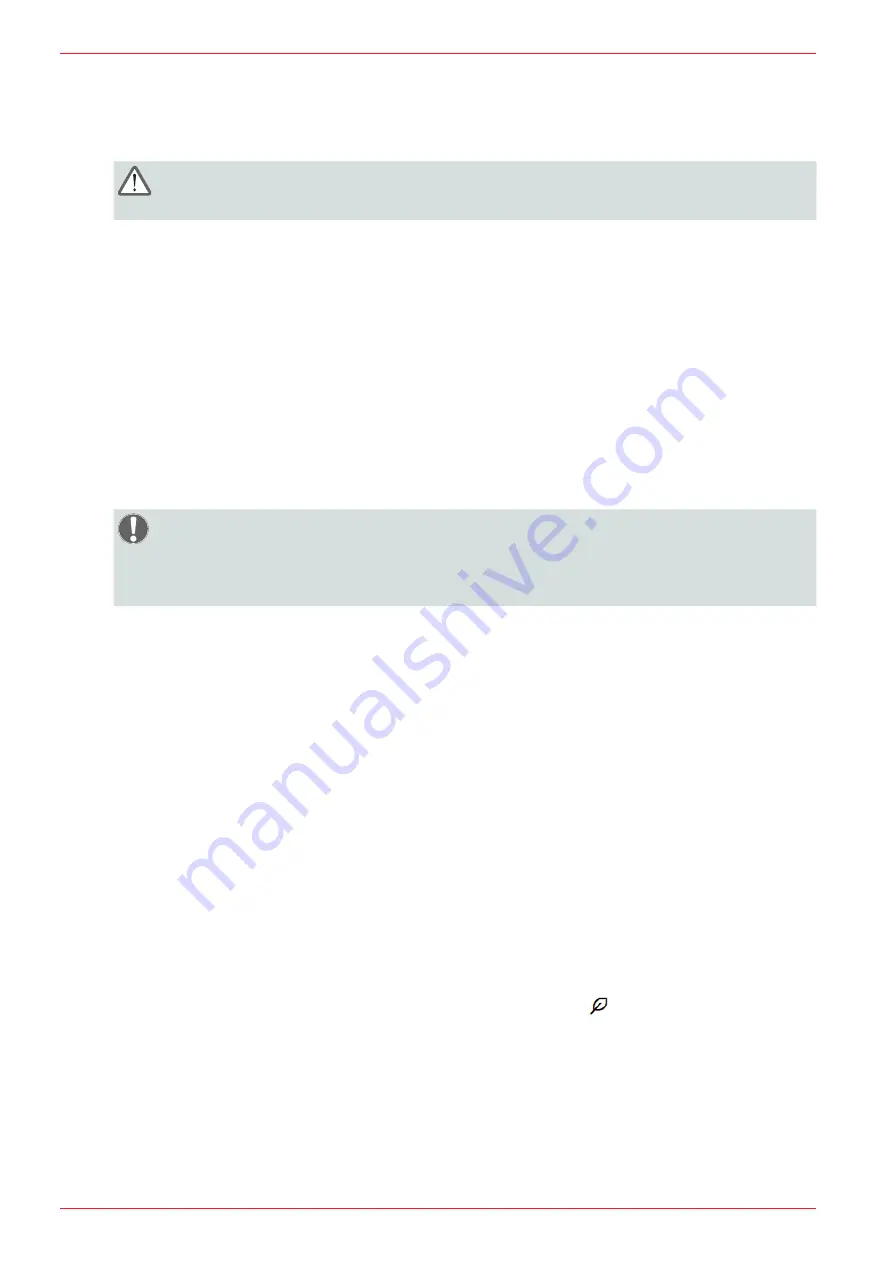
Translation of the original installation and operating instructions
14
AL-KO HYDROOPT
®
3
Commissioning
3.1
General information
Warning!
Installation, commissioning, maintenance, and repair work may only be performed by trained and qualified
specialist personnel.
3.2
Requirements
For commissioning the HYDROOPT M
®
station, the following actions must already have been completed on site:
The supply and exhaust air system must be operational.
The air quantities must have already been measured.
The glycol content of the system must already have been determined.
The system pressure must correspond to the specified idle pressure.
All isolation devices on the station and any on the heat exchangers must be open.
The electrical supply of the station must have been checked.. The protective earth conductor and neutral conductor
in particular must be in place.
Important!
The rotary pump must have been vented according to the manufacturer's instructions. For this purpose,
the corresponding plugs must be opened until brine flows out free of bubbles. Please have a suitable
collection container available for this procedure.
Improper venting can cause damage to the rotary pump.
3.3
Procedure for commissioning
After turning on the main switch, the pump can be manually operated on the frequency converter for a brief time.
The direction of rotation must be checked. The corresponding directional arrow is marked on the pump.
The analogue pressure monitor attached upstream of the pump protects the pump from running dry due to lost
brine. The switching threshold was set in the factory to approx. 1.5 bar (warning) and to 0.5 bar media overpres
-
sure (fault).
Finally, reset the frequency converter to AUTOmatic operation.
The pressure transmitter attached to the supply air device must be connected to the inlet nozzle and the device ring
line on the intake side. The pressure transmitter must be set to 4–20 mA.
The measuring range (factory setting 2500 Pa) may have to be adapted.
The pressure transmitter measures the differential pressure at the inlet nozzle and outputs this pressure linearly (not
square root).
The measuring range end value of the flowmeter is set to approx. 1.4x the nominal fluid volume at the factory, as the
fluid volume is raised above the nominal fluid volume even for a short time if there is a risk of frost.
Give the customer's enable signal and bring the customer's power control signal to 10 volts.
From 95 %, the controller display will show the request "Optimizing active”
unless other operating states (e.g.
defrost) are active. The fluid volume is then optimised on the basis of the supply air quantity.
1 m
3
/h brine corresponds to about 3300 m
3
/h air.
This optimisation process can take several minutes.
If the power control signal is set to below 90 % (9 volts), this initially reduces the pump speed. If this reaches a
lower limit of 12 Hz, the brine is also directed past the exhaust air heat exchanger via the power control valve (by
-
pass operation).