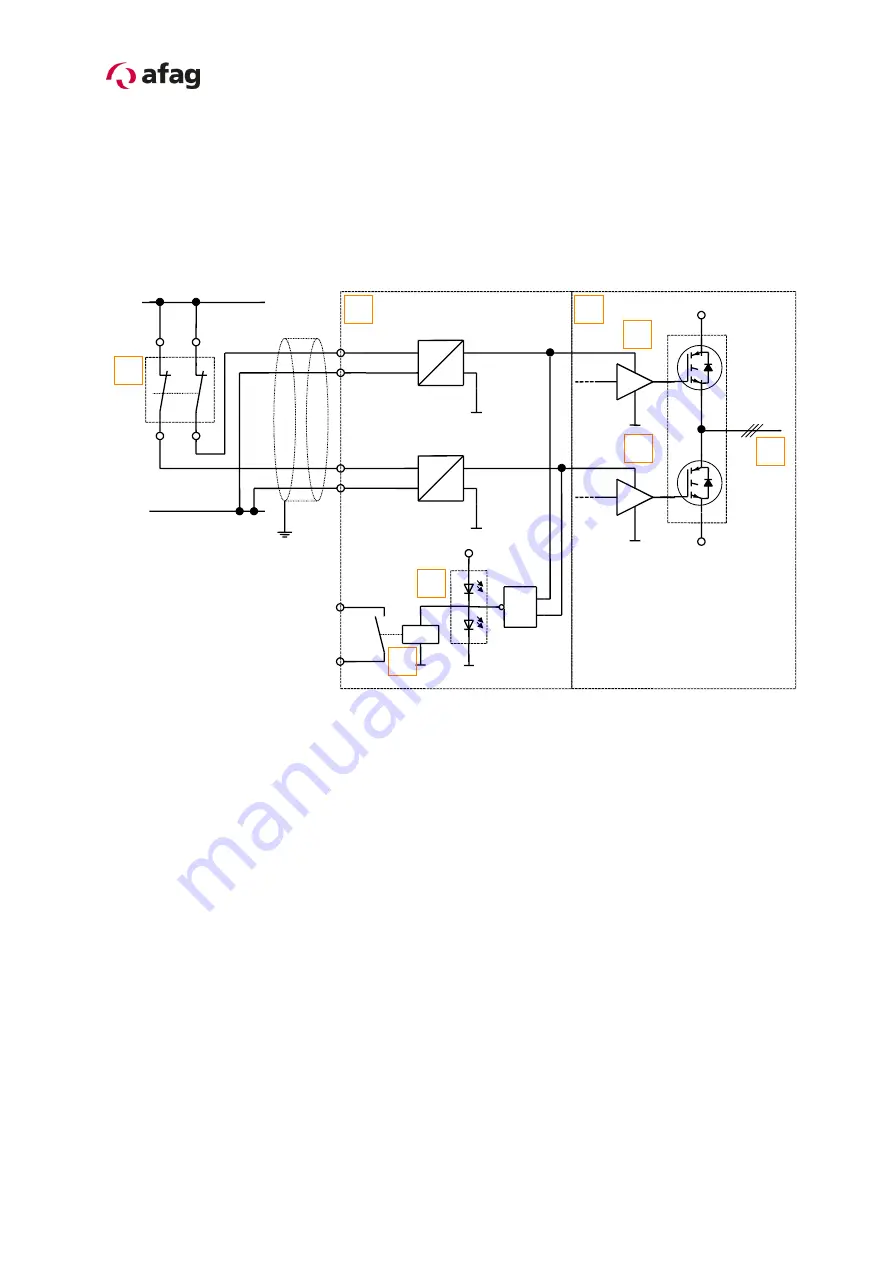
18
SE-Power FS STO-manual vers. 1.6 en.12.08.2015
4.2.1
Description of the safety function STO
Use the function “Safe Torque Off” (STO) whenever you have to reliably disconnect the
energy supply to the motor in your particular application.
The function “Safely Torque Off” switches off the driver supply for the power semiconductor,
thus preventing the power end stage supplying the voltage required by the motor see
1 Safety circuit (switch, relay, safety switching device)
2 SE-Power FS Safety Module STO
3 Power end stage in the SE-Power FS (only one phase illustrated)
4 Driver supply
5 Motor connection
6 LED (green / yellow), status display
7
Feedback contact
Figure 2:
“Safe Torque Off” – Operating principle for the SE-Power FS
0 V
7
4
4
3
5
6
2
1
>=1
DC
DC
STO_A
GND_A
GN
C1
C2
YE
DC
DC
STO_B
GND_B
3x
U, V, W
+VDC
-VDC
+24 VDC