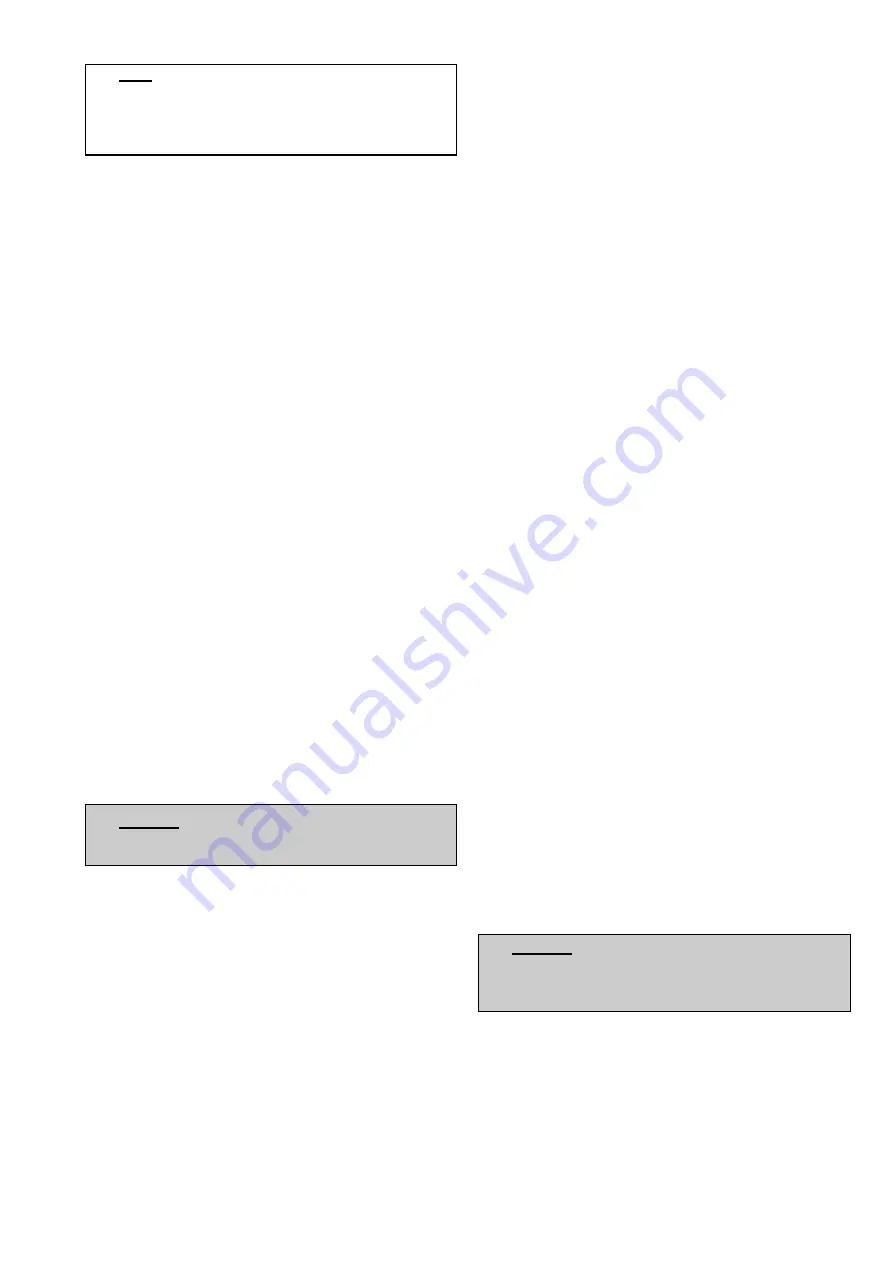
Note
Cables should be mechanically protected and
clamped close to terminal box to fulfil requirements
of EN 50014 and local installation standards (e.g.
NFC 15100).
Cooling
Check that the motor has sufficient airflow. Ensure that
no nearby equipment or surfaces radiate additional
heat to the motor. For more information about higher
ambient temperatures and cooling, see the Motor
Guide or contact ABB Motors.
Foundation
The purchaser bears full responsibility for preparation of
the foundation.
Metal foundations should be painted to avoid corrosion.
Foundations must be even, and sufficiently rigid to
withstand possible short circuit forces. They must be
dimensioned to avoid the occurrence of vibration due to
resonance.
Foundation studs
Bolt the foundation studs to the feet of the motor and
place a 1-to-2 mm shim between the stud and the feet.
Align the motor directly using appropriate means.
Grout the studs with concrete, check alignment and drill
holes for locating pins.
Alignment
Correct alignment is essential to avoid bearing failures,
vibrations and possible fractured shaft extensions.
Slide rails and belt drives
Fasten the motor to the slide rails as shown in figure 2.
Place the slide rails horizontally on the same level.
Check that the motor shaft is parallel with the driven, or
driving, shaft.
Any belt must be tensioned according to the suppliers
instructions.
Warning
Excessive belt tension will damage bearings and
can cause shaft breakage.
Do not exceed the maximum belt forces (i.e. radial
bearing loading) stated in the relevant product cata-
logues.
Motors with drain plugs for condensation
Non-sparking & Increased safety motors
Check that open drain holes face downwards when the
mounting orientation differs from standard horizontal
mounting. Motors with sealable plastic drain plugs are
delivered with these in the closed position in M2AA
motors and in the open position in M2BA motors. In very
dusty environments, all drain holes should be closed.
Flameproof motors
Drain plugs, if requested, are located at the lower part of
the end shields in order to allow condensation to escape
of the motor.
Periodically turn the knurled head of the drain plug in
order to prevent jamming. This operation must be done
when the motor is at standstill.
The regularity of checks depends on the humidity of the
ambient air, and on the local weather conditions. This
can initially be determined experimentally and must then
be strictly adhered to.
Dust Ignition Protection Motors
The drain holes must be closed on all dust ignition
protection motors.
Motor protection against overload and stalling
For increased safety motors (EEx e) the maximum
tripping time of protective devices must not be longer
than the time t
E
stamped on the motor rating plate.
A line sensitive device should be used to protect the Ex-
motor and DIP motors against overload and motor
stalling. Such devices should have good reliability and a
tripping time accurate to ±20%.
Bearings
Special care should be taken with the bearings.
These must be removed using pullers and fitted by
heating or using of special tools for the purpose. How to
replace bearings is described in detail in a separate
instruction leaflet available from ABB Motors.
Special recommendations apply when changing the
bearings on D.I.P. motors (as the seals should be
changed at the same time)
Fitting coupling halves and pulleys
Coupling halves and pulleys must be fitted using suit-
able equipment and tools that do not damage the
bearings and seals.
Never fit a coupling half or pulley by hammering it into
place or remove it using a lever pressed against the
body of the motor.
Mounting accuracy of coupling half:check that the
clearance
b
is less than 0.05 mm and that the difference
a1
to
a2
is also less than 0.05 mm. See figure 3.
Connection
In addition to the main winding and earthing terminals,
the terminal box can also contain connections for
thermistors, stationary heating elements, or PT 100
resistance elements.
Warning
Voltage may be connected at standstill inside the
terminal box for heating elements or direct winding
heating.
Connection diagrams for auxiliary elements and
connection parts can be found inside the terminal box
cover.
Approved connectors must be used to connect the
auxiliary elements. Thermistor relays, like other
switches and relays, must be placed outside the explo-
sion hazard zone.