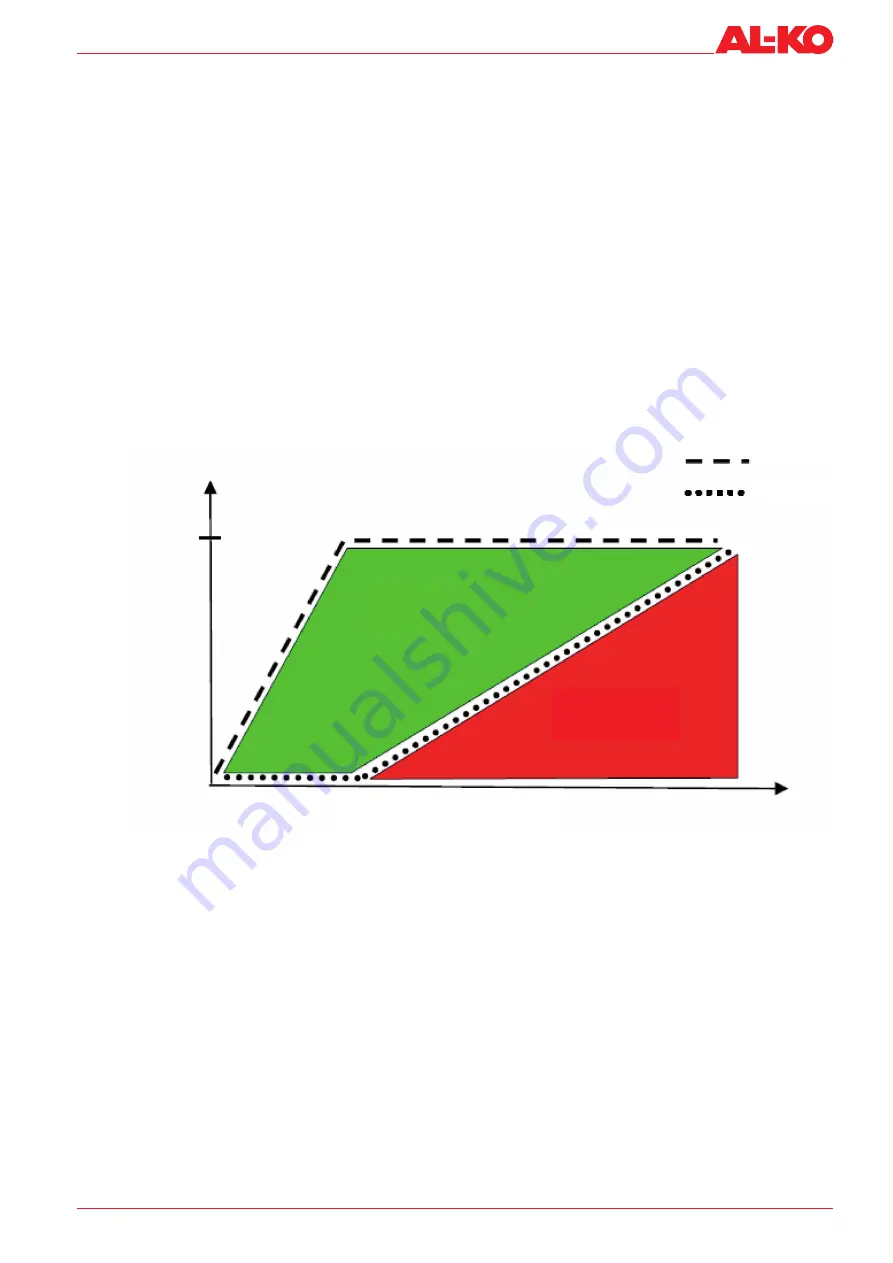
Subject to changes in line with technical progress.
15
3061955
Commissioning
3.4
Control-oriented integration of the HYDROOPT M
®
in the customer's instrument and control
facilities
The closed-cycle system covers the majority of the heat output during operation by recovering heat from the exhaust
air flow.
Due to the inertia of the system, any existing pump hot water heater (PWW) must be rinsed before starting the central
ventilation system.
After a rinsing period to warm up the on-site pipeline system, the air shut-off dampers must be opened.
Only then may the fans be put into operation and the enable given for the closed-cycle system.
After the enable contact, an analogue request signal (0–10 Volt) is required by the customer for operation of the
closed-cycle system. The heat recovery output can be controlled proportionally from 0–100 % via the signal.
Thus the complete station behaves like a (albeit sluggish) heating valve with a continuous valve drive and can be easily
integrated in the customer's control strategy.
The decision whether the heat recovery can take place must be made by the customer's control system by comparing
the air temperature.
y
100 %
y1 WRG
y2 Heizen
Wärmebedarf
WRG
Heizen
Fig. Control strategy for controlling the HYDROOPT M
®
closed-cycle system
HRO
Heating
Heating requirement
y1 HRO
y2 Heating