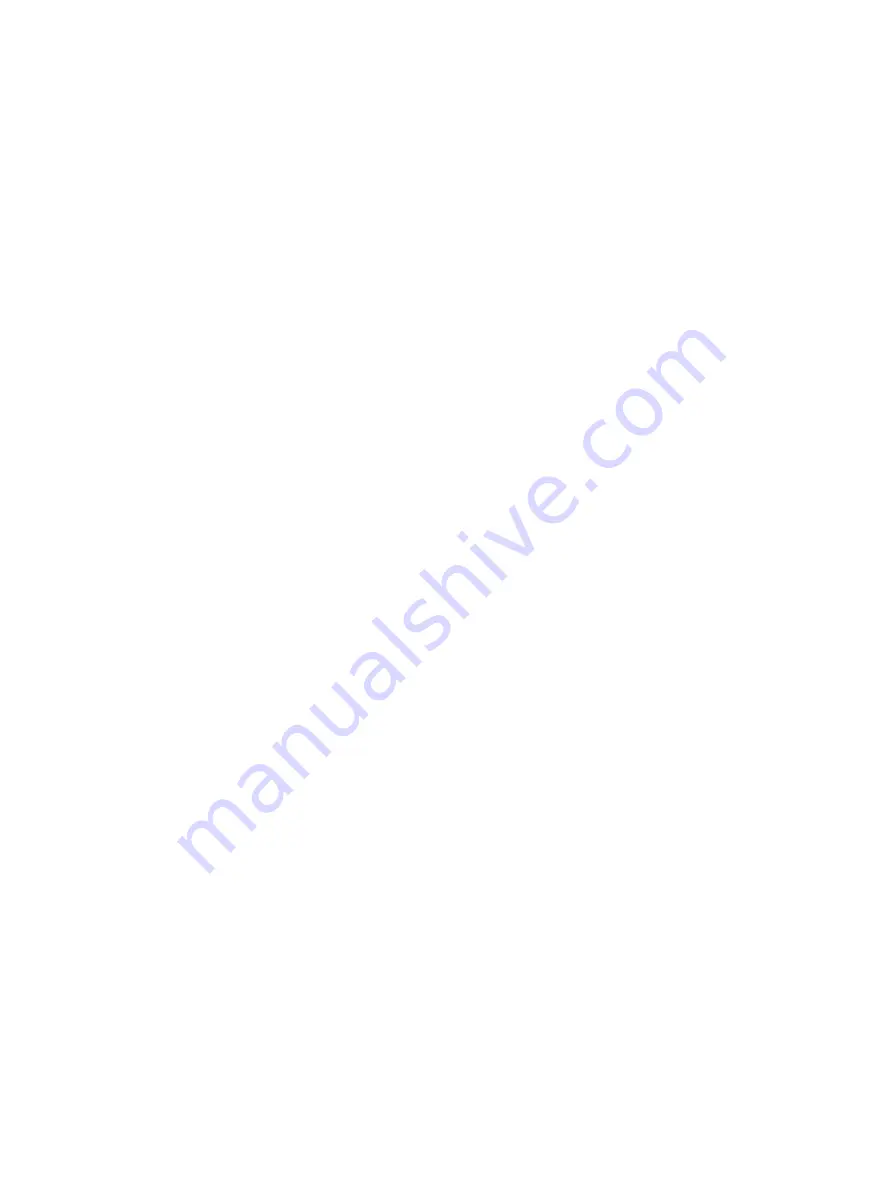
AO2000-LS25
LASER ANALYZERS | OI/AO2000-LS25-EN REV. D
37
4. Attach an O-ring (ungreased) to the adapter ring and mount
the transmitter unit to the balancing device. The guiding pin
on the adapter ring must fit the hole in the transmitter unit
window. Tighten the clamping nut on the transmitter unit.
5. Repeat steps 2 to 4 for the receiver unit.
6. Connect the transmitter and receiver units with the
corresponding cable, see
page 39.
All connectors are coded with small red pins on the inside.
7. Optionally, external pressure and temperature sensors can
be connected to the LS25 using 4 to 20 mA signals:
• General purpose devices: Connect the signal lines of the
sensors in the power supply connection plug to the
transmitter unit, see
page 41.
• Explosion-protected apparatuses: Connect the signal
lines from the sensors to the corresponding terminals in
the terminal box of the transmitter unit, see
unit – power supply / analog inputs
on page 20 or
Transmitter unit – power supply / analog inputs
page 26.
8. Connect the power supply unit to the transmitter unit with
the corresponding cable.
* Ensure that the sensors used are suitable for process conditions and have
a resolution suitable for the application.
The analyzer can now be switched on, see
page 46.
Air purging of flanges
The instrument windows are kept clean by setting up a positive
flow of air through the flanges and into the stack. This purging
will prevent particles from settling on the optical windows and
contaminating them.
The purge gas must be dried and cleaned. We recommend using
instrument air for purging. If instrument air is not available a
separate blower is needed.
A purge flow of approximately 20 to 50 l/min (process
dependent) is sufficient for most installations.
Alternatively, the initial velocity of the purge flow in the flanges
is set to
¹⁄₁₀
of the gas velocity in the duct.
After completion of the installation the purge flow is optimized
as described in
Optimizing purging gas flow of the flanges
page 75.
The air quality should conform to standard set by ISO 8573.1,
Class 2-3. This means particles down to 1 micron should be
removed, including coalesced liquid water and oil, and a
maximum allowed remaining oil aerosol content of 0.5 mg/m
3
at
21
°
C (instrument air).
Note that some instruments require nitrogen purging, e.g. O
2
instruments for high temperature or pressure applications,
some H
2
O instruments etc.