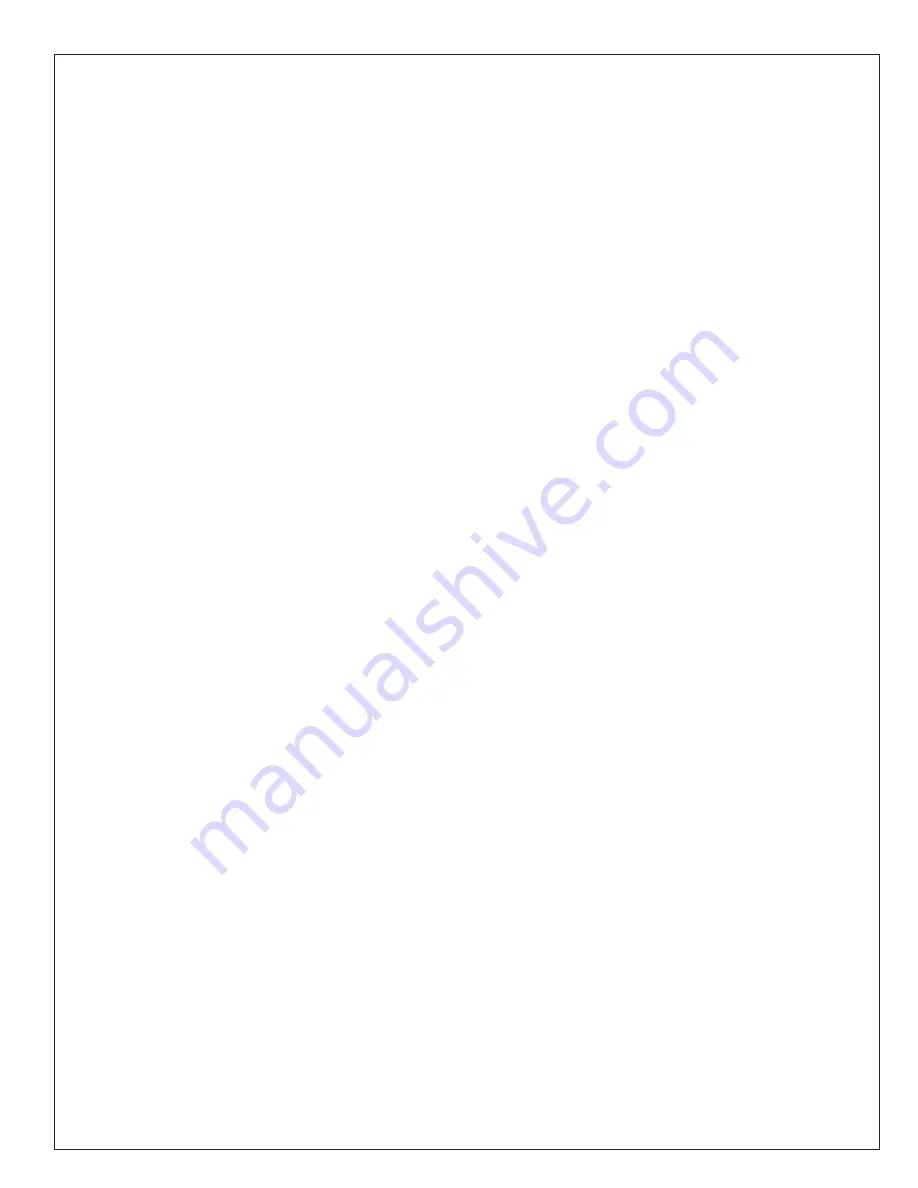
29
TROUBLESHOOTING (Continued)
TRAVERSING
--POSSIBLE CAUSE--
--REMEDY--
--REASON--
--PROBLEM--
A--Bearing shaft support
blocks are not perpendicular to
carriage shaft.
B--Drive shaft is bent.
C--DC drive motor shaft not
concentric to drive shaft.
Actuator drive
shaft whipping
excessively at
high traverse
speed.
Misalignment of shaft
support blocks to carriage
traverse rod causes a bow
in the rod. This bow will
cause an out of balance
which in turn will cause it to
whip at high traverse
speeds.
Excessive bend in the shaft
will cause the shaft to whip
at high traverse speeds.
Side load at the shaft end
will bend the shaft and
cause it to whip at high
speed traversing.
Loosen the screws that retain
the shaft support blocks on
each end of the actuator shaft.
Use a square to align bearing
face 90 degrees to the front
rail and holding the actuator
shaft to the front rail to 3.375
dimension. (For more detail,
see align front rail and drive
shaft in the adjustment section
in the manual.
Turn the actuator screw
clockwise 1/4 to 1/2 turn to
release actuator from the drive
shaft. Slide the carriage to
one end of the machine.
Mount indicator in the middle
of the two bearing support
blocks. Check for a maximum
of .015 indicator reading when
you rotate the shaft. Replace
shaft if required. NOTE: Item
A above must be done proper
to this step.
Loosen two bolts holding the
motor. Align the motor shaft
concentric to the drive shaft.
See if coupling spiral gaps are
equally spaced when re-
aligned. (For more detail, see
Traverse Motor Coupling in the
adjustment section.)
Summary of Contents for 670
Page 36: ...36 ELECTRIC SCHEMATIC 67095233 ...
Page 38: ...38 PARTS LIST 6709534 MAIN BASE ASSEMBLY ...
Page 40: ...40 PARTS LIST Continued 6609529 GRINDING HEAD ASSEMBLY ...
Page 42: ...42 PARTS LIST Continued 6709531 TRAVERSE CARRIAGE ASSEMBLY ...
Page 44: ...44 PARTS LIST Continued 6709533 BEDKNIFE SUPPORT ASSEMBLY ...
Page 46: ...46 PARTS LIST Continued 6709536 CONTROL PANEL ASSEMBLY 50 ...
Page 48: ...48 PARTS LIST Continued 6709536 ELECTRICAL ASSEMBLY ...
Page 50: ...50 PARTS LIST Continued 3708784 COOLANT PUMP TANKASSEMBLY 15 ...
Page 52: ...52 ...