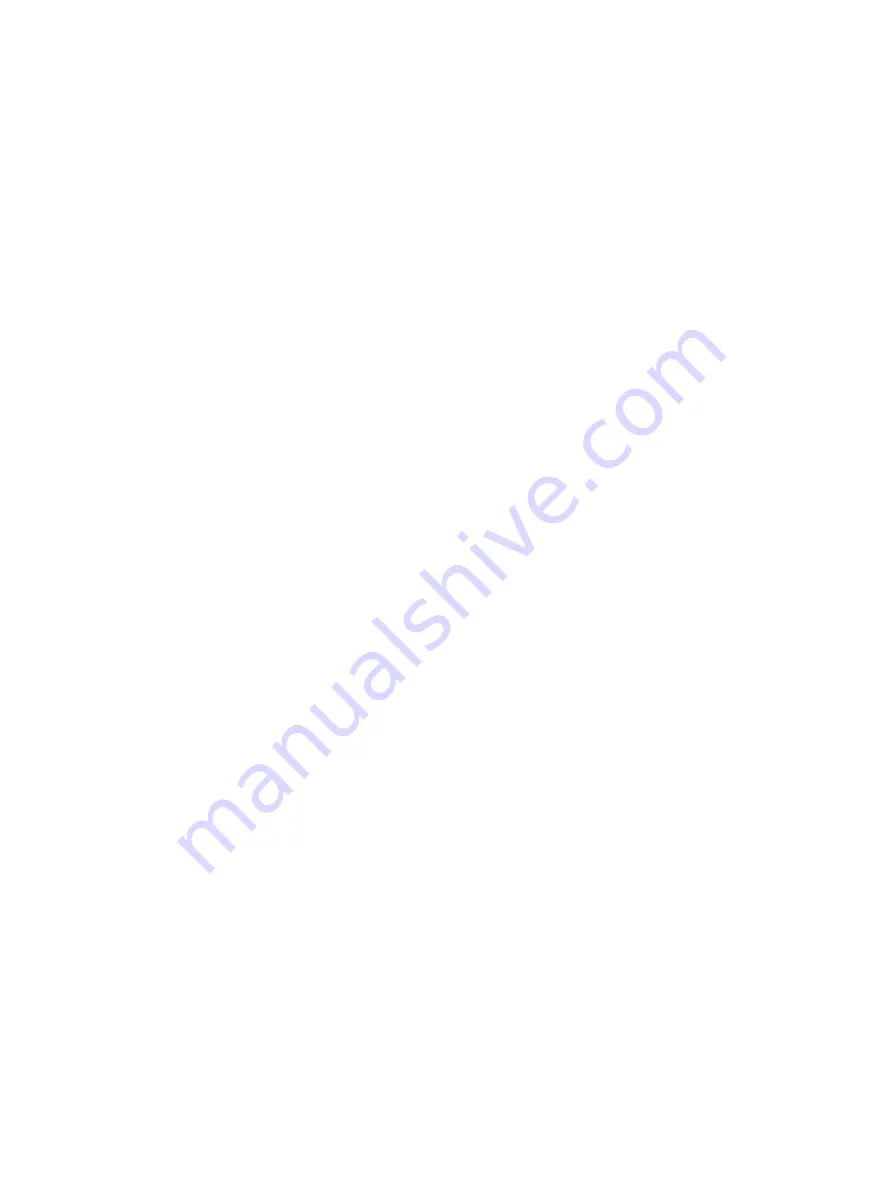
AO2000-LS25
LASER ANALYZERS | OI/AO2000-LS25-EN REV. D
75
Cleaning of optical windows
Dust, soot or other contamination on the optical windows will
reduce the signal level.
The LS25 is designed to allow a considerable reduction of
transmission (down to 10 to 30 %) without influencing the
quality of the measurements.
However, if the transmission falls below the level for reliable
measurements, the LCD shows “Low transmission.”
The optical windows must then be cleaned:
• The optical windows can be cleaned with nonabrasive
detergents or solvents.
• If there are cracks in or damage to the optical window, the
optical window should be replaced.
Since the optical windows are wedge-shaped, the new
optical window must be aligned in the same way as the old
optical window in order to maintain optical adjustment of
the system.
In order to reduce dust accumulations on the optical windows,
the device is equipped with purging connections on the
transmitter and receiver units as well as on the flanges.
A check of the optical windows should also be done in
connection with purging failures.
Alignment of the device
The alignment of the receiver and transmitter units may change
due to outer strains.
The transmission can, therefore, decrease with time.
The LCD shows the messages «Laser line-up error» and «Low
transmission» alternately.
In this case, realign the transmitter and receiver units, see
analyzer with laser alignment device
Optimizing purging gas flow of the flanges
It is generally difficult to give a recommendation of what purge
gas quantity is needed for certain applications. The required
purge gas volume depends on the flow velocity of the gas in the
sample gas path (e.g. stack, boiler or process line), as well as on
the length and diameter of the flanges, etc.
From experience, it can be assumed that the flow rate of the
purge gas in the flanges corresponds to ¹⁄₁₀ of the flow rate of
the purge gas in the pipe.
If the gas concentration to be measured is fairly constant (and
non-zero) over a few minutes one can try one of the following
procedures to measure the required purge flow:
Alternative 1:
1. Connect the service PC, and with the menu <Custom
logging> selected, start the 2-second sampling period
with “Concentration Instant”, see
Alternatively, the instantaneous concentration can be
noted down from the “Measurements” menu.
2. Quickly turn off the purge gas flow for 30 to 60 seconds
and then back on.
– The flanges will be filled with sample gas path gas a
few seconds after the purge gas is turned off.
3. Repeat step 2. a few times to be sure to have good
repeatability of the change in the measured gas
concentration, as opposed to true fluctuations in the
process.