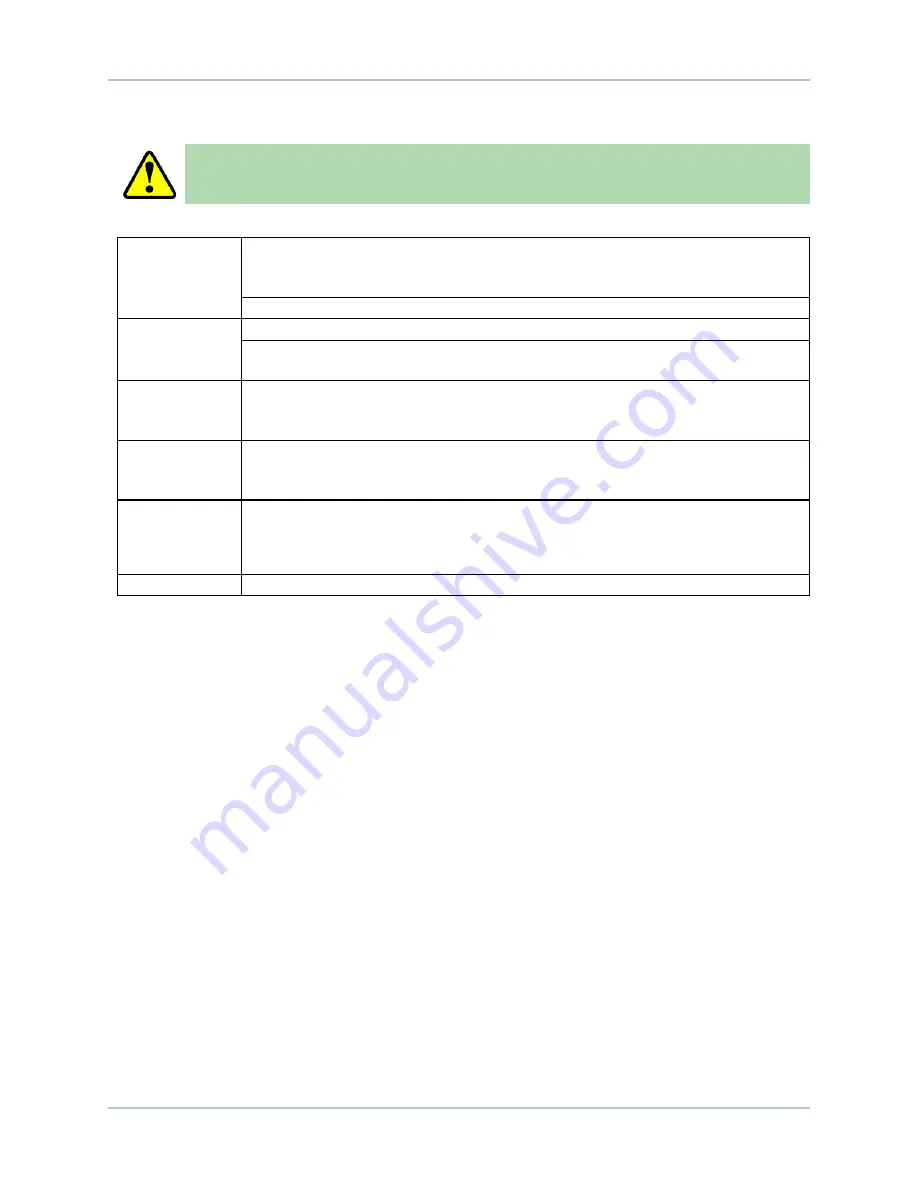
AGR Hardware Manual
Overview
1.1. Environmental Specifications
W A R N I N G : Do not expose this product to environments or conditions outside of the listed
specifications. Exceeding environmental or operating specifications can cause damage to the
equipment.
Table 1-2:
Environmental Specifications
Ambient
Temperature
Operating: 10° to 35° C (50° to 95° F)
The optimal operating temperature is 20° C ±2° C (68° F ±4° F). If at any time the
operating temperature deviates from 20° C degradation in performance could occur.
Storage: 0° to 40° C (32° to 104° F) in original shipping packaging.
Humidity
Operating: 20% to 60% RH
Storage: 10% to 70% RH, non-condensing in original packaging. The stage should be
packaged with desiccant if it is to be stored for an extended time.
Altitude
Operating: 0 m to 2,000 m (0 ft to 6,562 ft) above sea level.
Contact Aerotech if your specific application involves use above 2,000 m or below sea
level.
Vibration
Use the system in a low-vibration environment. Excessive floor or acoustical vibration
can affect system performance. Contact Aerotech for information regarding your
specific application.
Protection
Rating
In their standard configuration, the AGR stages have limited protection against airborne
particles but not water. This equates to an ingress protection rating of IP40.
With the Seal (-SL1) option, the AGR stages have limited protection against dust, but no
protection against water. This equates to an ingress protection rating of IP50.
Use
Indoor use only.
www.aerotech.com
Chapter 1
15