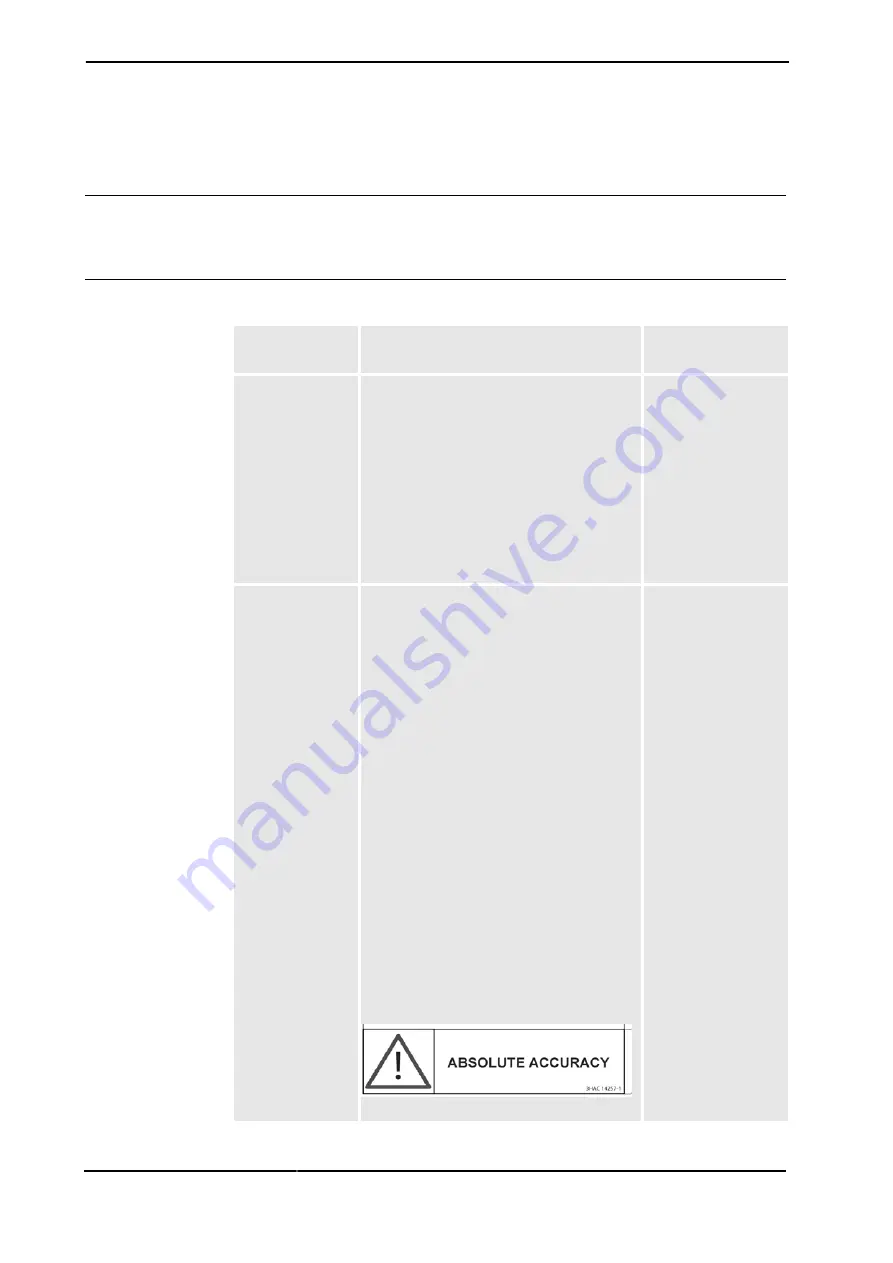
5 Calibration information
5.2. Calibration methods
3HAC023297-001 Revision: A
164
5.2. Calibration methods
Overview
This section specifies the different types of calibration and the calibration methods that are
supplied from ABB.
Types of calibration
Type of
calibration
Description
Calibration method
Standard
calibration
The calibrated robot is positioned at home
position, i.e. the axes positions (angles) are
set to 0º.
Standard calibration data is found in the file
calib.cfg, supplied with the robot at delivery.
The file identifies the correct resolver/motor
position corresponding to the robot home
position.
From deliveries together with RobotWare 5.0.5
and higher, the data will instead be found on
the SMB (serial measurement board) in the
robot, and not in a separate file.
Calibration Pendulum
(standard method)
or
Levelmeter calibration
(alternative method)
Absolute Accuracy
calibration
(optional)
Based on standard calibration, but besides
positioning the robot at home position, the
Absolute Accuracy calibration also
compensates for:
•
mechanical tolerances in the robot
structure
•
deflection due to load.
Absolute Accuracy calibration focuses on
positioning accuracy in the Cartesian
coordinate system for the robot.
Absolute Accuracy data is found in the file
absacc.cfg, supplied with the robot at delivery.
The file replaces the calib.cfg file and identifies
motor positions as well as absacc-
compensation parameters.
From deliveries together with RobotWare 5.0.6
and higher, the data will instead be found on
the SMB (serial measurement board) in the
robot, and not in a separate file.
A robot calibrated with AbsAcc has a sticker
next to the identification plate of the robot.
To regain 100% Absolute Accuracy
performance, the robot must be recalibrated
for Absolute Accuracy!
xx0400001197
CalibWare
Summary of Contents for M2000
Page 1: ... Product manual part 1 of 2 procedures Articulated robot IRB 140 M2000 M2000A M2004 ...
Page 2: ......
Page 8: ...Table of Contents 3HAC023297 001 Revision A 6 ...
Page 42: ...1 Safety 1 3 4 WARNING Safety risks during work with gearbox oil 3HAC023297 001 Revision A 40 ...
Page 78: ...3 Maintenance 3 5 1 Oil change gearbox axes 5 and 6 3HAC023297 001 Revision A 76 ...
Page 176: ...5 Calibration information 5 6 Checking the calibration position 3HAC023297 001 Revision A 174 ...
Page 178: ......
Page 179: ......
Page 182: ......
Page 186: ...Table of Contents 3HAC023297 001 Revision A 4 ...
Page 192: ...Product documentation M2004 3HAC023297 001 Revision A 10 ...
Page 208: ...1 Reference information 1 11 Mounting instructions for seals 3HAC023297 001 Revision A 26 ...
Page 214: ...2 Spare part part list 2 2 Spare part part list 3HAC023297 001 Revision A 32 ...
Page 221: ......
Page 223: ...Circuit Diagram CONTENTS Page IRB 140 Manipulator diagram 3HAC 6816 3 Rev 0 101 108 ...
Page 224: ...Manipulator Circuit Diagram 3HAC 6816 3 IRB 140 No of Sheets 8 Sheet no 101 LIST OF CONTENTS ...
Page 227: ...Manipulator Circuit Diagram 3HAC 6816 3 IRB 140 No of Sheets 8 Sheet no 104 MOTOR AXIS 1 3 ...
Page 228: ...Manipulator Circuit Diagram 3HAC 6816 3 IRB 140 No of Sheets 8 Sheet no 105 FEEDBACK AXIS 1 3 ...
Page 229: ...Manipulator Circuit Diagram 3HAC 6816 3 IRB 140 No of Sheets 8 Sheet no 106 MOTOR AXIS 4 6 ...
Page 232: ......
Page 233: ......