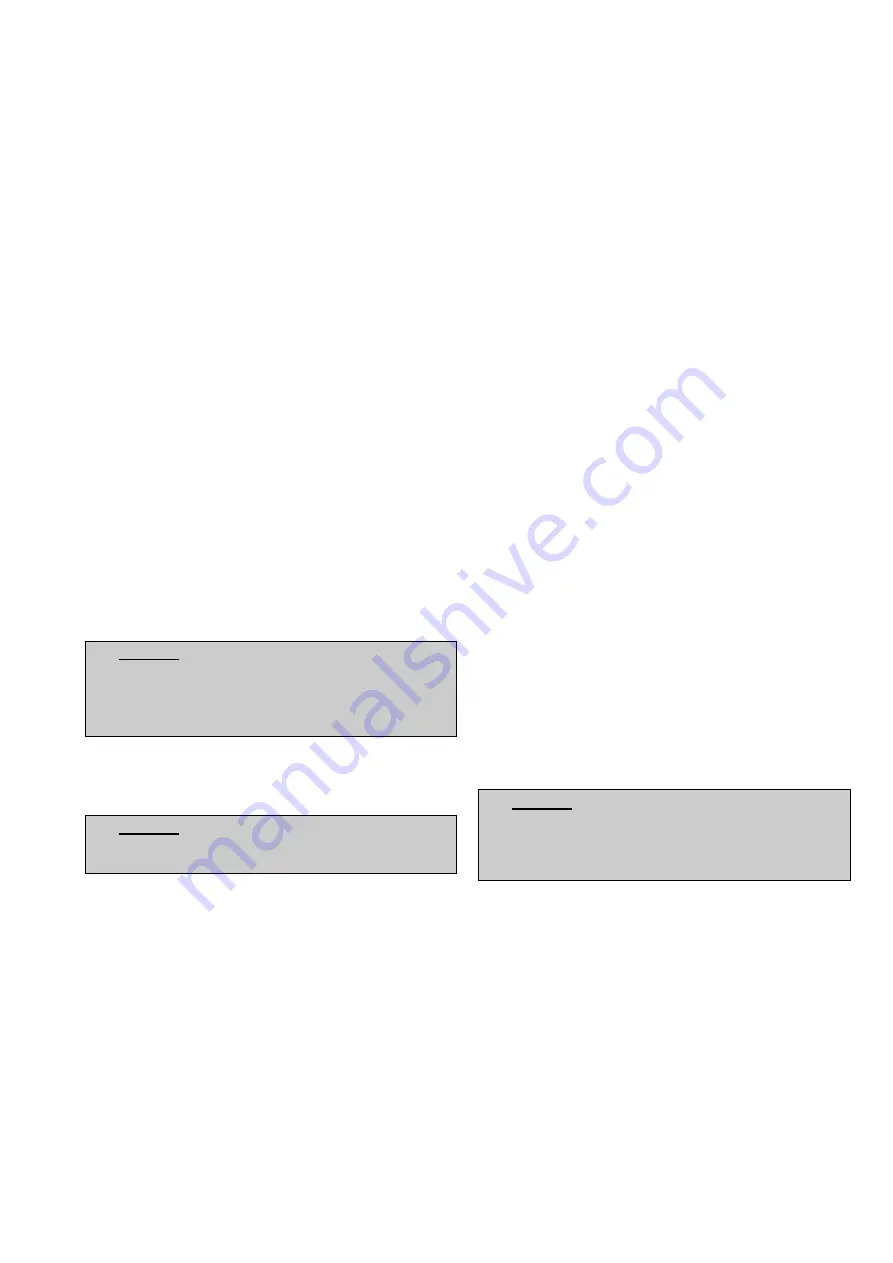
Putting into service (starting)
Reception check
Immediately upon receipt check the motor for external
damage and if found, inform the forwarding agent
without delay.
Check all rating plate data, especially voltage, winding
connection (star or delta), category,type of protection
and temperature marking.
Turn shaft by hand to check free rotation, remove
transport locking if employed.
Motors equipped with roller bearings:
Running the motor with no radial force applied to the
shaft may damage the roller bearing.
Motors equipped with angular contact bearing:
Running the motor with no axial force applied in the
right direction to the shaft may damage the angular
contact bearing.
The type of bearing is specified on the rating plate.
Motors equipped with regreasing devices:
When starting the motor for the first time, apply at least
the specified quantity of grease until new grease is
forced out from the grease outlet.
For details see section Machines with relubrication
system on page 8.
Insulation resistance check
Measure insulation resistance before commissioning
and when winding dampness is suspected.
Warning
Disconnect and lock out before working on the
motor or the driven equipment. Ensure no explo-
sive atmosphere is present while executing insula-
tion resistance check procedures.
Resistance, measured at 25°C, shall exceed the refer-
ence value, i.e.
10 M ohm (measured with 500 V dc Megger)
Warning
The windings should be discharged immediately
after measurement to avoid risk of electric shock.
Insulation resistance reference value is halved for each
20°C rise in ambient temperature.
If the reference resistance value is not attained, the
winding is too damp and must be oven dried. Oven
temperature should be 90°C for 12-16 hours followed by
105°C for 6-8 hours.
Drain hole plugs, if fitted, must be removed during
heating. After heating, make sure the plugs are refitted.
Windings drenched in seawater normally need to be
rewound.
Direct-on-line or star/delta starting
The terminal box on standard single speed motors
normally contains six winding terminals and at least one
earth terminal.
For two-speed and special motors, the supply connec-
tion must follow the instructions inside the terminal box.
Earthing must be carried out according to local regula-
tions before the machine is connected to the supply
voltage.
The voltage and connection are stamped on the rating
plate.
Direct-on-line starting (DOL):
Y or
∆
winding connections may be used.
E.g. 690 VY, 400 V
∆
indicates Y-connection for 690V
and
∆
-connection for 400V.
Star/Delta starting (Y/
D
):
The supply voltage must be equal to the rated voltage
of the motor in
∆
-connection.
Remove all connection links from the terminal block.
For increased safety motors, only direct-on-line starting
is normally allowed. If star-delta starting is required,
please consult ABB Motors.
Other starting methods:
If considering any other method for starting, e.g. soft
starter, consult ABB Motors first.
Terminals and direction of rotation
Direction of rotation is clockwise when viewing the
shaft face at the motor drive end, and the line phase
sequence L1, L2, L3 is connected to the terminals as
shown in figure 1.
To alter the direction of rotation, interchange the
connection of any two line cables.
If the motor has a uni-directional fan, ensure that the
direction of rotation is according to the arrow marked
on the motor.
Use
Operation
Warning
Disconnect and lock out before working on the
motor or the driven equipment. Ensure no explo-
sive atmosphere is present while the work is in
progress.
The motors are designed for the following environ-
mental conditions:
Normal ambient temperature limits are -20°C to +40°C.
Maximum altitude 1000m above sea level.
If these limits are exceeded, all electrical data must be
checked to equalise the surface temperature with the
temperature class according to Ignition temperature of
gases or dust. Please contact ABB Motors.
Particular attention must be paid to corrosive atmos-
pheres when using flameproof motors; ensure that the
paint protection is suitable for the ambient conditions
as corrosion can damage the explosion-proof enclo-
sure.