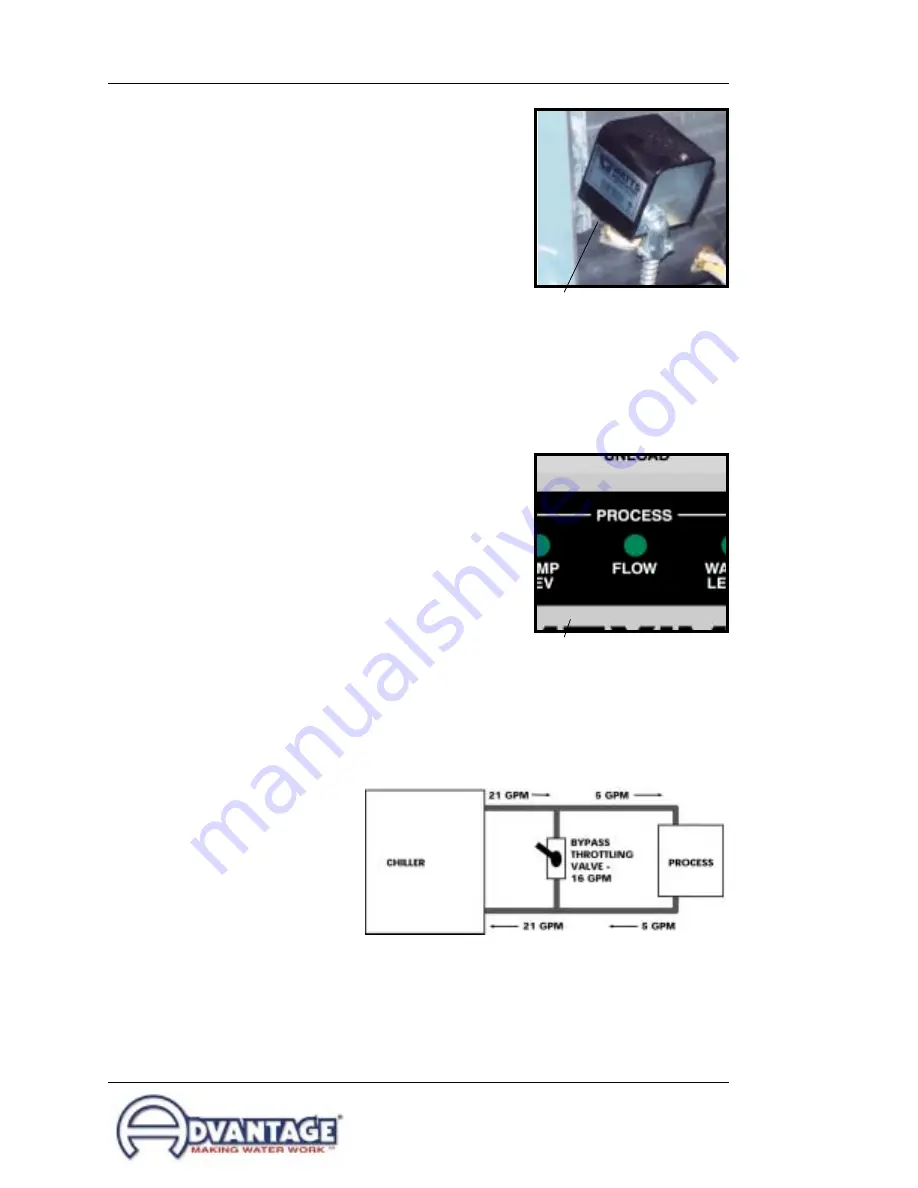
MK Series Portable Chiller : Air-Cooled : HE INSTRUMENT
Page: 22
ADVANTAGE ENGINEERING, INC.
525 East Stop 18 Road Greenwood, Indiana 46142
317-887-0729 Fax: 317-881-1277
Service Department Fax: 317-885-8683
Email: [email protected]
c.
A
low coolant flow
safety switch
is
supplied (figure
3.2F) to stop the
unit if the liquid
flow falls to
approximately 33%
of full flow. This is a
paddle type flow
switch which is
mounted directly in
the water stream.
2.
Press the START key on the display to activate the process
pump. Wait a few moments to allow air to be purge from
system. Observe the COOLANT pressure gauge for steady
readout. Two items the operator for look for are low flow or
excessive flow conditions.
3.
LOW FLOW:
If the LOW
FLOW light (figure 3.2G) is
‘flashing red’ be sure all
process valves are open. If
all process valves are open,
then a low flow condition
exists.
a.
To operate under a
low flow condition,
it is necessary to
install a flow bypass
system in the
process circuitry. This will allow a portion of the
flow to bypass the process and return directly to
the chiller. This keeps the total flow above the
cutoff point. Figure 3.2H illustrates a typical bypass
loop.
b.
Some models may have a factory installed bypass.
Adjust the valve accordingly.
Figure 3.2F
Low flow safety switch
Figure 3.2G
Low flow light
Figure 3.2H Typical low flow by-pass loop
Summary of Contents for Maximum
Page 2: ......
Page 6: ...Page 6 THIS PAGE INTENTIONALLY BLANK ...
Page 44: ...Page 44 THIS PAGE INTENTIONALLY BLANK ...
Page 58: ...Page 58 THIS PAGE INTENTIONALLY BLANK ...
Page 79: ...END 2003 ADVANTAGE ENGINEERING INC RE 1 2 03 ...
Page 80: ......