPX 303SGP-11
Page 6: ...ventas fdm com pe fdmsac gmail com Movil 959440045 6 www fdm com pe...
Page 14: ...ventas fdm com pe fdmsac gmail com Movil 959440045 2 Safety Instructions 14 www fdm com pe...
Page 78: ...ventas fdm com pe fdmsac gmail com Movil 959440045 78 www fdm com pe...
Page 124: ...ventas fdm com pe fdmsac gmail com Movil 959440045 124 www fdm com pe...
Page 155: ...ventas fdm com pe fdmsac gmail com Movil 959440045 155 www fdm com pe...
Page 159: ...ventas fdm com pe fdmsac gmail com Movil 959440045 159 www fdm com pe...
Page 174: ...ventas fdm com pe fdmsac gmail com Movil 959440045 174 www fdm com pe...
Page 176: ...ventas fdm com pe fdmsac gmail com Movil 959440045 176 www fdm com pe...
Page 178: ...ventas fdm com pe fdmsac gmail com Movil 959440045 178 www fdm com pe...