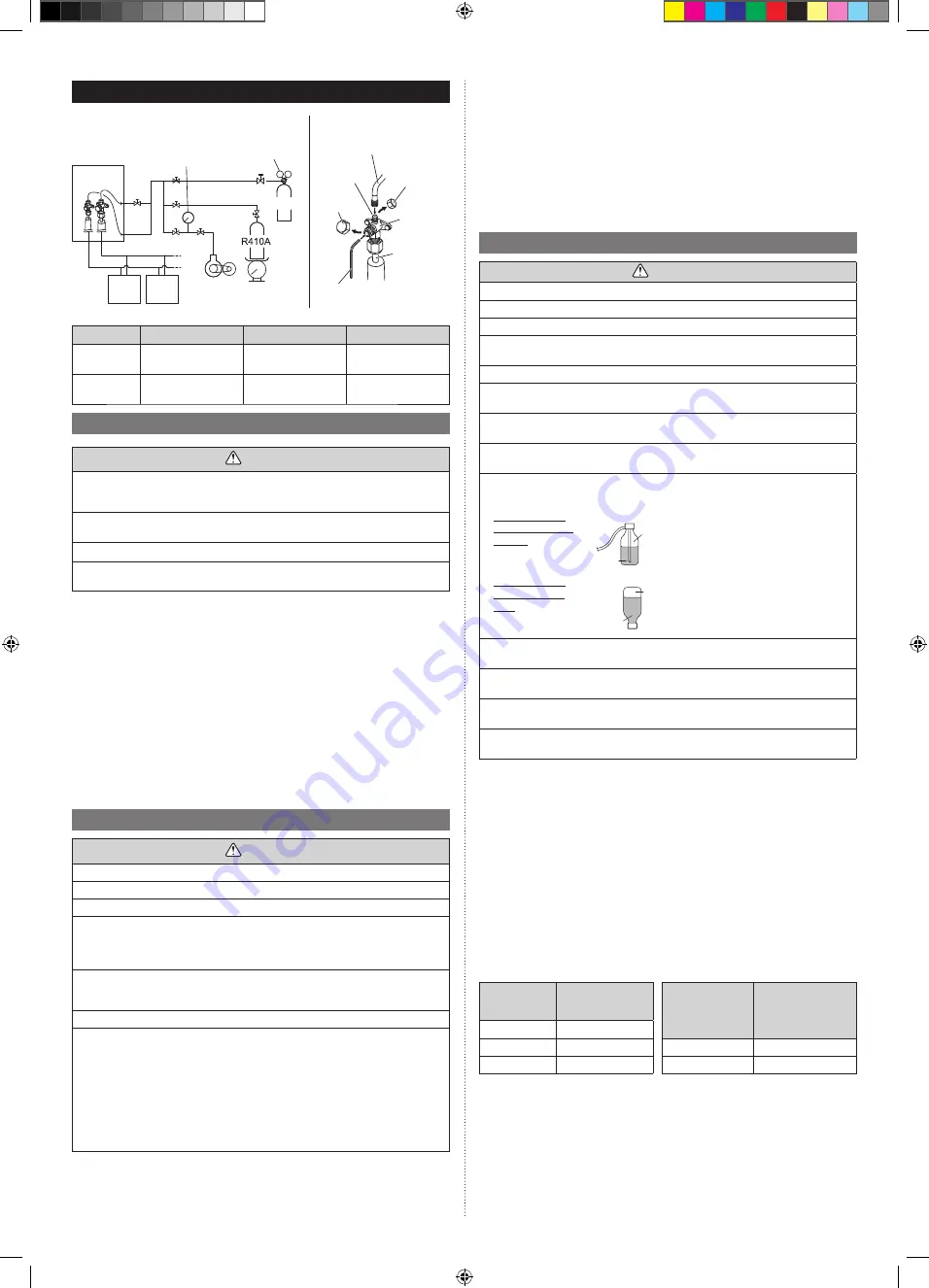
En-15
8. PIPE INSTALLATION II
Fig. A Connection system
Fig. B
Outdoor unit
Pressure
gauge
Vacuum
pump
Scale
Pressure regu-
lating valve
Nitrogen
Indoor
unit
Indoor
unit
Service hose
with valve core
Charging
port
Charging
port cap
3-way
valve
Connecting
pipe
Blank cap
Hexagon wrench
4 mm (5/32")
Table. A
Pipe
3-way valve
Blank cap
Charging port cap
Liquid valve
7.0 to 9.0 N·m
(70 to 90 kgf·cm)
20.0 to 25.0 N·m
(200 to 250 kgf·cm)
12.5 to 16.0 N·m
(125 to 160 kgf·cm)
Gas valve
11.0 to 13.0 N·m
(110 to 130 kgf·cm)
30.0 to 35.0 N·m
(300 to 350 kgf·cm)
12.5 to 16.0 N·m
(125 to 160 kgf·cm)
8.1. Sealing
test
CAUTION
Use only nitrogen gas.
Never use refrigerant gas, oxygen, in
fl
ammable gas or poisonous gas to pressurize the
system. (If oxygen is used, there is the danger of an explosion.)
Do not apply shock during sealing test.
It can rupture the pipes and cause serious injury.
Do not turn on the power unless all operations are complete.
Do not block the walls and the ceiling until the sealing test and the charging of the refrig-
erant gas have been completed.
After connecting the pipes, perform an sealing test.
Recheck that the 3-way valve are closed before performing a sealing test.
(Fig. B)
Pour nitrogen gas through both the liquid pipe and the gas pipe.
Pressurize nitrogen gas to 4.2 MPa to perform the sealing test.
Check all
fl
are connection areas and brazed areas.
Then, check that the pressure has not decreased.
