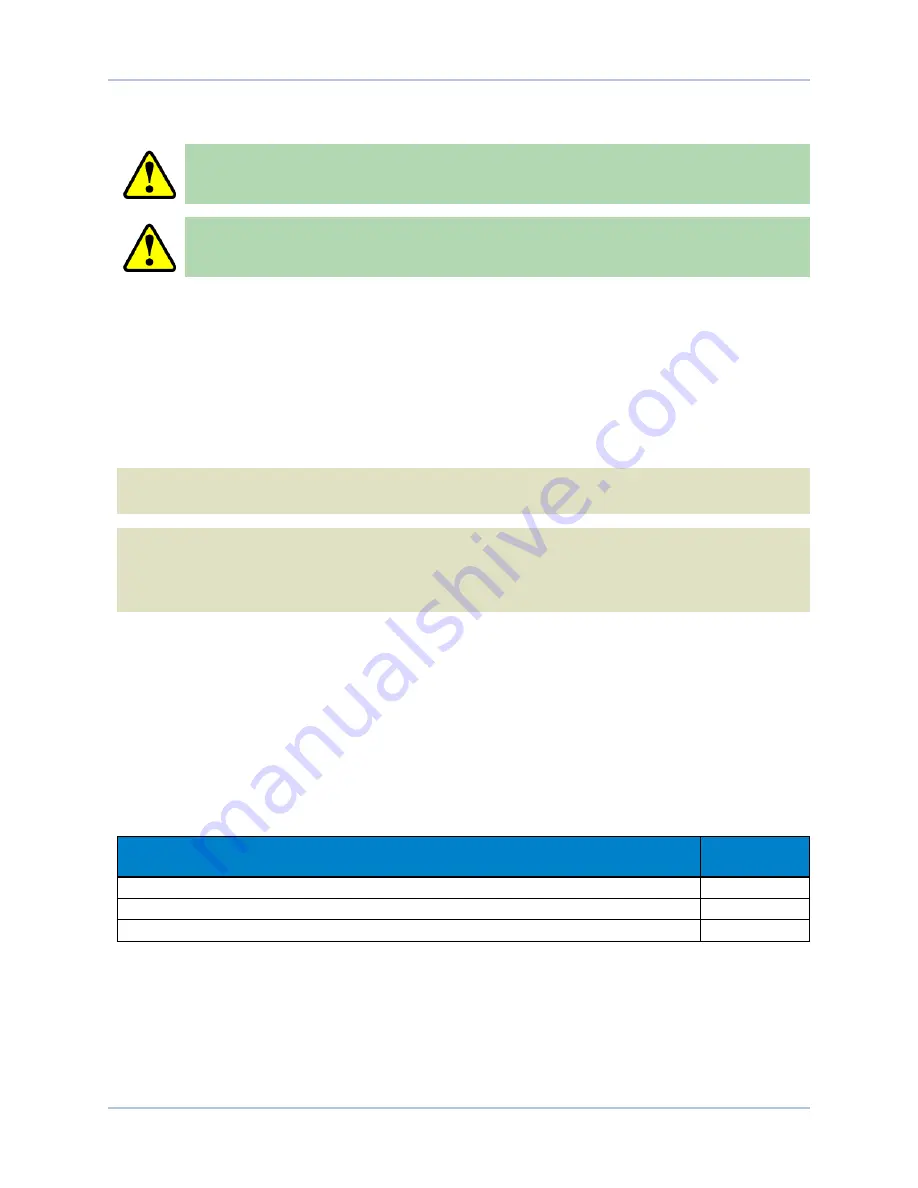
Mechanical Specifications and Installation
AGR Hardware Manual
2.3. Securing the Stage to the Mounting Surface
W A R N I N G : The AGR must be mounted securely. Improper mounting can result in injury and
damage to the equipment.
W A R N I N G : Make sure that all moving parts are secure before moving the AGR. Unsecured
moving parts may shift and cause bodily injury.
The mounting surface must be flat and have adequate stiffness to achieve the maximum performance from
the AGR stage. When it is mounted to a non-flat surface, the stage can be distorted while the mounting
screws are tightened. This distortion will decrease overall accuracy. Adjustments to the mounting surface
must be done before the stage is secured.
Inspect the mounting surface for dirt or unwanted residue and clean if necessary. Use precision flatstones
on the mounting surface to remove any burrs or high spots. Clean the mounting surface with a lint-free cloth
and acetone or isopropyl alcohol and allow the cleaning solvent to completely dry. Gently place the stage on
the mounting surface.
N O T E :
To maintain accuracy, the mounting surface must be flat to within 10 µm over the entire stage
footprint.
N O T E :
The AGR is precision machined and verified for flatness prior to product assembly at the factory.
If machining is required to achieve the desired flatness, it should be performed on the mounting surface
rather than the AGR. Shimming should be avoided if possible. If shimming is required, it should be
minimized to retain maximum rigidity of the system.
AGR series stages have a fixed mounting pattern available to secure the stage to a mounting surface. The
counter-bored mounting holes are designed for 5 mm socket head cap screws (SHCS) for the AGR50 and
AGR75, 6 mm SHCS for the AGR100 and AGR150, and 8 mm SHCS for the AGR200.
AGR series stages also have a fixed mounting pattern on the side of the stage. The size of the side mounting
holes are M5 for the AGR50 and AGR75; M6 for the AGR100 and AGR150; and M8 for the AGR200.
Tightening torque values for the mounting hardware are dependent on the properties of the surface to which
the stage is being mounted. Values provided in
are typical values and may not be accurate for your
mounting surface. Refer to
for specific model mounting locations and dimensions.
Table 2-1:
Stage to Mounting Surface Hardware
Mounting Hardware
Typical Screw
Torque
M5 Socket Head Cap Screw (SHCS)
4.1 N·m
M6 SHCS
7.0 N·m
M8 SHCS
17.0 N·m
30
Chapter 2
www.aerotech.com