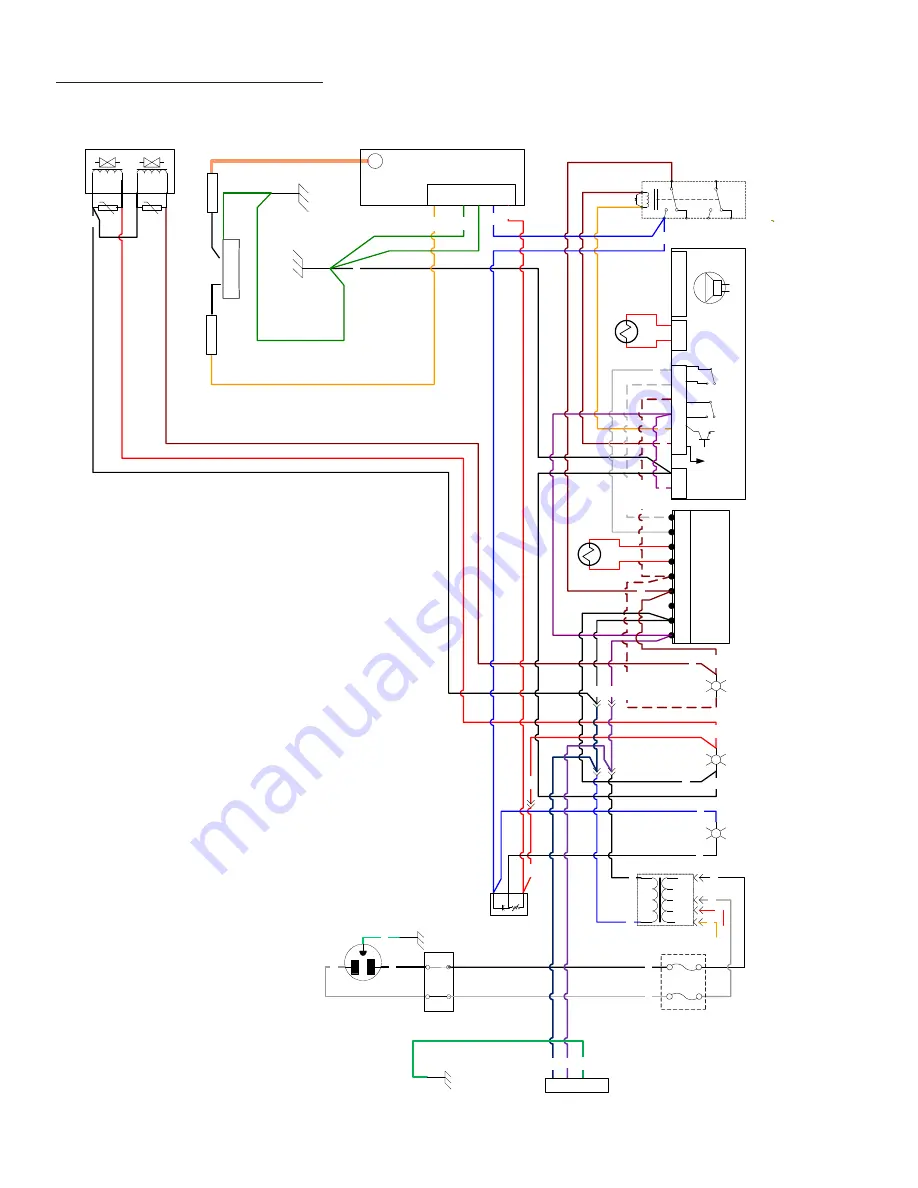
Accu-Steam™ G2 Gas Service Manual
31
SP8042-1911
S
C
H
E
M
A
T
IC,
G
2
G
R
IDDL
E
F
o
rt
W
ayn
e,
I
N
46
8
25
AT2T-3912
-1 Rev A
8
4
1
5
N
.
C
lin
to
n
P
a
rk
A
ccu
T
em
p
P
ro
d
u
ct
s,
I
n
c.
AT2T-3912-1
120V-240V
ACCU-STEAM G2 GAS
GRIDDLE
YEL
O
RN
BR
N
VI
O
B
RN
YEL
B
LU
YEL
B
LU
R
ED
OR
N
YEL
10
0
O
P
RT
D
10
00O
P
RT
D
N
.O
.
N
.C
.
C
OM
7
4
1
N.
O
.
N.
C.
C
OM
8
5
2
3
6
R
L
Y
2
D
C
CO
IL
B
RN
W
HT
/G
RA
Y
GR
Y
WH
T/B
R
N
W
HT
/B
RN
O
VER
T
E
MP
VI
O
L
1
L
2
N
.C
.
N
.O
.
C
O
M
*R
T
D
*
R
E
S
E
T
H
IG
H
L
IM
IT
CO
NT
RO
L
L
E
R
Y
EL
BR
N
Z
R
1
38V
Z
R
2
38V
PV
MV
G
A
S
VA
L
VE
1
2
3
4
5
6
SP
AR
K
M
O
DUL
E
G
RN
H
V
IG
N
IT
O
R
B
U
RNE
R
BL
K
W
HT
G
RN
2
1
W
HT
BL
K
RE
D
Y
EL
B
LU
H
EA
T
RE
D
RE
D
B
LK
W
HT
24
0V
20
8V
1
20V
CO
M
24V
RE
D
OR
N
.7
5
A
F2
.7
5
A
F1
IG
N
F
A
U
L
T
B
LU
W
HT
F
A
U
L
T
T
IM
ER
1
2
3
1
2
J2
PO
W
ER
IN
P
UT
D
IGI
TAL
CO
NT
R
O
L
L
E
R
ON
/
O
FF
1
2
3
4
5
6
J7
+
24
V
GN
D
1
2
J3
SE
N
SO
R
INP
U
T
1
2
3
4
5
ISSP
YEL
VI
O
G
RN
1
2
J
1
3
4
O
PT
IO
N
AL
R
E
M
O
T
E
T
IM
E
R
AT0A-2779-5
TRANSFORMER ASSEMBLY
AT0E-3625-5 Control Board
AT0E-3880-1
HI-LIMIT CONTROL
AT0E-2825-6
Relay, DC
AT0E-1800-2 PILOT LAMP, RED
AT2E-1807-1
IGNITION CONTOL MODULE
AT2E-4717-1
FLAME SENSE PROBE
AT2E-4716-1
IGNITOR
AT2E-1806-2 NG
CONTROL
VALVE
AT2E-1806-
3
PROPANE CONTROL VALVE
AT0E-2885-7
HI-LIMIT SENSOR
AT0E-2885-
8
TEMPERATURE
SENSOR
AT0A-2911-1
AC POWER CORD ASSEMBLY
AT0E-2500-3
TIME DELAY RELAY
AT2B-2099-2
36"& 48" BURNER
AT2B-2
131
-2
24"
BURNER
10. Wiring Schematic
Summary of Contents for Accu-Steam G2 Series
Page 34: ......