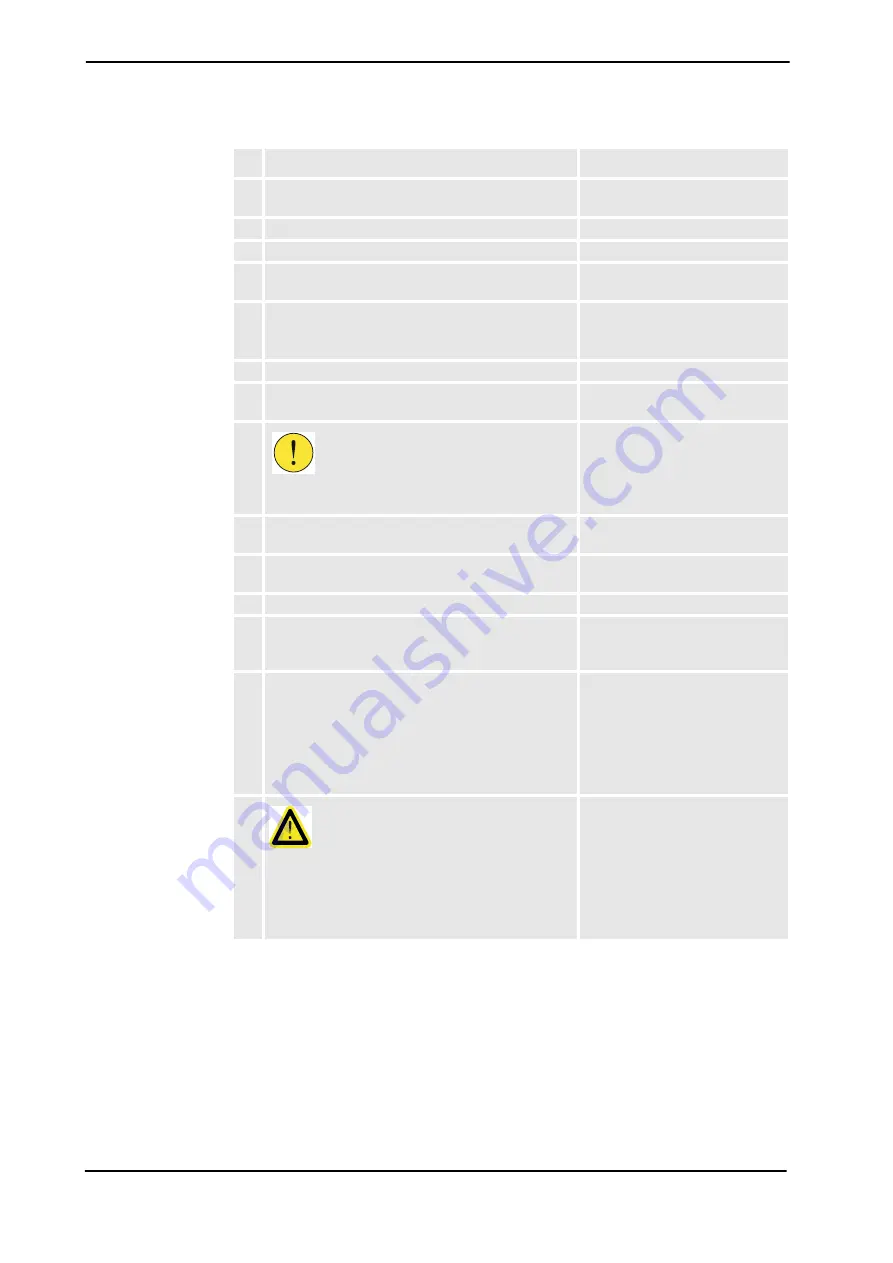
4 Repair
4.4.6. Replacement of parallel arm
3HAC028197-001 Revision: A
210
©
Co
py
rig
h
t 200
7-
200
8 ABB. All righ
ts reser
v
ed.
4. Refit a bearing on each shaft with
pressing tool,
lower arm
.
Art. no. is specified in
5. Refit the protection washer on the inner shaft.
6. Refit the lock ring on the inner shaft.
7. Lift the lower arm onto the workbench with
lifting
tool, lower arm complete
.
Art. no. is specified in
8. Adjust the lower arm in a way that both holes are
parallel.
Use a level.
9. Apply some grease in the holes in the lower arm.
10. Fit the
lifting device, parallel arm
.
Art. no. is specified in
.
11.
CAUTION!
The parallel arm weighs 92 kg.
12. Lift the parallel arm and put it in mounting position
with the lower arm.
13. Carefully press the parallel arm onto the lower arm
with the
pressing tool, lower arm
.
Art. no. is specified in
.
14. Refit the big and small VK covers.
15. Refit the complete lower arm.
Detailed in section
of complete lower arm on page
203
.
16. Recalibrate the robot.
Calibration is detailed in a
separate calibration manual,
enclosed with the calibration
tools.
General calibration information is
included in section
Calibration
information
.
17.
DANGER!
Make sure all safety requirements are met when
performing the first test run. These are further
detailed in section
cause injury or damage! on page 33
Action
Note
Continued
Summary of Contents for IRB 6660 - 130/3.1
Page 1: ...Product manual Articulated robot IRB 6660 130 3 1 IRB 6660 205 1 9 M2004 ...
Page 2: ......
Page 332: ... 0 1 23 3 4 5 5 6 2 70 2 888 2 9 6 0 9 9 2 A 8B C D 9 8 B ...
Page 333: ... 2 3 4 5 5 6 2 70 2 888 2 9 6 0 9 9 1 EF 2 888 2 9 6 9 9 8 B ...
Page 336: ... 98 2 888 7 066 0 10I 4 5 5 06 6 2 70 2 888 2 9 6 0 9 9 G E 7 F E 7 F 9 8 B ...
Page 347: ......