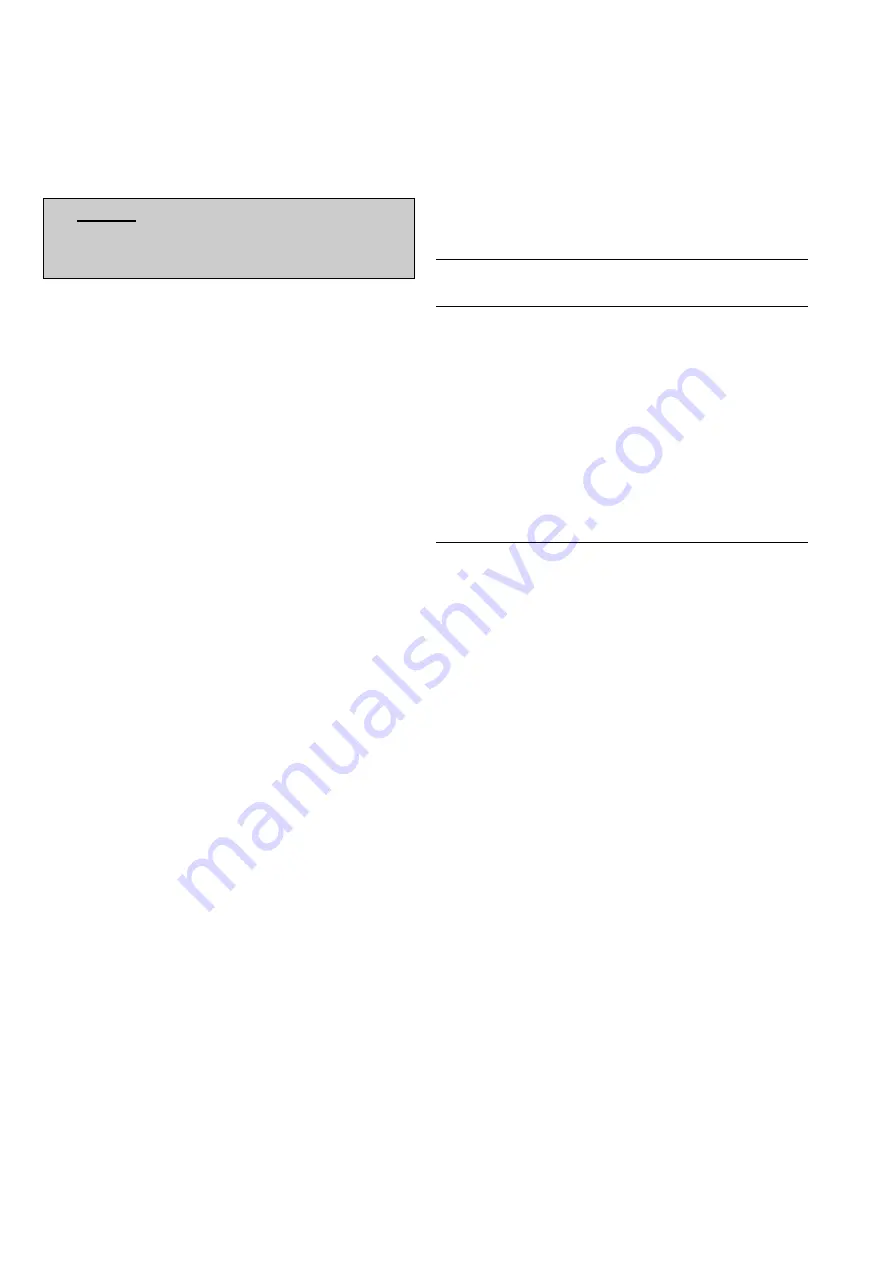
Safety considerations
The motor is intended for installation and use by quali-
fied personnel, familiar with health and safety require-
ments and national legislation.
Safety equipment necessary for the prevention of
accidents at the installation and operating site must be
provided in accordance with local regulations.
Warning
Small motors with supply current directly switched
by thermally sensitive switches can start automati-
cally.
Points to observe
1.
Do not use the motor to step on.
2.
The temperature of the outer casing of the motor
may be hot to the touch during normal operation.
3.
Some special motor applications require special
instructions (e.g. using frequency converter sup-
plies).
4.
Lifting lugs must only be used for lifting the motor
itself. They must not be used to lift the motor when
it is attached to other equipment.
Handling
Storage
The motor should always be stored indoors, in dry,
vibration free and dust free conditions.
Unprotected machined surfaces (shaft-ends and
flanges) should be protected with anti-corrosive paint.
It is recommended that shafts are rotated periodically by
hand to prevent grease migration.
Anti condensation heaters, if fitted, should preferably be
energised.
Transportation
Motors fitted with cylindrical-roller and/or angular
contact bearings must be fitted with locking devices
during transport.
Lifting
Only lift the motor using the liftling lugs.
The center of gravity of motors with the same frame
may vary due to different output, mounting arrange-
ments and auxiliary equipment.
Check that eyebolts or the lifting lugs integrated with the
motor frame are undamaged before lifting. Damaged
lifting eyes must not be used.
Lifting eyebolts must be tightened before lifting. If
needed the position of the eyebolt must be adjusted with
suitable washers.
Ensure that proper lifting equipment is used and that the
sizes of the hooks are suitable for the lifting lugs.
Care must be taken not to damage auxiliary equipment
and cables attached to the motor.
Machine weights
Total machine weight can vary within the same frame
size (center height) depending on different output,
mounting arrangement and added features.
The following table shows estimated maximum weights
for machines in their basic versions as a function of
frame material.
On machines weighing more than 25 kg, the actual
weight is stamped on the rating plate.
M2AA/MBT
M2BA
M2JA/M2KA
Frame
Weight
Add.
Weight
Weight
size
kg
for brake
kg
kg
63
6
71
8
5
13
80
12
8
20
24
90
17
10
30
37
100
25
16
40
48
112
36
20
50
52
132
63
30
90
99
160
110
55
170
170
180
160
65
250
250
200
220
300
300
225
295
400
400
250
370
550
550
280
800
800
315
1300
1300
355
2500
2500
400
3500
3500
Installation
All rating plate values relating to certification must be
carefully checked, to ensure that the motor protection,
atmosphere and zone are compatible.
Standards EN 1127-1 (Explosion prevention and protec-
tion) and EN 50281-1-2 (Electrical apparatus for use in
the presence of combustible dust) must be respected.
Special attention should be paid to dust ignition tem-
perature and dust layer thickness in relation to the
motors temperature marking.
When fitted in a vertical position with the shaft pointing
downwards, the motor must have a protective cover
against falling objects and fluid.
Ensure that the motor protection corresponds to the
environment and weather conditions; e.g. make sure
that water cannot enter the terminal box.
The earth terminal on the frame has to be connected to
PE (protective earth) with a cable according to Table 3
of EN 50014.
Cable connection between network and motor terminals
must fulfil the requirements stated in country standards
for installation or in the standard EN 60204-1 according
to the rated current indicated on the rating plate.
Motors are intended for fixed installation only. In other
cases ensure only certified cable glands for increased
safety and flameproof motors are used. For non-spark-
ing motors, cable glands should comply with EN 50014.
The IP-class of the cable gland should be at least same
as the motor protection.