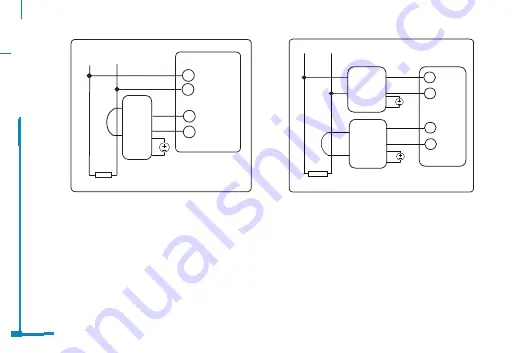
22
AcuDC 210/220 Series
Fig 2.17 Voltage and Current input with
Hall Effect Sensors
5
6
AcuDC
210/220
Cur
ren
t Hall
Eff
ec
t S
ensor
Voltage Hall Effect Sensor
Load
Vdc+ Vdc-
7
8
V-
V+
I -
I+
Input
Output
Output
External DC
Power
External DC Power
+
+
_
_
+
_
5
Load
AcuDC 210/220
Current Hall
Effect Sensor
Vdc+
Vdc-
8
6
7
V-
V+
I -
I+
Output
External
DC Power
_
+
Fig 2.16 Voltage and Current input with
Hall Effect Sensor