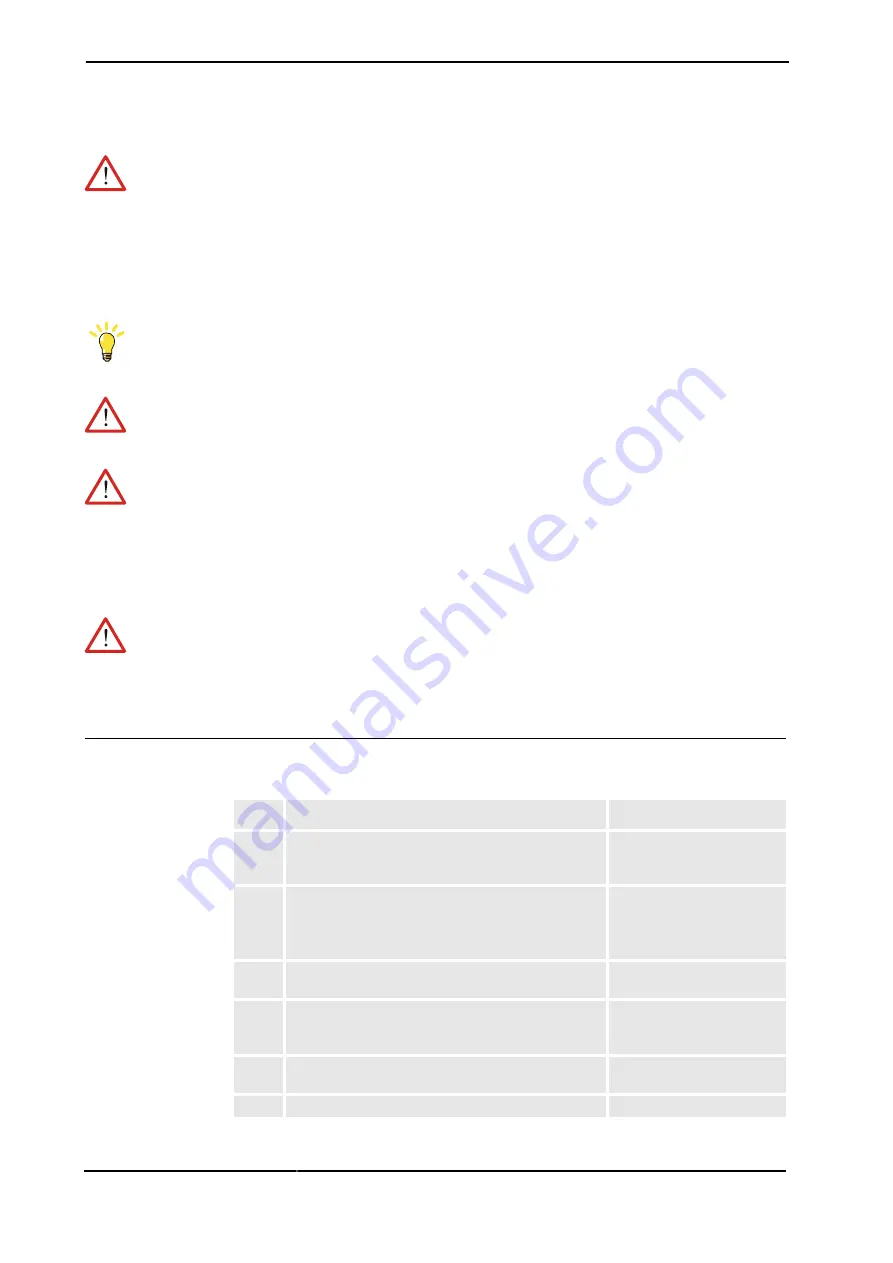
3 Maintenance
3.5.1. Oil change, gearbox, axes 5 and 6
3HAC023297-001 Revision: A
74
WARNING!
