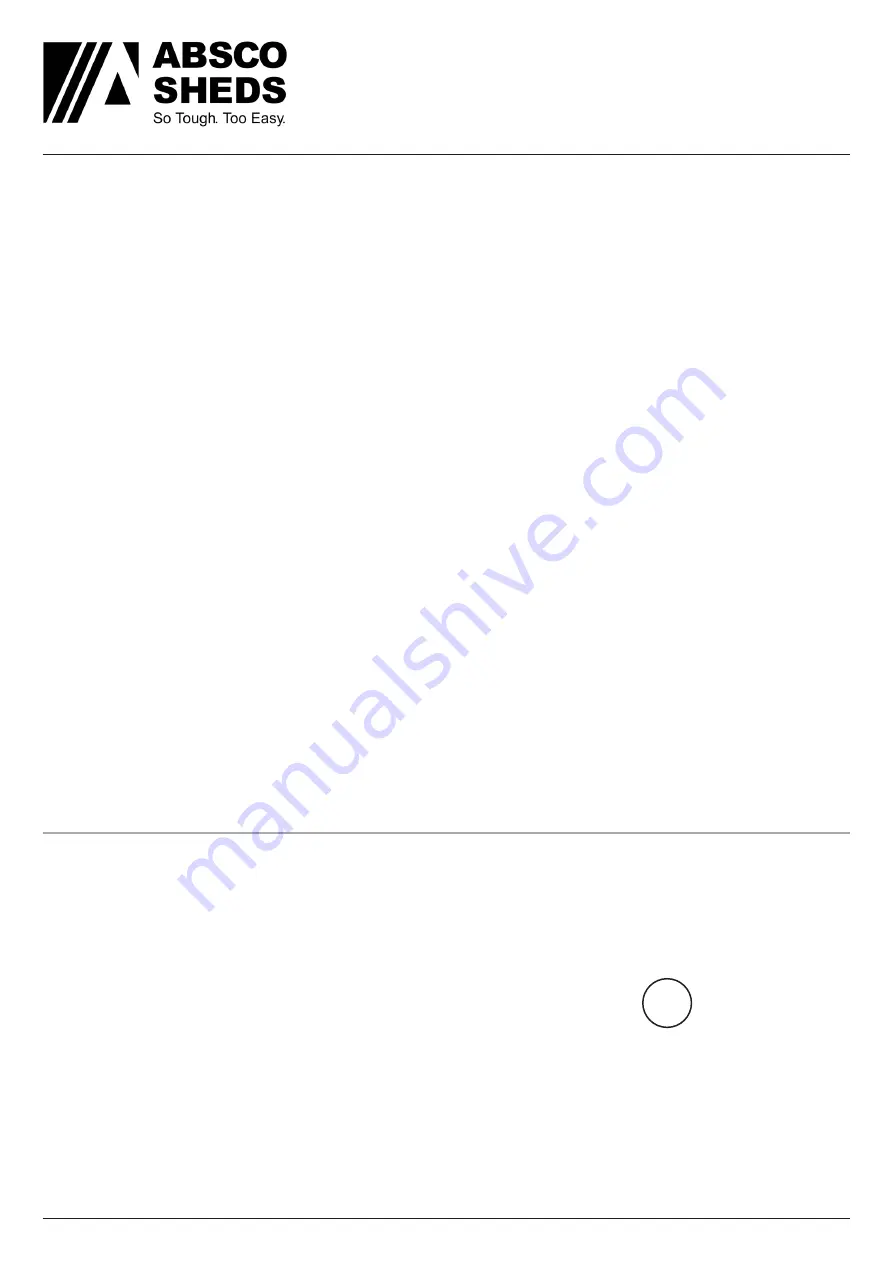
Absco Industries
Assembly Instruction Manual
ABSCO SIGNATURE PATIO
MODEL: ADPATIO6030
6.12m W x 3.11m D x up to 3.18m H
Model: ADPATIO6030
21/09/23
1.0
2
IMPORTANT INFO - READ BEFORE CONSTRUCTION BEGINS
understanding of assembly
methods and associated details.
4. Unpack and carefully identify
and check off all the parts
against the parts described and
illustrated on “Components
List” page.
If you are missing anything do
not begin, contact Absco.
5. The structure shall be
erected on top of suitable
foundations and anchored down
appropriately.
The site for the structure must
be level. An uneven surface may
result in misalignment of parts.
6. Region specific: If required,
you have approval for the
structure. If unsure, seek advice
from relevant local authorities.
7. Some parts may have sharp
edges. It is recommended to
wear gloves when handling
items and safety glasses when
drilling holes. Sensible shoes
are highly recommended.
Minimum two people are
required to easily lift and align
assemblies.
8. Consider the weather and do
not build in windy conditions.
If the structure must be left for
a period of time uncompleted
it must be made safe to prevent
damage.
TOOLS REQUIRED
Use as a guide, other tools/equipment may be suitable. Safely work within your ability.
Please wear recommended
PPE for any tool used during
construction
!
1. Awnings are typically
attached to a fascia board
(beneath the gutter), or to a
wall.
The space required on the
existing structure for receiver
channel is 90 mm x 6125 mm
Max attachment height is 3180
mm - measured from foundation
to top of receiver channel
2. Fixing method is dependent
on material type and location.
This kit contains typical fasteners
for timber and steel fascia as
well as brick walls.
3. Information provided in this
manual regarding “existing
structure” is to be used as a guide
only, it is your responsibility that
connection detail is compliant
with applicable building codes.
Read through these instructions
in detail to gain a thorough
• 4mm drill bit
• 5/16” & 3/8” nut setter
• 12mm masonry drill bit
• Chuck drill
• Impact drill driver
• Hammer drill
• 8m tape measure (2 required)
• Caulking gun
• 16mm socket
• 1.8m ladder (2 required)
• Plumb bob
• Visegrips or clamps
• Pop riveter
• Stanley knife
• Masking tape
• Spirit level
• Angle grinder
• Marker
• Ruler
• Square
• String line
• 70mm hole saw
• Tin snips