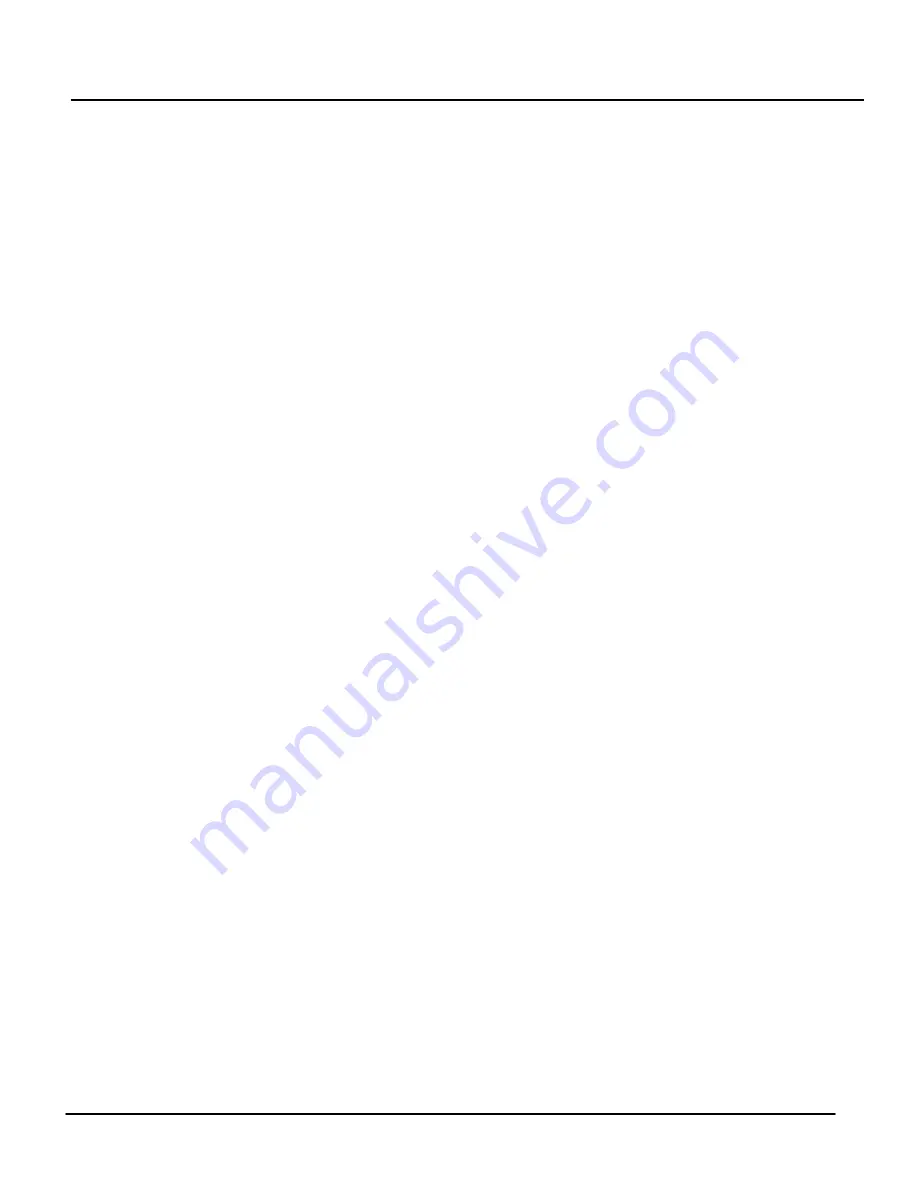
Page
142
of
200
AERCO International, Inc.
•
100 Oritani Dr.
•
Blauvelt, NY 10913
•
Ph.: 800-526-0288
07/21/11
GF-5030
TAG-0044_0A
Gas Supply Design Guide
Disclaimer
The information contained in this manual is subject to change without notice from AERCO International, Inc. AERCO
makes no warranty of any kind with respect to this material, including but not limited to implied warranties of
merchantability and fitness for a particular application. AERCO International is not liable for errors appearing in this
manual. Nor for incidental or consequential damages occurring in connection with the furnishing, performance, or use
of this material.
Pg. 2 of 10
Technical Support:
(Mon–Fri, 8am-5pm EST)
1-800-526-0288
www.aerco.com