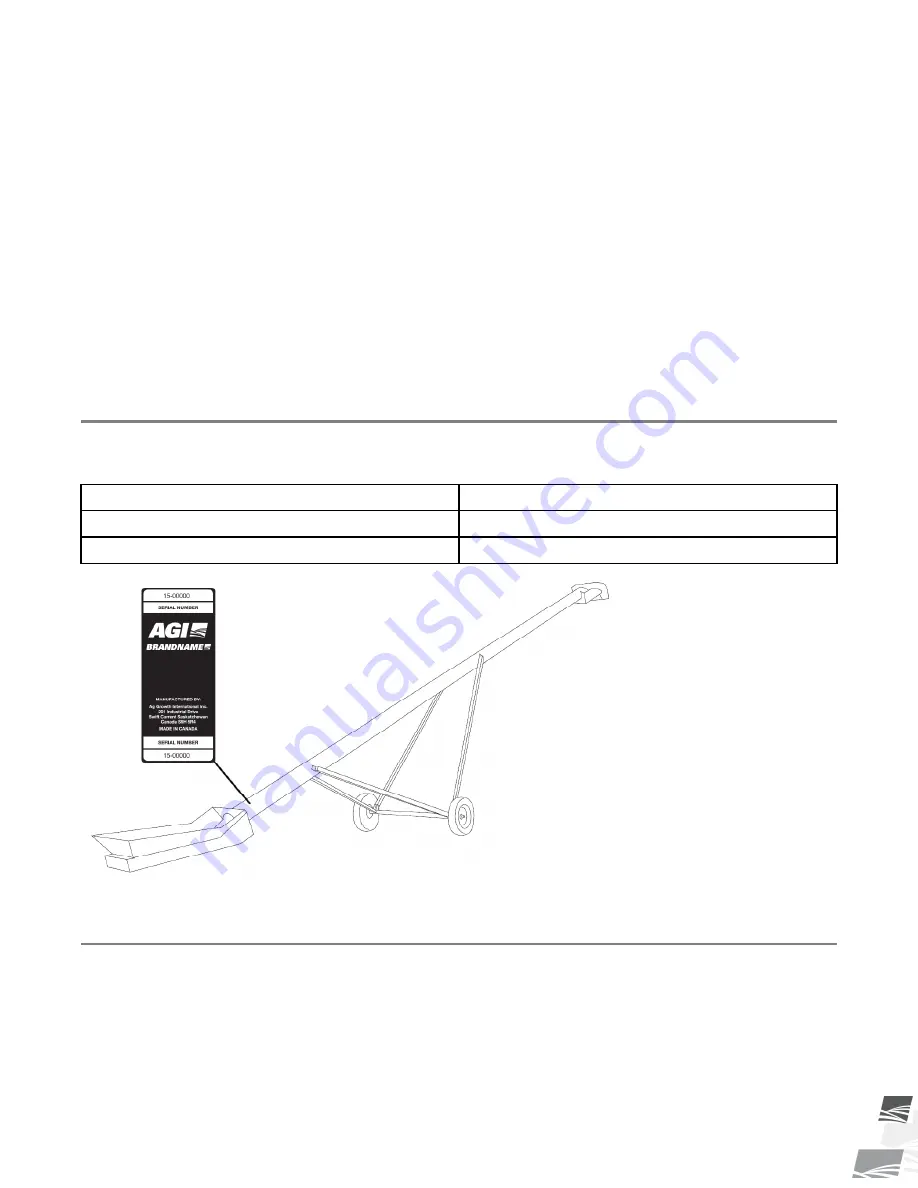
P1512134 R2
5
1. Introduction
Thank you for purchasing a Westfield Portable Grain Belt Conveyor. This equipment will allow safe and
efficient operation when you read and follow all of the instructions contained in this manual. With
proper care, your conveyor will provide you with many years of trouble-free operation.
Keep this manual handy for frequent reference and to review with new personnel. A sign-off form is
provided on the inside front cover for your convenience. If any information in this manual is not
understood or if you need additional information, please contact your local distributor or dealer for
assistance.
This manual should be regarded as part of the equipment. Suppliers of both new and second-hand
equipment are advised to retain documentary evidence that this manual was provided with the
equipment.
1.1. Serial Number Location
Always give your dealer the serial number on your conveyor (shown below) when ordering parts or requesting
service or other information. Please record this information in the table below for easy reference.
Model Number
Serial Number
Date Received
1.2. Intended Use
The conveyor is designed solely for use in the intended agricultural use as listed below. Use in any other way is
considered as contrary to the intended use. Compliance with and strict adherence to the conditions of
operation and maintenance as specified by the manufacturer, also constitute essential elements of the intended
use.
The conveyor should be operated, maintained, serviced, and repaired only by persons who are familiar with its
particular characteristics and who are acquainted with the relevant safety procedures.
S-DRIVE FIELD LOADER – PORTABLE GRAIN BELT CONVEYOR