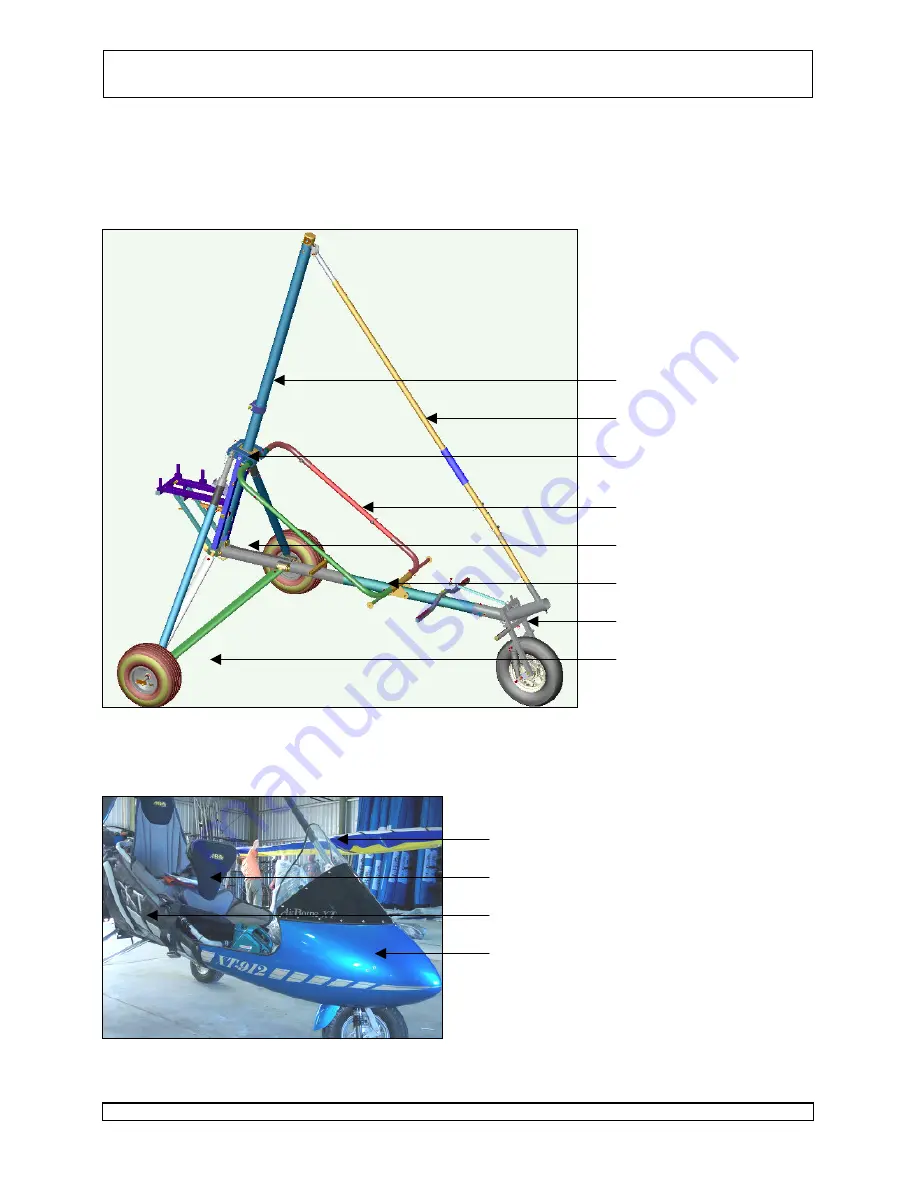
©
A
ir
B
orne
W
ind
S
ports
P
ty.
L
td.
XT 582 Maintenance Manual
Issue 1.0
September 21st 2005
Page 12
00.10.00 Component Overview
Important areas of the Trike base have been identified in this section to aid maintenance personnel.
These photos and list of names are not comprehensive.
Aircraft Structure
Figure 1 Main structural members
Cockpit
Figure 2 Cockpit (XT 912 shown in photo)
Mast
Seat frame
Engine mount sub-frame
Base Tube
Front end assembly
Rear landing gear
Front pole
Mast/Seat block
Windscreen
Seats
Soft-side
Pod