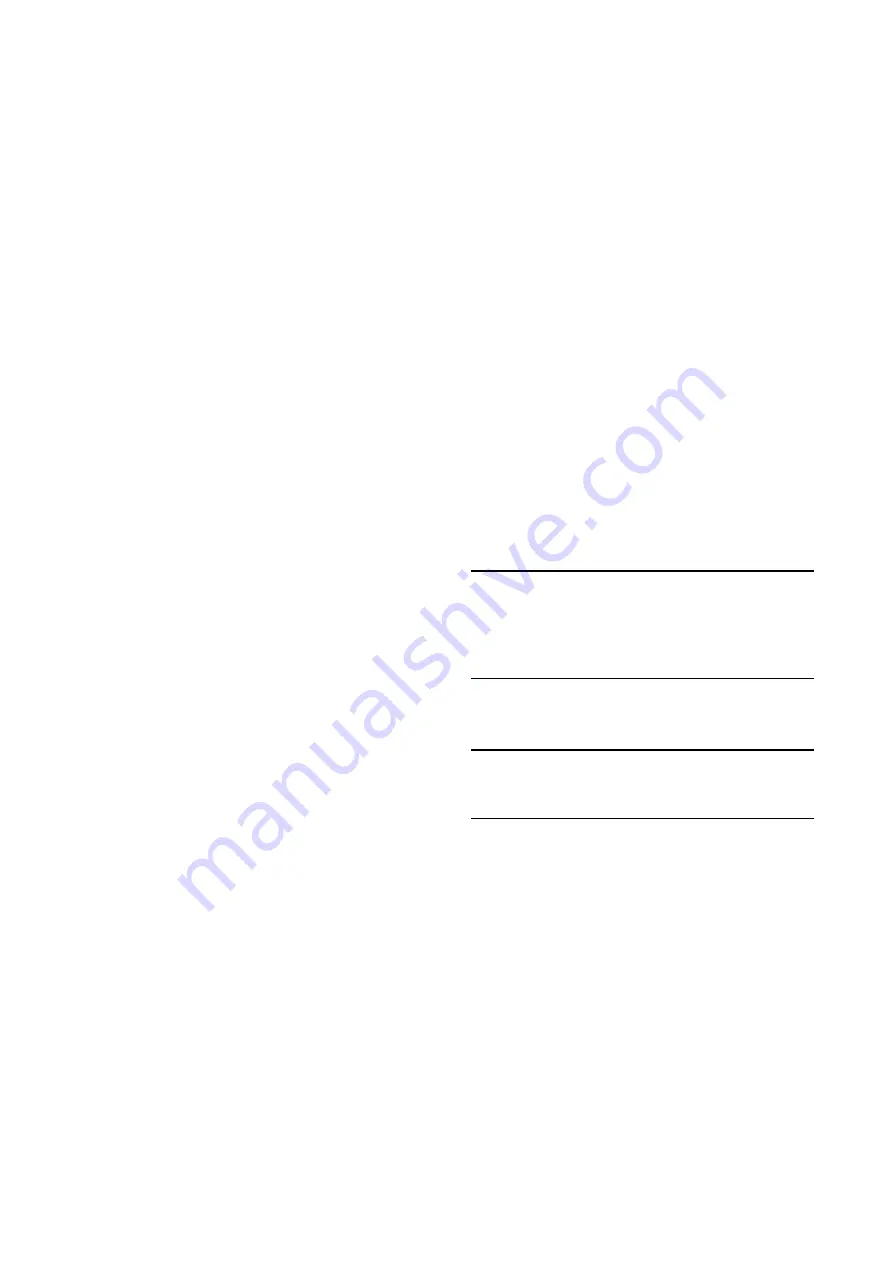
ISTRUZIONI ORIGINALI
TECHNICAL INFORMATION
24/43
87-900-136-01
proach the pump at least until you have pro-
vided ventilation to drive out the smoke. Take
care not to breathe in the fumes remaining in-
side the pump in the course of repair work.
g. In case of fire, do not throw water on the
pump. Switch the power off and use CO
2
ex-
tinguishers.
h. Carefully inspect the flanges to ensure that
there is no dust, oil, dirt or defects of the mat-
ing surfaces, before making the required con-
nections.
i.
Ensure that all joints and couplings are locked
correctly before starting the pump again after
repair work.
j.
Do not wear any objects that may become en-
tangled in the mechanisms and/or act as con-
ductors (chains, bracelets, etc.).
k. Ensure that the tools to be used are in perfect
working condition and have insulating grips,
where necessary. Check that the insulating
material of the cables and that the conductors
of the test equipment do not show any signs
of damage.
l. Do not replace the oil immediately after stop-
ping the machine as the oil may still be at high
temperature.
m. Perform repairs in clean and, where possible,
dust-free areas. Protect all the clearances of
connection points with suitable plastic caps and
cover the machined surface areas of all parts
stripped down until they are put back on the
pump again.
n. Do not start the pump if the fan cover sleeve
(reference 81 of fig. MS-301 Pump parts – Ex-
ploded View and 82 of fig. MS-631 Pump parts
– Exploded View) is not properly in place.
CAUTION NOTES
a. Before putting the pump back into operation
after a breakdown, inspect it and check care-
fully for any other signs of damage.
b. Use only tools that are in perfect working or-
der and specially designed for the job; use of
inappropriate or ineffective tools may cause
serious damage.
c. Perform repairs in clean and, where possible,
dust-free areas. Protect all the clearances of
connection points with suitable plastic caps
and cover the machined surface areas of all
parts stripped down until they are put back on
the pump again.
d. Always check the lubricant and that it is prop-
erly distributed through the pump; inadequate
lubrication may damage the pump seriously.
e. Give the parts some form of marking as you
strip them down to ensure that you reassem-
ble them again in the proper order.
f.
Check that there are no scratches or grooves
on the machined shafts, in their seats inside
the pump or on machine-ground surfaces.
Slight scratches and abrasions may be elimi-
nated with very fine emery paper or by a little
light grinding.
g. Before putting a group together, always
spread a little oil over inner parts and mating
surfaces. Replace all seals with original spare
parts before reassembling components.
MAINTENANCE ACTIONS
Maintenance may be seen as the totality of all
scheduled and unscheduled maintenance work.
Maintenance includes:
1.
SCHEDULED MAINTENANCE:
Maintaining
the nominal state of operation.
2.
UNSCHEDULED MAINTENANCE:
Restoring
the nominal state of operation
NOTE
The frequency with which repairs are performed
depends on the process and presence of sub-
stances that shorten pump life (dust, abrasives,
solvents, water, chemically aggressive sub-
stances).
The pump must be cleaned at regular intervals of
time.
CAUTION
Do not clean with Alcohol the plastic or rubber
components of the pump.
Use only the strictly necessary amount of lubricant;
an excess of lubricating oil, like when there is
none, may sometimes compromise proper opera-
tion of the pump.
Only the recommended lubricants, or lubricating
oils with similar characteristics and known and ex-
perimented quality, should be used.
Oil changes must be made with the oil at a suffi-
ciently high temperature, after leaving the pump to
cool for a few minutes following operation.
The drain and filler plugs must not be left open any
longer than is strictly necessary.
When performing maintenance, look out for all sig-
nals that may precede a breakdown, in particular:
•
traces of corrosion;
•
oil
leaks;