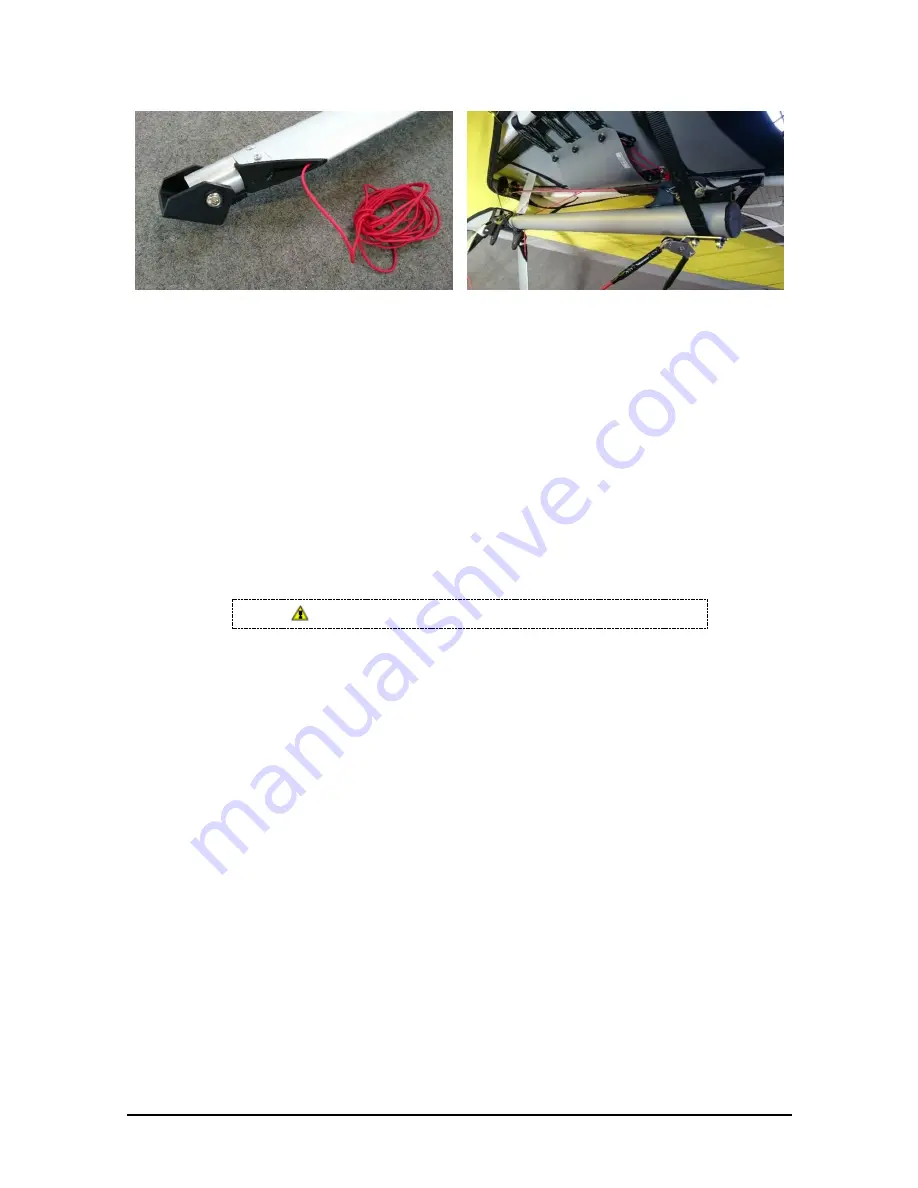
GDMMBi²13-1G
Version 0010
29
Figure 5-27
Figure 5-28
Secure the back-up pull back bridle webbing to the main pull back cables with a ziptie to keep
it close to the hang point. This will ease access when rigging, as the hang point back up cable
also threads through this back-up loop.
11. A-Frame Corner
Refer to the drawing
OP10-32MO
which shows the front view of the port side control frame.
Thread the extension base of the right upright
D258722
to the lower end of it.
Assemble the front lower cables
D201591
and rear lower cables
D202573
to the uprights
using the
CHC / BHC 8-55-13 B085510
screws, washers and nuts as shown in view B on the
drawing.
Thread the wing wires through the
control bar leather protection boots
(D074916)
. The
stitching must be on the back side.
Reinstall a heat shrink sleeve
(P371836)
on the control bar using a heat gun or a hair dryer
and assemble the bases
(D258010)
at its ends. The sleeve must be positioned in a balanced
manner with respect to the bends of the control bar.
Position the control bar at the lower end of the uprights.
Take care of the positioning direction ! (cf 3-6-1, 5)
The
lower side cable N1 (D203674),
fixed on the inner drilling of the cross bar, is positioned
at the front of the assembly.
The
lower side cable N2 (D203675),
fixed on the outer drilling of the cross bar, is positioned
at the back of the assembly.
Apply threadlock and gently tighten the nuts, allowing easy rotation.
12. Batten Clasps
Firmly push the battens in their pockets by hand.
Close the
batten clasps P235020
on the tips of the battens, batten
screws P235015
.
13. Nose of Sail
Check the symmetry of the sail leading edges at the nose plates, move the sail into the middle
by means of the string.
Check the tension of the upper part of the sail leading edge at the nose plate, pull downwards
on the string if necessary to achieve a smooth profile.
If the front part of the leading-edge has been changed, drill a 4mm diameter hole into each
leading edge through the eyelet, remove the string and secure with a self tapping screw. If not,
align the eyelets with the existing holes and secure with the
self-tapping screws
B199010
.
(Refer to drawing
OP10-23CA
& Figure 5-29.)
14. Wing Tip Adjustment
Each wing tip should now be tensioned 10 full turns of the tensioning screw,
screw HM 6-45
(B126410)
(or the value that was checked prior to dismantling the wing if particular settings
need to be reproduced). Figure 5-30.
This should be counted from the start of the slot, or when the slackness in the adjuster screw
is first felt to be taken up. Each turn is equivalent to 1mm of sail tension.
Summary of Contents for BioniX2 13
Page 42: ...GDMMBi 13 1G Version 0010 42...
Page 48: ......