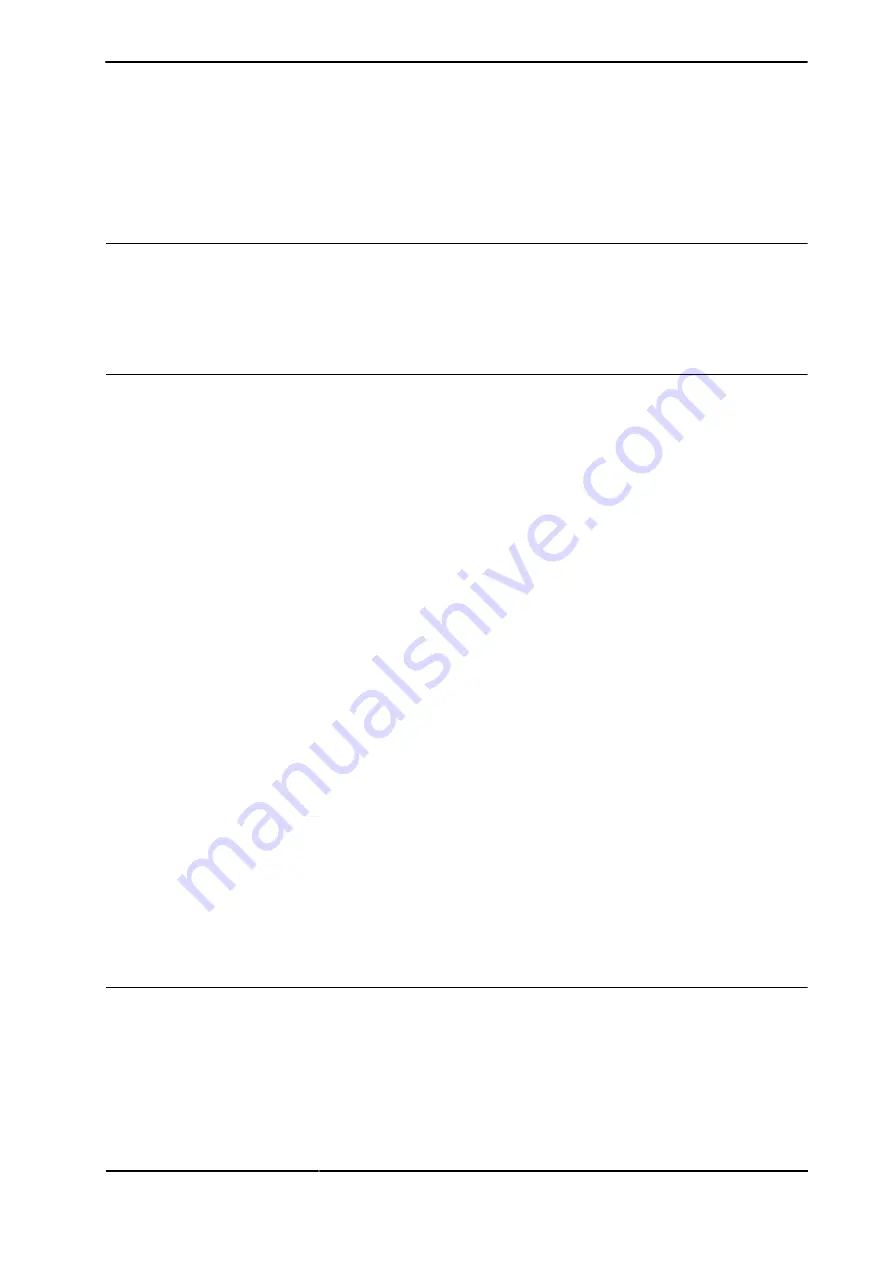
5 Calibration information
5.1. Introduction
163
3HAC023297-001 Revision: A
5 Calibration information
5.1. Introduction
General
This chapter includes general information about different calibration methods and details also
procedures that does not require specific calibration equipment.
When the robot system must be recalibrated, it is done according to documentation enclosed
with the calibration tools.
When to calibrate
The system must be calibrated if any of the below occurs.
The resolver values are changed
If resolver values are changed, the robot must be recalibrated using the calibration methods
supplied from ABB. Calibrate the robot carefully with standard calibration. The different
methods are briefly described in section
on page 164, and further
detailed in separate Calibration manuals.
If the robot has Absolute Accuracy calibration, it is also recommended but not always needed
to be calibrated for new Absolute Accuracy.
The resolver values will change when parts affecting the calibration position are replaced on
the robot, e.g. motors, wrist or part of transmission.
Contents of the revolution counter memory are lost
If the contents of the revolution counter memory are lost, the counters must be updated as
detailed in section
on page 168. This will occur when:
•
the battery is discharged
•
a resolver error occurs
•
the signal between a resolver and measurement board is interrupted
•
a robot axis is moved with the control system disconnected
The revolution counters must also be updated after the robot and controller are connected at
the first installation.
The robot is rebuilt
If the robot has been rebuilt, e.g. after a crash or when the robot has been changed for other
reachability, it needs to be recalibrated for new resolver values.
If the robot has Absolute Accuracy calibration, it needs to be calibrated for new Absolute
Accuracy.
References
The article numbers for the Calibration manuals are listed in section
Document references
in
the Product manual (part 2 of 2), reference information. Article numbers for the calibration
tools are also listed in part 2 of the Product manual.
Summary of Contents for M2000
Page 1: ... Product manual part 1 of 2 procedures Articulated robot IRB 140 M2000 M2000A M2004 ...
Page 2: ......
Page 8: ...Table of Contents 3HAC023297 001 Revision A 6 ...
Page 42: ...1 Safety 1 3 4 WARNING Safety risks during work with gearbox oil 3HAC023297 001 Revision A 40 ...
Page 78: ...3 Maintenance 3 5 1 Oil change gearbox axes 5 and 6 3HAC023297 001 Revision A 76 ...
Page 176: ...5 Calibration information 5 6 Checking the calibration position 3HAC023297 001 Revision A 174 ...
Page 178: ......
Page 179: ......
Page 182: ......
Page 186: ...Table of Contents 3HAC023297 001 Revision A 4 ...
Page 192: ...Product documentation M2004 3HAC023297 001 Revision A 10 ...
Page 208: ...1 Reference information 1 11 Mounting instructions for seals 3HAC023297 001 Revision A 26 ...
Page 214: ...2 Spare part part list 2 2 Spare part part list 3HAC023297 001 Revision A 32 ...
Page 221: ......
Page 223: ...Circuit Diagram CONTENTS Page IRB 140 Manipulator diagram 3HAC 6816 3 Rev 0 101 108 ...
Page 224: ...Manipulator Circuit Diagram 3HAC 6816 3 IRB 140 No of Sheets 8 Sheet no 101 LIST OF CONTENTS ...
Page 227: ...Manipulator Circuit Diagram 3HAC 6816 3 IRB 140 No of Sheets 8 Sheet no 104 MOTOR AXIS 1 3 ...
Page 228: ...Manipulator Circuit Diagram 3HAC 6816 3 IRB 140 No of Sheets 8 Sheet no 105 FEEDBACK AXIS 1 3 ...
Page 229: ...Manipulator Circuit Diagram 3HAC 6816 3 IRB 140 No of Sheets 8 Sheet no 106 MOTOR AXIS 4 6 ...
Page 232: ......
Page 233: ......