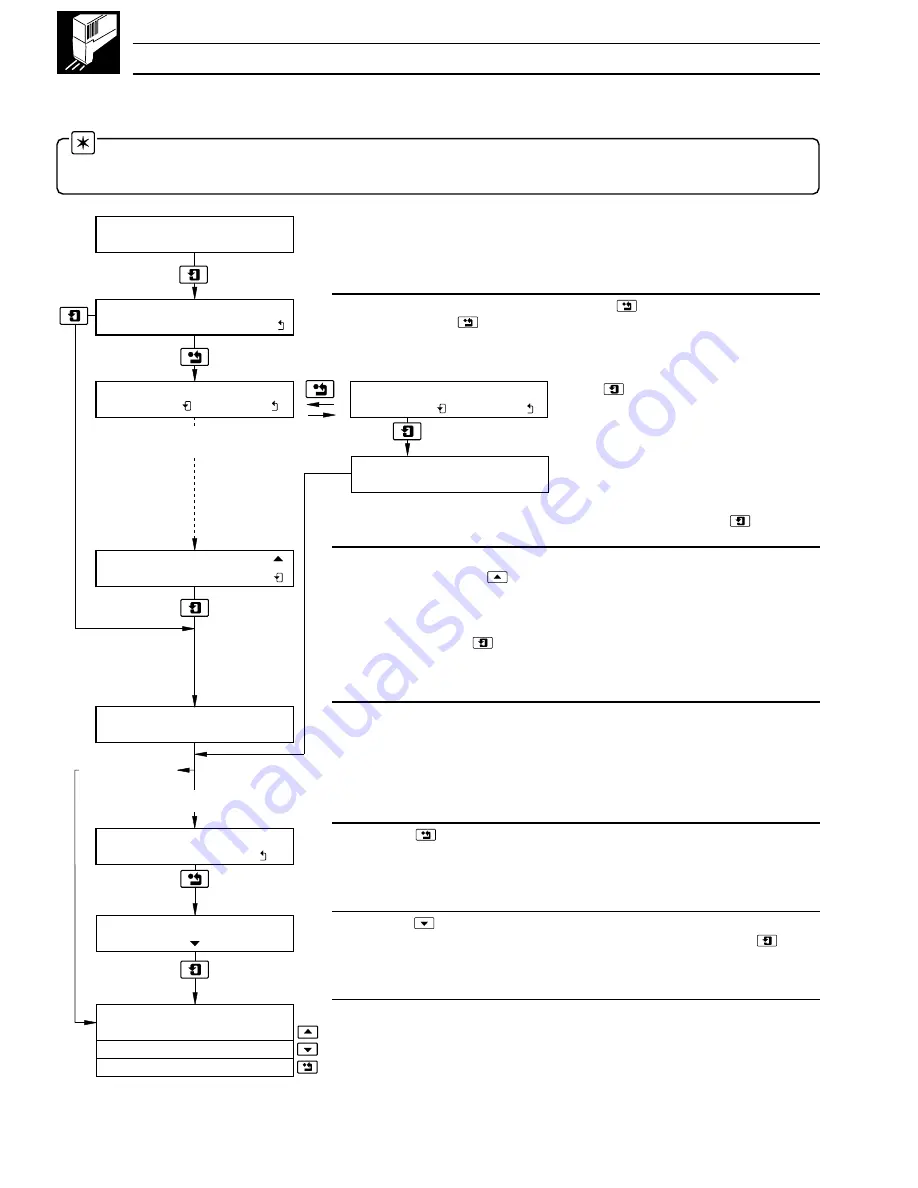
4
…1
CHARTS AND PENS
…1.1
Loading a Roll Chart – Fig. 1.2
Select the
Load Chart Page
– see Fig. 1.1.
Note. If automatic chart rewind has been enabled in the
Chart Control Configuration Page
(see Section 3.4.1), when the
chart remaining counter reaches
0
the chart will begin rewinding automatically and the instrument display will show the
REWINDING XXX%
frame.
If an old chart is to be removed, press the
key to start rewind. To pause
rewind press the
key again.
If the
key is pressed whilst rewind is
paused
, rewind is aborted, the chart returns
to its previous position and the instrument
resumes recording.
This frame is displayed momentarily if
rewind is aborted.
If all of the chart is rewound before the motor stops, press the
key.
When rewind is complete there may still be some chart left to be rewound. If this
is the case, press the
key until all remaining chart is rewound.
Remove the old chart and load the new chart – see Fig. 1.2 (refer to Section 6,
Spares List for part numbers). When a new chart is fitted and the cassette is
replaced, press the
key. The chart moves forward approximately 30mm to
take up any slack.
This frame is displayed momentarily when chart loading is complete.
When the
key is pressed, recording ceases and the chart stops.
The print head moves from side to side printing at the 40% and 60% positions
on the chart to enable adjustment onto the time line.
Press the
key to move chart to the correct position to allow printing of time
to correspond to major time lines. Recording resumes when the
key is
pressed.
Select one of three pre-defined chart speeds. The values shown are the
Company standard settings.
LOAD CHART
PAGE
TO START RELOAD
PRESS ENTER
REWINDING XXX%
REWIND PAUSED
Frame advances automatically
when rewind complete
(STOP ) (PAUSE )
(ABORT )(RESUME )
FOR ADVANCE TO TIME
LINE PRESS ENTER
ADVANCE TO CORRECT
TIME LINE
SELECT CHART SPEED
SPEED 1: Omm/h
SPEED 2: 2Omm/h
SPEED 3: 12Omm/h
Time Line Advance
ON
XX.Xm CHART LOADED
XX.Xm REMAINING
Time Line Advance
OFF
REWIND ABORTED
REWOUND (MORE )
LOAD NEW ABB CHART