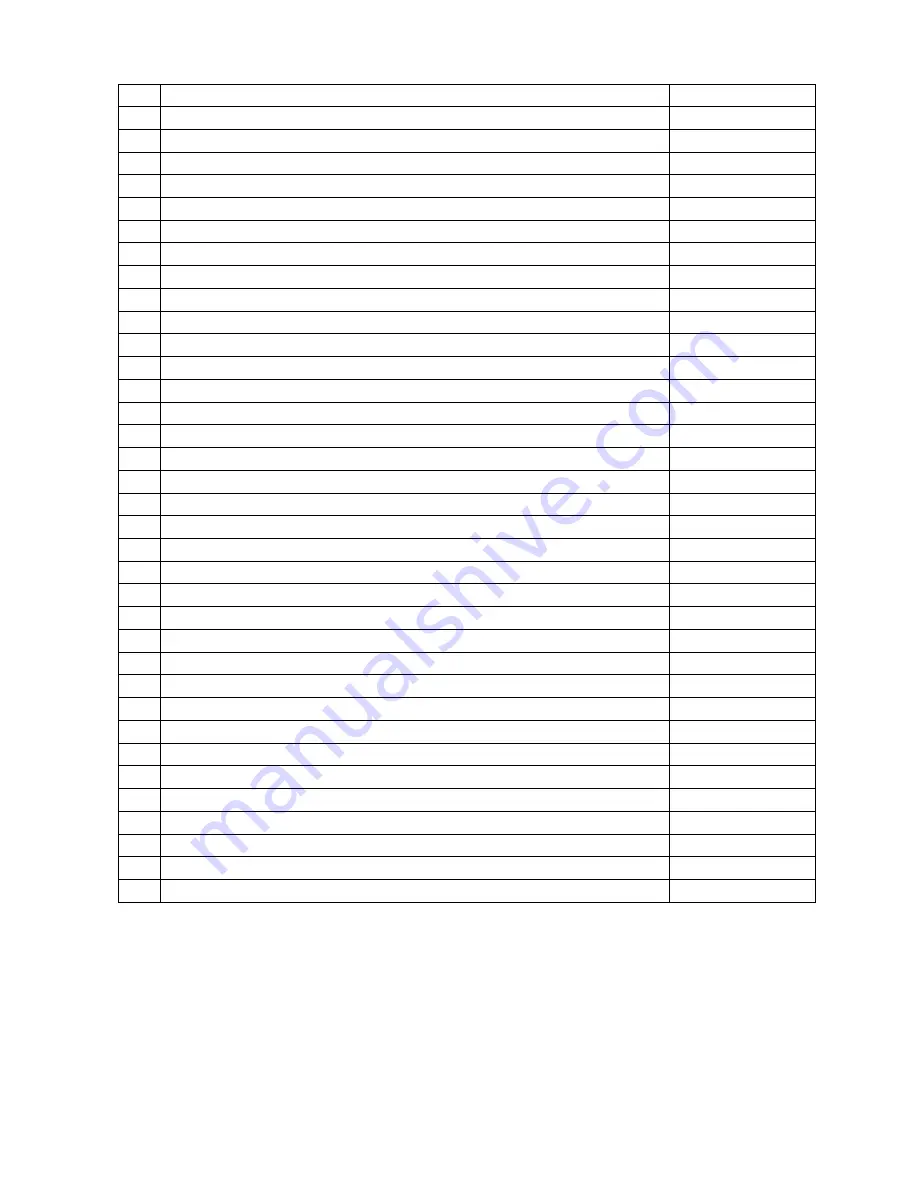
56
RUNWAY ASSEMBLY
No.
Description
Part Number
1
Runway
2
Runway Foot
3
Bump stop
PC5019
4
Cable Carrier – 30 ft.
PC5041-30
Cable Carrier – 40 ft.
PC5041-40
Cable Carrier – 60 ft.
PC5041-60
5
Runway Idler Assembly
SA5042
6
3/8 Flat Washer
7
½ Flat Washer
8
3/8-16 X 1-1/4 Hex Bolt
9
½-13 X 1-1/2 Hex Bolt
10 ½-13 Hex Nut
11
Timing Belt – 30 ft.
PC5027-30
Timing Belt – 40 ft.
PC5027-40
Timing Belt – 60 ft.
PC5027-60
12 Panel Tubing
13 Wire Panel Assembly 56 x 54
SA5134
14 Belt Support Assembly
SA5075
15 Enclosure Assembly
SA5094
16 Runway Drive Assembly
SA5109
17 Bracket Home Sensor
MC5553
18 Brake Plate – 144
MC5531
19 Brake Plate - 130
MC5631
20 Brake Plate - 59
MC5632
21 Glide Stand-off
MC5449
22 Track Glide Bar – Front
MC5626
23 Track Glide Bar – Rear
MC5625
24 Air Supply Assembly
SA5228
25 1-8 Hex Nut
26 3/8-16 X 1 Hex Bolt
27 3/8-16 Hex Nut
28 5/16-18 X 1 Hex Bolt
29 5/16-18 Hex Nut
30 ¼ Flat Washer
31 ¼-20 X 1 Hex Bolt
Summary of Contents for Wood Runner
Page 5: ...5 ...
Page 36: ...36 ...
Page 37: ...37 ...
Page 54: ...54 ...
Page 55: ...55 10 DETAILED PARTS IDENTIFICATION WOOD RUNNER 10 1 RUNWAY ASSEMBLY ...
Page 58: ...58 10 3 RUNWAY DRIVE ASSEMBLY ...
Page 61: ...61 10 5 GANTRY ASSEMBLY ...
Page 62: ...62 GANTRY ASSEMBLY ...
Page 64: ...64 10 6 PICKING HEAD ASSEMBLY ...
Page 65: ...65 PICKING HEAD ASSEMBLY ...
Page 68: ...68 10 7 ELECTRICAL PANEL ASSEMBLY ...
Page 70: ...70 10 8 GANTRY ENCLOSURE ASSEMBLY ...
Page 72: ...72 10 9 CONSOLE ASSEMBLY ...
Page 73: ...73 CONSOLE ASSEMBLY ...
Page 75: ...75 10 10 AIR SUPPLY ASSEMBLY ...
Page 77: ...77 10 11 GANTRY VALVE ASSEMBLY ...
Page 79: ...79 10 12 GANTRY BRAKE ASSEMBLY ...
Page 81: ...81 11 ELECTRICAL DIAGRAMS 11 1 SYSTEM OVERVIEW ...
Page 82: ...82 11 2 MAIN ENCLOSURE LOW VOLTAGE ...
Page 83: ...83 11 3 GANTRY WIRING LOW VOLTAGE ...
Page 84: ...84 11 4 I O CHART ...
Page 85: ...85 11 5 INFEED WIRING LOW VOLTAGE ...
Page 86: ...86 11 6 OPERATORS CONSOLE ...
Page 87: ...87 11 7 MAIN ENCLOSURE HIGH VOLTAGE ...
Page 88: ...88 11 8 MAIN ENCLOSURE RECEPTACLE WIRING ...
Page 89: ...89 11 9 SAFETY CIRCUIT LAYOUT ...
Page 90: ...90 11 10 SAFETY CIRCUIT DIAGRAM ...
Page 91: ...91 11 11 BRAKE SENSOR DIAGNOSIS ...
Page 92: ...92 12 PNEUMATIC DIAGRAMS 12 1 SINGLE HEAD GANTRY ...
Page 93: ...93 12 2 DOUBLE HEAD GANTRY ...
Page 94: ...94 12 3 INFEED DECK ...