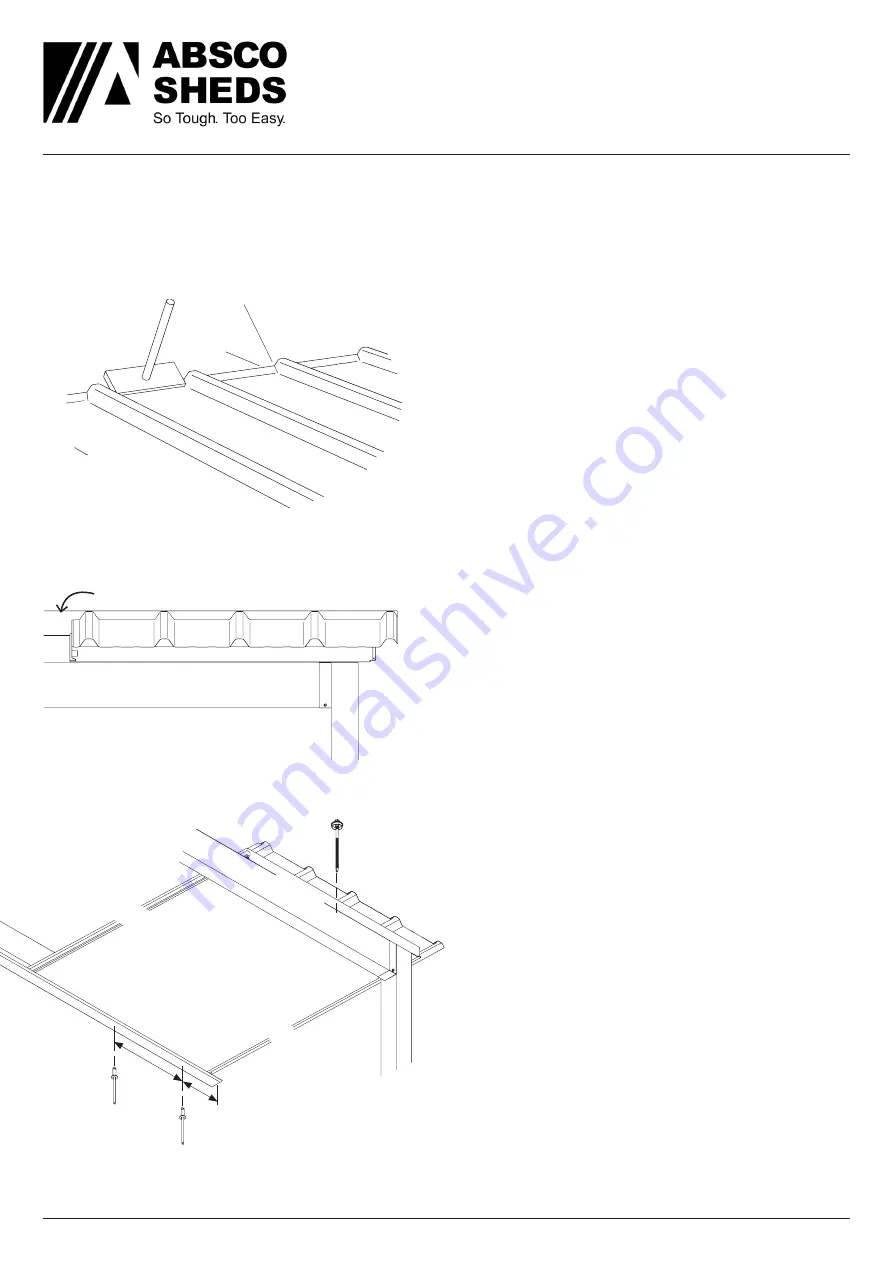
Absco Industries
Assembly Instruction Manual
ABSCO SIGNATURE PATIO
MODEL: ADPATIO6030
6.12m W x 3.11m D x up to 3.18m H
Model: ADPATIO6030
21/09/23
1.0
9
FRONT VIEW - Aligning the first roof panel
Preparing the
AD1
panels using a tool before
inserting into receiver channel.
ROOF PANEL
FLUSH
1
Beam
Beam
Receiver channel
Post
Post
2
FLUSH
UNDERSIDE VIEW
Bottom skin
150
300
3
4
15
o
C
The end with ‘top skin’ overhang & sticker must
go to the front.
The other end goes into the receiver channel and
requires some preparation.
A. Check the foam core is flush with the top and
bottom skins. If it bulges out, safely trim flush with
a Stanley knife.
B. Check if the steel ‘Bottom skin’ corner is bent
down below the bottom face. Bend it up with
pliers.
C. To increase weather protection turn up the
pans 15 degrees with a turn up/down tool or
equivalent as shown
Familiarize yourself with the weight and orientation
of the
AD1
panel before lifting.
The ‘bottom skin’ has a protective plastic coating,
this can be peeled off just before lifting.
Remember to lift and place
do not slide
, this can
scratch the panel.
1.
Safely position the first panel on top of the
beam and insert into the receiver channel - all the
way to the right.
The steel ‘top skin’ edge will be flush with right
end of the receiver channel as shown.
2.
Check the beam for alignment, the roof panel
bottom skin is to be flush with the exterior side of
the beam as shown.
3.
For now
fix the
AD1
panel to the receiver panel
from below with two 4mm pop rivets
FAST102.
Inset 150 mm from the right and another 300 mm
further along.
4.
Fasten the front edge of the roof panel to
beam with a tek 14 x 125 mm
FAST104
through
the centre-most rib.
Don’t over-tighten and crush the panel.
For further screw position detail see page 11.