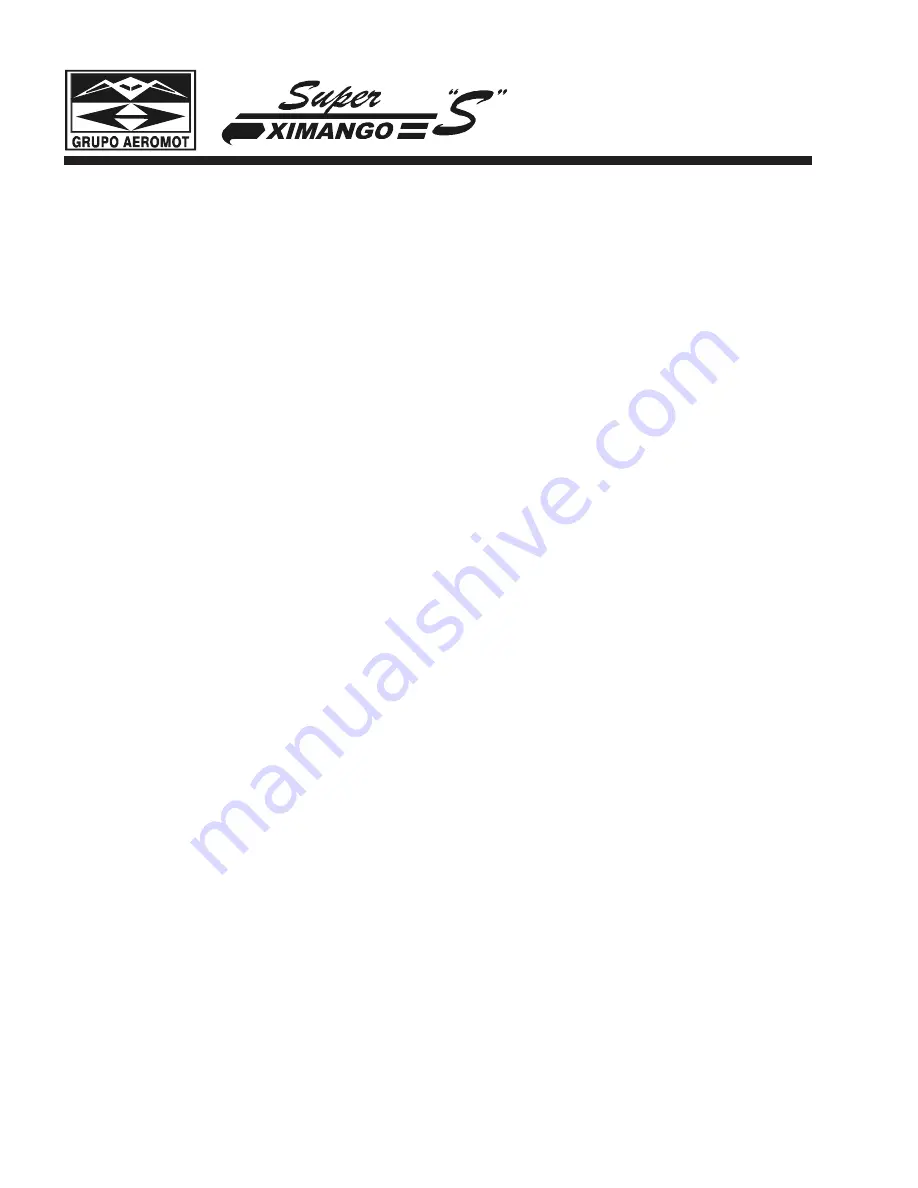
MAINTENANCE MANUAL
AMT 200S
SECTION: 5
MM - 200-25
Page 5.24
August 10, 2004 - Rev. 8
6.3
Corrosion
In case you find signs of corrosion, follow procedures from Section 4.
6.4
Deterioration
Replace rubber and plastic components when superficial cracks start.
6.5
Composite Material Surface Damage
Only repair superficial damage (nicks, scratches, etc.). For larger repairs, contact the
manufacturer or an authorized workshop to repair the damaged areas.
6.6
Anemometric System Obstruction
Check and clean dirty or clogged filter and anemometric hose . Replace filters, as necessary.
In case of water condensing, disconnect instrument hose and use suction to the other end of
the hose.
6.7
External Composite Material Surface Cleaning
Clean composite material surfaces with water and a foam or chamois leather.
Make sure water does not penetrate the anemometric hoses.
Never use silicone products to polish the surfaces.
Never use gasoline, alcohol or solvents, etc.
Protect the aircraft from humidity and heat for extended periods of time.
Repair small cracks according to section 4.
6.8
Torques
Apply the recommended torques on bolts and nuts as specified on items shown in AMT-200S
Parts Catalog.
7. Motorglider Service Life
The motorglider service life corresponds to 3,000 flight hours. The service life can be progressevely
extended to 4,000, 5,000 and 6,000 flight hours if the scheduled inspections described on
BS100-10-021 are performed at authorized workshops. In case you need to extend service life
even more, previous authorization must be obtained from the aeronautical certification authority.
Summary of Contents for AMT 200S SUPER XIMANGO S
Page 1: ...200 25 MAINTENANCE MANUAL AMT 200S...
Page 20: ...MAINTENANCEMANUAL AMT 200S SECTION 1 MM 200 25 Brake System Page 1 19 August 10 2004 Rev 8...
Page 24: ...MAINTENANCEMANUAL AMT 200S SECTION 1 MM 200 25 AileronControls Page 1 23 August 10 2004 Rev 8...
Page 26: ...MAINTENANCEMANUAL AMT 200S SECTION 1 MM 200 25 ElevatorControl Page 1 25 August 10 2004 Rev 8...
Page 28: ...MAINTENANCEMANUAL AMT 200S SECTION 1 MM 200 25 RudderControl Page 1 27 August 10 2004 Rev 8...