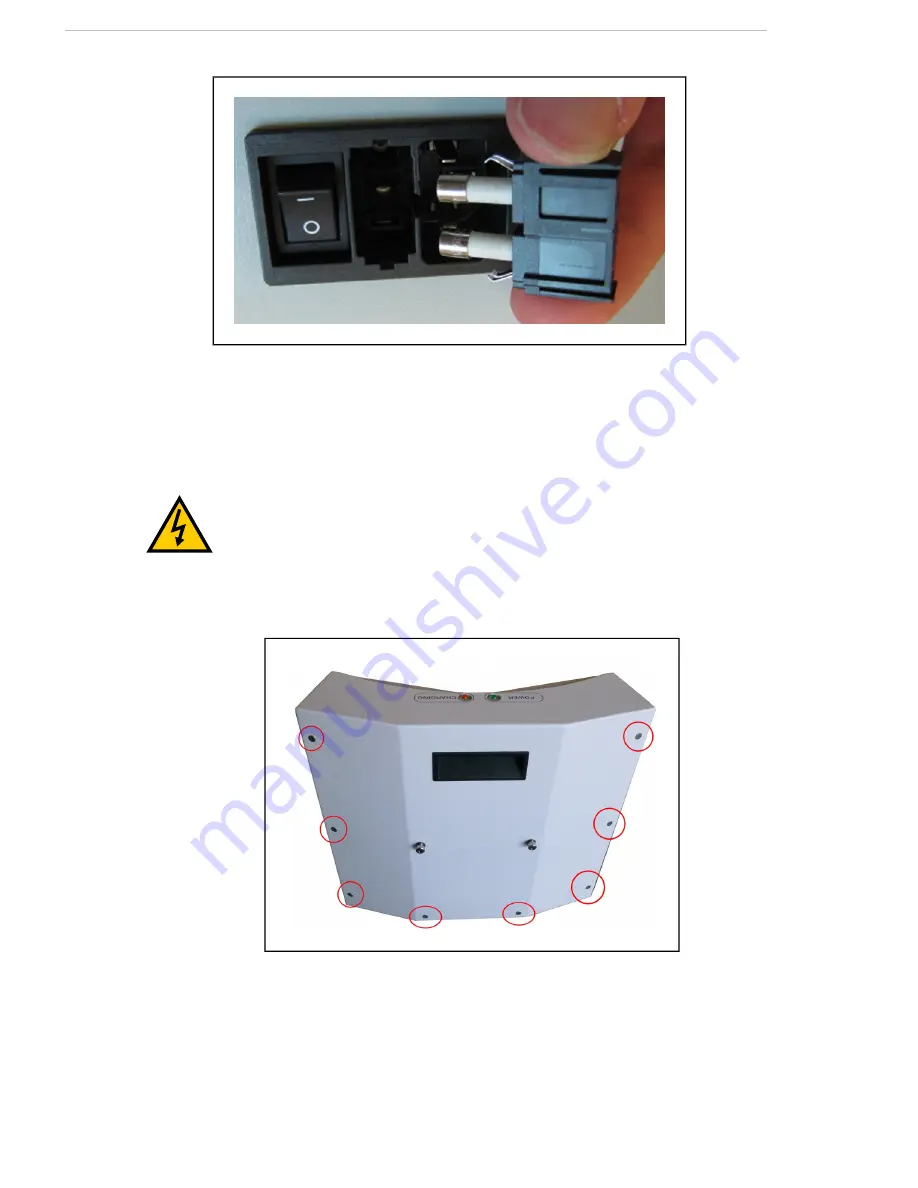
Pioneer LX User's Guide, Rev. A
Page 96 of 125
Chapter 8: Maintenance
Figure 8-10. Charging Station Fuse
Charging Station Internal Fuse
Symptoms: When the charging station is switched on, the blue power light does not come on,
but the charging station can charge a battery manually.
WARNING:
Unplug power from the charging station before starting.
The charging station cover is NOT interlocked. Remove the power cord
at the charger.
1. Remove the ten screws from the back cover of the charging station.
Two of these are on the sides, near the bottom.
Figure 8-11. Charging Station Rear Cover Screws (8 of 10)
Retain the screws for reassembly.
Summary of Contents for Pioneer LX
Page 1: ...User s Guide Rev A November 2013...
Page 16: ......
Page 32: ......
Page 36: ......
Page 48: ......
Page 60: ......
Page 82: ......
Page 108: ......
Page 125: ...10 Colrumbia Drive Amherst NH 03450 USA Phone 1 603 881 7960 www mobilerobots com...