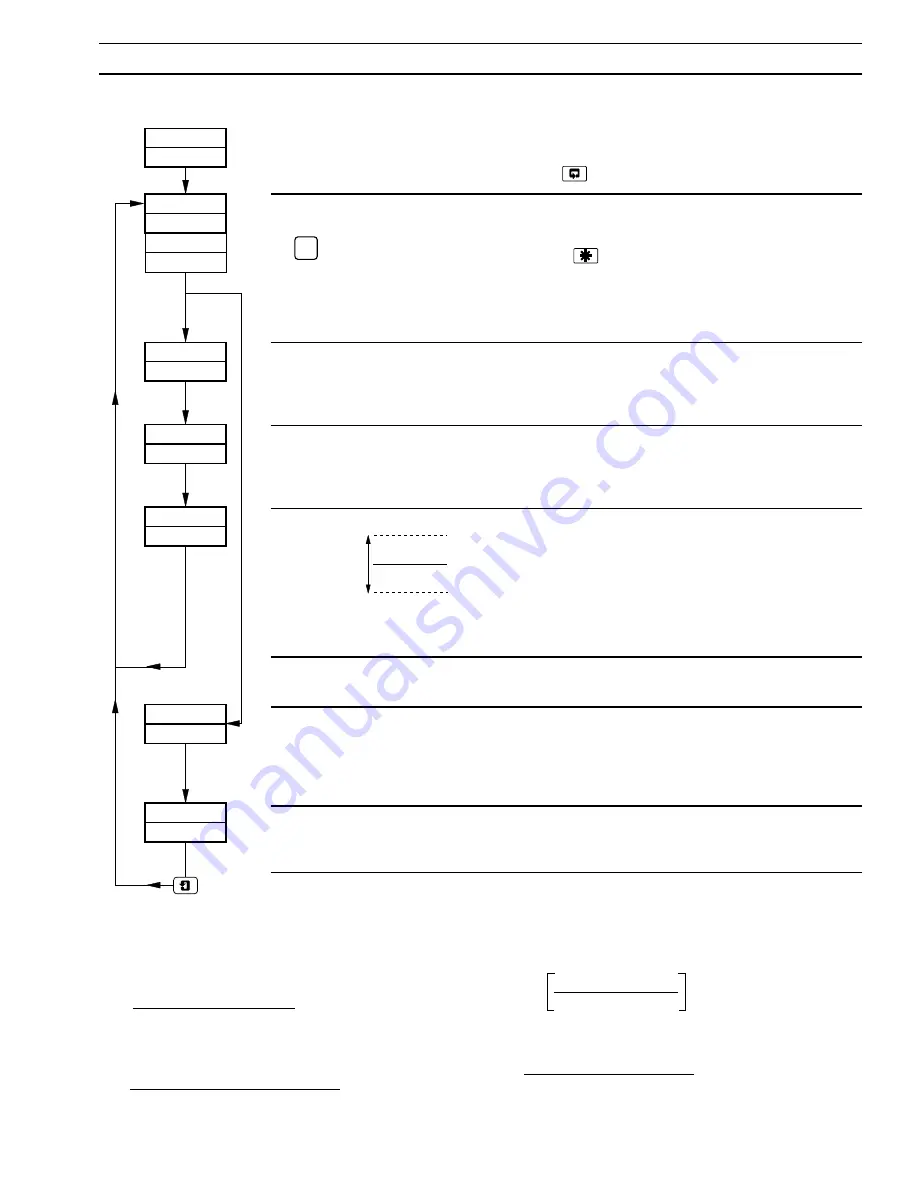
35
Page Header – Valve Page.
To advance to
Set Up Control Page
press the
switch.
Select Controller
Select the controller to be programmed (1 or 2).
✶
Note. In the remaining frames press the
switch to view the controller selected.
Ratio
The Ratio is a scaling factor, i.e. multiplies the position feedback input by the value set here.
Set the required feedback ratio, between 0.01 and 10.00 in 0.01 increments.
Bias
The Bias is an offset set as a percentage of the display full scale.
Set the required feedback bias, between –100.0 and +100.0% in 0.1% increments.
Dead Band
Deadband is set as a percentage of the position feedback span,
between 0.0 and 10.0%, to produce a deadband around the valve
control value. This gives minimum ‘hunting’ of the motorized valve.
Example – if the valve is to be driven to 50% open position and the
deadband is set to 4.0%, the motor stops driving when the position
feedback is 48%. The deadband is between 48% and 52%.
Return to
Select Controller
frame.
Regulator Travel Time
This is the time set for the regulator to travel from the fully open to the fully closed position or from
the fully closed to the fully open position.
Set the value required in seconds, between 1 and 5000 seconds.
Dead Band
Deadband is set as a percentage of the engineering range. Set a value which gives minimum
hunting of the regulator, between 0.0 and 10.0 in 0.1% increments.
Return to
Select Controller
frame.
Percentage
Deadband
(% of Range
Span
Set Point
Boundless
VALVE
PAGE
SELECt
CtrL 2
CtrL 1
NONE
rAtIO
-.--
bIAS
-.--
rGL-t
----
dEAd b
--.-
dEAd b
--.-
Position-
Proportioning
4
CONTROL CONFIGURATION LEVEL…
4.2.3
Valve Page
4.2.4
Calculation for Control Pulses, Steps and Deviation (Boundless Control only)
Minimum ‘ON’ time of integral action pulses (for a fixed control
deviation)
= (in seconds)
Minimum (approximate) time between integral action pulses
(for a fixed control deviation)
= (in seconds)
Duration of the proportional step
= 2 x x Travel Time in Seconds
% Control Deviation
= x 100%
Travel Time x Deadband %
%PB
% Control Deviation
% Proportional Band
Integral Action Time x Deadband %
2 x Control Deviation
Set Point – Process Variable
Span