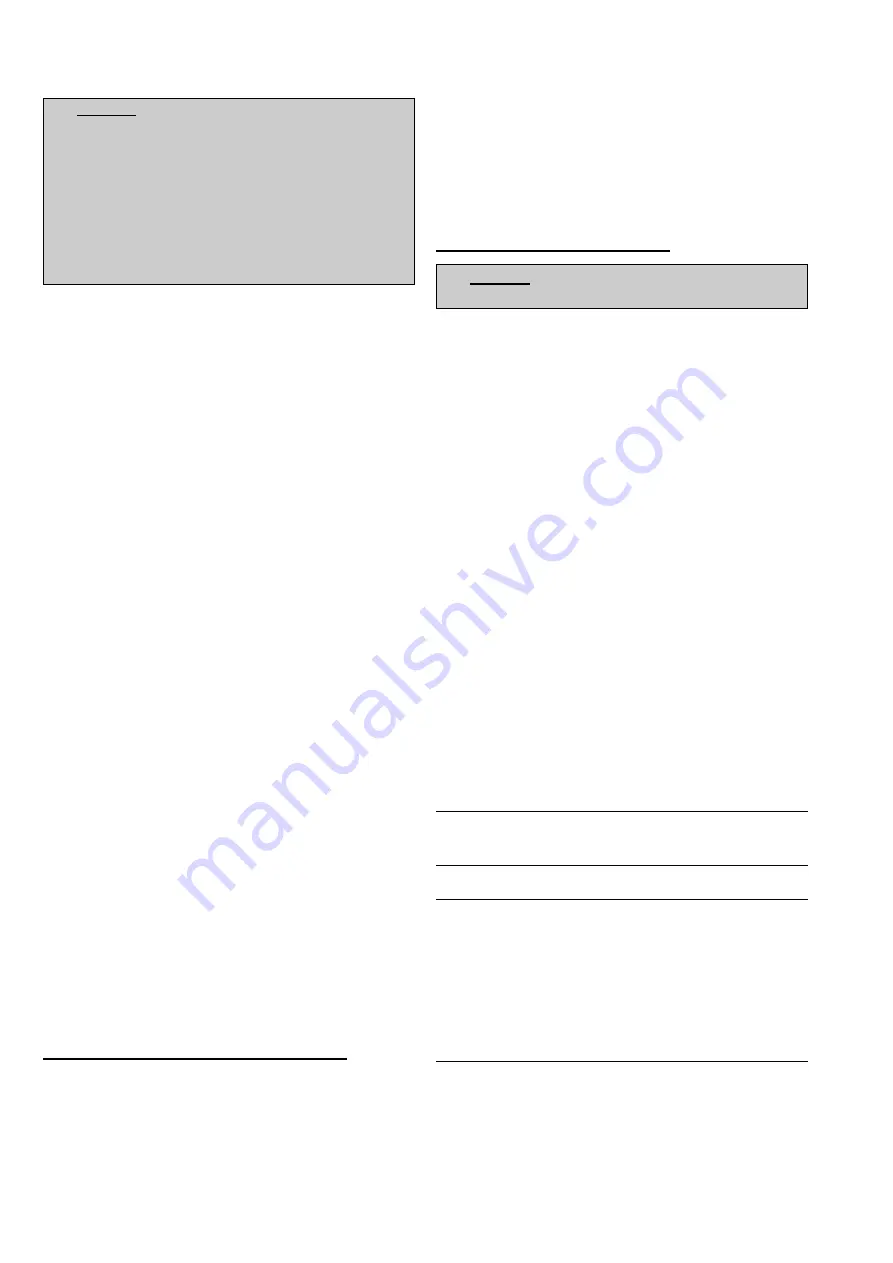
Maintenance and lubrication
Warning
Standards relating to connection and use of
electrical apparatus in hazardous areas must be
taken into consideration. Only trained personnel
fully acquainted with such standards must handle
this type of apparatus.
Depending on the nature of the work in question,
disconnect and lock out before working on motor
or driven equipment. Ensure no explosive gas or
dust is present while work is in progress.