Compare the pressures after pressurizing and letting it stand for 24 hours, and check that
the pressure has not decreased.
* When the outdoor temperature changes 5 °C, the test pressure changes 0.05 MPa.
If the pressure has dropped, the pipe joints may be leaking.
If a leakage is found, immediately repair it and perform a sealing test again.
* Decrease the pressure of nitrogen gas before blazing
After completing the sealing test, release the nitrogen gas from both valves.
Release the nitrogen gas slowly.
8.2. Vacuum
process
CAUTION
Do not turn on the power unless all operations are complete.
If the system is not evacuated suf
fi
ciently, its performance will drop.
Be sure to evacuate the refrigerant system using a vacuum pump.
The refrigerant pressure may sometimes not rise when a closed valve is opened after
the system is evacuated using a vacuum pump. This is caused by the closure of the
refrigerant system of the outdoor unit by the electronic expansion valve. This will not
affect the operation of the unit.
Use a clean gauge manifold and charging hose that were designed speci
fi
cally for use
with R410A. Using the same vacuum equipment for different refrigerants may damage
the vacuum pump or the unit.
Do not purge the air with refrigerants, but use a vacuum pump to evacuate the system.
• If moisture might enter the piping, follow below. (i.e., if doing work during the rainy
season, if the actual work takes long enough that condensation may form on the
inside of the pipes, if rain might enter the pipes during work, etc.)
• After operating the vacuum pump for 2 hours, pressurize to 0.05 MPa (i.e., vacuum
breakdown) with nitrogen gas, then depressurize down to -100.7 kPa (-755 mmHg) for
an hour using the vacuum pump (vacuum process).
• If the pressure does not reach -100.7 kPa (-755 mmHg) even after depressurizing for
at least 2 hours, repeat the vacuum breakdown - vacuum process.
After vacuum process, maintain the vacuum for an hour and make sure the pressure
does not rise by monitoring with a vacuum gauge.
Evacuation procedure
(1) Remove the blank caps of the gas pipe and liquid pipe and check that the valves are
closed.
(2) Remove the charging port cap.
(3) Connect a vacuum pump and a pressure gauge to a charging hose and connect it to
the charging port.
(4) Activate
the
vacuum
pump
and vacuum the indoor unit and connection piping until the
pressure gauge becomes -100.7 kPa (-755mm Hg).
Evacuate from both the gas pipe and the liquid pipe.
(5) Continue
evacuating
the
system
for
1
hour
after the pressure gauge reads -100.7 kPa
(-755mm Hg).
(6) Remove
the
charging
hose
and
reinstall the charging port cap.
8.3. Additional
charging
CAUTION
Do not turn on the power unless all operations are complete.
After evacuating the system, add refrigerant.
Do not charge the system with a refrigerant other than R410A.
Always keep to the limit on the total amount of refrigerant. Exceeding the limit on the
total amount of refrigerant will lead to malfunction during charging of refrigerant.
Do not reuse recovered refrigerant.
Use an electronic scale to measure the charging amount of refrigerant.
Adding more refrigerant than the speci
fi
ed amount will cause a malfunction.
Charge refrigerant using the liquid pipe.
Adding refrigerant through the gas pipe will cause a malfunction.
Add refrigerant by charging the system with the refrigerant in the liquid state. If the refrig-
erant cylinder is equipped with a siphon, it is not necessary to place the cylinder upright.
Check if the steel cylinder has a siphon installed or not before
fi
lling. (There is an indica-
tion “with siphon for
fi
lling liquid” on the steel cylinder.)
Filling method
for cylinder with
siphon
Liquid
Gas
R410A
Set the cylinder vertical and
fi
ll with
the liquid.
(Liquid can be
fi
lled without turning
bottom up with the siphon inside.)
Filling method
for other cylin-
ders
Liquid
Gas
R410A
Turn bottom up and
fi
ll with liquid.
(Be careful to avoid turning over
the cylinder.)
Be sure to use the special tools for R410A for pressure resistance and to avoid mixing of
impure substances.
If the units are further apart than the maximum pipe length, correct operation can not be
guaranteed.
Make sure to back closing valve after refrigerant charging. Otherwise, the compressor
may fail.
Minimize refrigerant release to the air. Excessive release is prohibited under the Freon
Collection and Destruction Law.
8.3.1 Procedure for charging the system with refrigerant
(1) Remove
the
charging
port
cap from the liquid pipe.
(2) Attach a charging hose to the refrigerant cylinder, and connect it to the charging port.
(3) Add
refrigerant
by
calculating
the
additional refrigerant volume in accordance with the
calculation formula indicated below.
(4) Remove the charging hose and install the charging port cap.
(5) Remove the blank caps (gas pipe and liquid pipe) and open the valves.
(6) Close
the
blank
caps.
(7) After
adding
refrigerant,
indicate
the added charging volume on the unit.
* Tighten the blank caps and charging port caps to the torque values speci
fi
ed in the Table
A. To open and close the valves, use an M4 hexagon wrench.
8.3.2
Checking total amount of refrigerant and calculating the
amount of refrigerant charge to be added
• The amount of refrigerant charge to be added is the total value of the basic refrigerant
charge amount and the value calculated from the length of the liquid pipe.
• Round up the value to 2 decimal places.
Model
“B”
Factory charged
amount (kg)
Diameter of liquid
pipe (mm)
“a”
Additional amount
for pipe length (kg/m)
AJ*040LBLAH
4.80
AJ*045LBLAH
5.30
Ø 6.35
0.021
AJ*054LBLAH
5.30
Ø 9.52
0.058
9380545170_IM.indb 15
9380545170_IM.indb 15
5/19/2016 2:23:17 PM
5/19/2016 2:23:17 PM