Please observe the following before commencing any repair work on the manipulator:
•
Motors and gears are HOT after running the robot! Touching the motors and gears may
result in burns!
•
Turn off all electric power, hydraulic and pneumatic pressure supplies to the robot!
•
Take any necessary measures to ensure that the manipulator does not collapse as parts
are removed, e.g. secure the lower arm with fixtures if removing motor, axis 2.
TIP!
When changing gearbox oil, first run the robot for a time to heat up the oil. Warm oil drains
quicker than cold oil.
WARNING!
When filling gearbox oil, do not mix different types of oil unless specified in the instruction.
Always use the type of oil specified by the manufacturer!
WARNING!
When filling gearbox oil, do not overfill, since this could lead to internal over-pressure inside
the gearbox which in turn may:
•
damage seals and gaskets
•
completely press out seals and gaskets
•
prevent the manipulator from moving freely
WARNING!
Changing and draining gearbox oil may require handling hot oil of up to 90 °C! Make sure
that protective gear like goggles and gloves are always worn during this activity.
Also, be aware of possible pressure build up in gearbox! When opening the oil plug, there
may be pressure present in the gearbox, causing oil to spray from the opening!
Draining, axes 5 and 6
The procedure below details how to drain the oil from gearboxes, axes 5 and 6.
Step
Action
Note
1.
Move the robot to a position where the upper arm is
close to horizontal and axis 4 in the calibration
position.
2.
Remove the oil plugs.
The cavity behind the plugs, containing the oil, is
common to gearboxes 5 and 6, but during draining,
both must be removed.
Shown in the figure
3.
Move axis 4 90° to a position where the axis 6 oil plug
faces downwards.
4.
Drain the oil from the gearbox.
Vessel capacity specified in
section
5.
Move axis 4 another 90°.
This allows the remaining oil
to be drained.
6.
Refit the oil plug.
Summary of Contents for M2000
Page 1: ... Product manual part 1 of 2 procedures Articulated robot IRB 140 M2000 M2000A M2004 ...
Page 2: ......
Page 8: ...Table of Contents 3HAC023297 001 Revision A 6 ...
Page 42: ...1 Safety 1 3 4 WARNING Safety risks during work with gearbox oil 3HAC023297 001 Revision A 40 ...
Page 78: ...3 Maintenance 3 5 1 Oil change gearbox axes 5 and 6 3HAC023297 001 Revision A 76 ...
Page 176: ...5 Calibration information 5 6 Checking the calibration position 3HAC023297 001 Revision A 174 ...
Page 178: ......
Page 179: ......
Page 182: ......
Page 186: ...Table of Contents 3HAC023297 001 Revision A 4 ...
Page 192: ...Product documentation M2004 3HAC023297 001 Revision A 10 ...
Page 208: ...1 Reference information 1 11 Mounting instructions for seals 3HAC023297 001 Revision A 26 ...
Page 214: ...2 Spare part part list 2 2 Spare part part list 3HAC023297 001 Revision A 32 ...
Page 221: ......
Page 223: ...Circuit Diagram CONTENTS Page IRB 140 Manipulator diagram 3HAC 6816 3 Rev 0 101 108 ...
Page 224: ...Manipulator Circuit Diagram 3HAC 6816 3 IRB 140 No of Sheets 8 Sheet no 101 LIST OF CONTENTS ...
Page 227: ...Manipulator Circuit Diagram 3HAC 6816 3 IRB 140 No of Sheets 8 Sheet no 104 MOTOR AXIS 1 3 ...
Page 228: ...Manipulator Circuit Diagram 3HAC 6816 3 IRB 140 No of Sheets 8 Sheet no 105 FEEDBACK AXIS 1 3 ...
Page 229: ...Manipulator Circuit Diagram 3HAC 6816 3 IRB 140 No of Sheets 8 Sheet no 106 MOTOR AXIS 4 6 ...
Page 232: ......
Page 233: ......