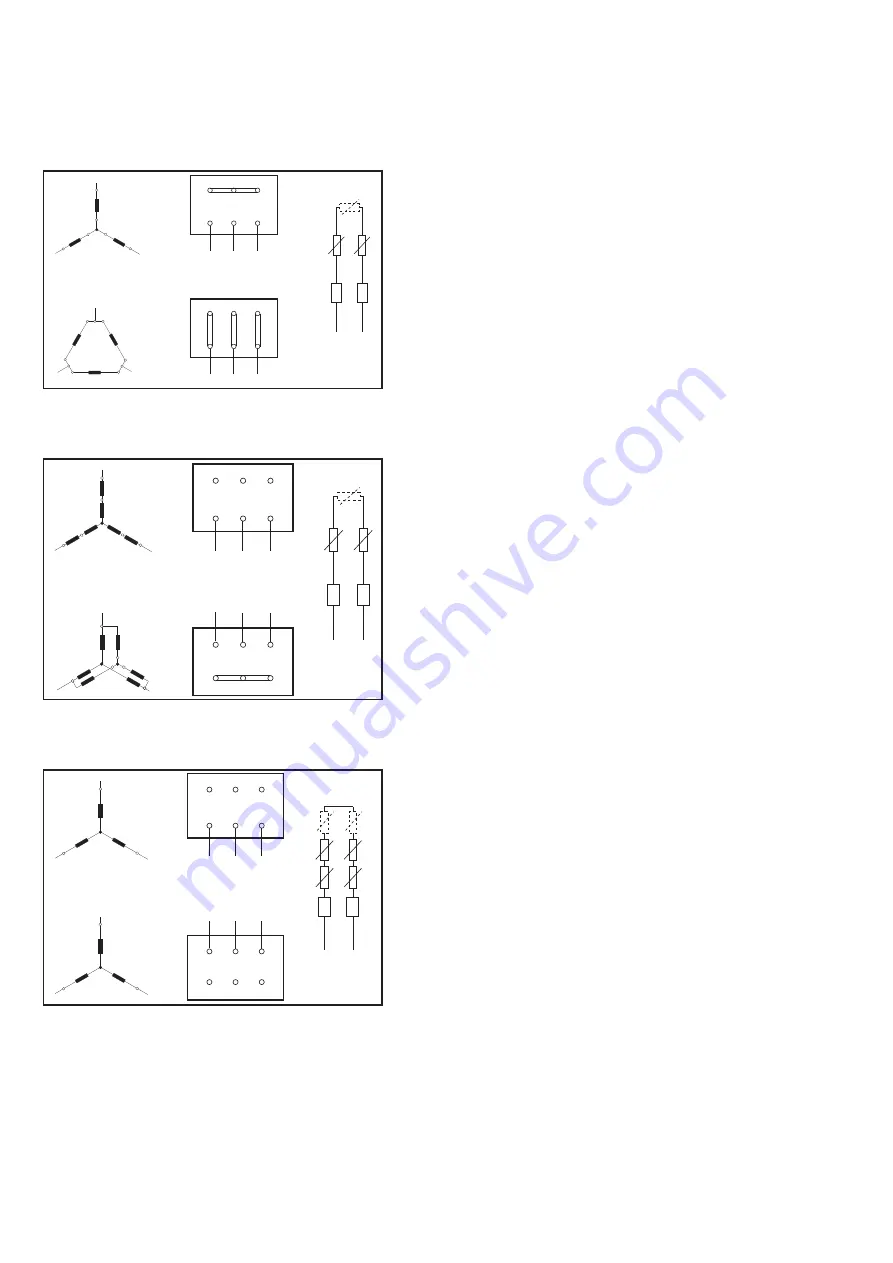
21
Electrical Connection
K
K
W2
U2
V2
U1
V1
W1
L2
L1
L3
W2
U2
V2
U1
V1
W1
L2
L1
L3
L1
U1
W2
L2
L3
V1
V2
U2
W1
L1
U1
W2
L2
L3
V1
V2
U2
W1
*2
*1
2U
2V
2W
1U
1V
1W
L2
L1
L3
2W
2U
2V
1U
1V
1W
L2
L1
L3
K
K
L1
1U
L2
L3
1V
2V
2U
2W
1W
L1
1U
2U
L2
L3
1V
2V
2W
1W
Speed 1:
750 rpm
Speed 2:
1500 rpm
*2
*1
K
K
2U
2V
2W
1U
1V
1W
L2
L1
L3
2W
2U
2V
1U
1V
1W
L2
L1
L3
L1
2U
L2
L3
2V
2W
L1
1U
L2
L3
1V
1W
Speed 1:
1000 rpm
Speed 2:
1500 rpm
*2
*1
Single-speed motor: 1500 rpm, voltage interchangeable
Motor version:
– up to 2.2 kW: 3 x 230 V with Δ connection,
3 x 400 V with Y connection
– above 3 kW: 3 x 400 V with Δ connection,
3 x 690 V with Y connection
2-3 PTC resistor sensors, depending on the size of the
motor
Total resistance R
K
(20 °C) approx. 200-300 Ω
*1 PTC resistor
*2 Full motor protection device
Two-speed motor: 750/1500 rpm Dahlander connection Y/YY
Motor version:
8/4 pole
pole interchangeable
single winding with Dahlander connection Y/YY
2-3 PTC resistor sensors, depending on the size of the
motor
Total resistance R
K
(20°C) approx. 200-300 Ω
*1 PTC resistor
*2 Full motor protection device
Two-speed motor: 1000/1500 rpm separate winding Y/Y
Motor version:
6/4 pole
pole interchangeable
two separate windings Y/Y
4-6 PTC resistor sensors, depending on the size of the
motor
Total resistance R
K
(20°C) approx. 400-600 Ω
*1 PTC resistor
*2 Full motor protection device