General inspection
1.
Inspect the motor at regular intervals. The regular-
ity of checks depends on the humidity level of the
ambient air, and on the local weather conditions.
This can initially be determined experimentally and
must then be strictly adhered to.
2.
Keep the motor clean and ensure free ventilation
airflow. If the motor is used in a dusty environment,
the ventilation system must be regularly checked
and cleaned. For DIP motors respect the environ-
ment specifications stated in standard EN 50281-
1-2.
3.
Check the condition of shaft seals (for example V-
ring or radial seal) and replace if necessary.
For D.I.P. motors the shaft seals should be
changed at least once a year depending of envi-
ronment conditions as mentioned above(1).
4.
Check the condition of connections and mounting
and assembly bolts.
5.
Check the bearing condition by listening for unu-
sual noise, vibration measurement, bearing tem-
perature, inspection of spent grease or SPM
bearing monitoring.
When signs of wear are noticed, dismantle the motor,
check the parts and replace if necessary. When bear-
ings are changed on D.I.P. motors, replacement bear-
ings must be of the same type as those originally fitted.
The shaft seals have to be replaced when changing
bearing; with seals of same quality and characteristics
as the original ones.
For flameproof motors, periodically turn the knurled
head of the drain plug, if equipped, in order to prevent
jamming. This operation must be done when the motor
is at standstill. The regularity of checks depends on the
humidity level of the ambient air, and on the local
weather conditions. This can initially be determined
experimentally and must then be strictly adhered to.
Lubrication
Bearing types are specified in the respective product
catalogues. On motors size 160 and larger, the bearing
type is indicated on the rating plate.
Motors with permanently greased bearings
Motors up to frame size 180 are normally fitted with
permanently greased bearings of either 1Z or 2Z types.
As a guide, adequate lubrication can be achieved for
the following duration, according to L1 at ambient
temperature of 25°C.
32 000 - 45 000 duty hours for 4 pole machines.
1)
16 000 - 26 000 duty hours for 2 and 2/4 pole
machines.
1)
The shorter times are valid for larger frame sizes.
1)
Depending on application and load conditions, see
applicable product catalogue.
Hours of operation for vertical motors are half of the
above values.
Motors with relubrication system
Warning
Beware of all rotating parts.
Relubrication procedure:
-
Remove grease outlet plug if fitted.
-
Press fresh grease into the bearing until all old
grease has been forced out.
-
Let the motor run 1-2 hours to ensure that all
excess grease is forced out of the bearing. Close
the grease outlet plug if fitted.
Regrease motors while running. If this is not possible,
lubrication can be carried out while the motor is at a
standstill. In this case, use only half the quantity of
grease, then run the motor for a few minutes at full
speed. When the motor has stopped, the remaining
quantity of grease can then be forced in until the old
grease has been replaced.
After 1-2 running hours, close the grease outlet plug (if
fitted).
The grease outlet plug must be removed permanently
with automatic lubrication.
If the motor is fitted with a lubrication information plate,
follow the values given; otherwise use the values in the
table below.
ABB Motors policy is to have reliability as a vital issue
in bearing lubrication intervals. That is why we follow
the L1-principle (meaning that 99% of the motors are
sure to make the interval time). According to the L1
principle, the lubrication intervals are as follows:
Frame Amount
3600
3000
1800
1500
1000
500-900
size
of grease
r/min
r/min
r/min
r/min
r/min
r/min
g/bearing
Ball bearings
Lubrication intervals in duty hours
112 10
10000 13000 18000 21000 25000 28000
132 15
9000
11000 17000 19000 23000 26500
160 25
7000
9500
14000 17000 21000 24000
180
30
6000
8000
13500 16000 20000 23000
200
40
4000
6000
11000 13000 17000 21000
225
50
3000
5000
10000 12500 16500 20000
250
60
2500
4000
9000
11500 15000 18000
280
70
2000
3500
8000
10500 14000 17000
315
90
2000
3500
6500
8500
12500 16000
355
120
1200
2000
4200
6000
10000 13000
400
120
1200
2000
4200
6000
10000 13000