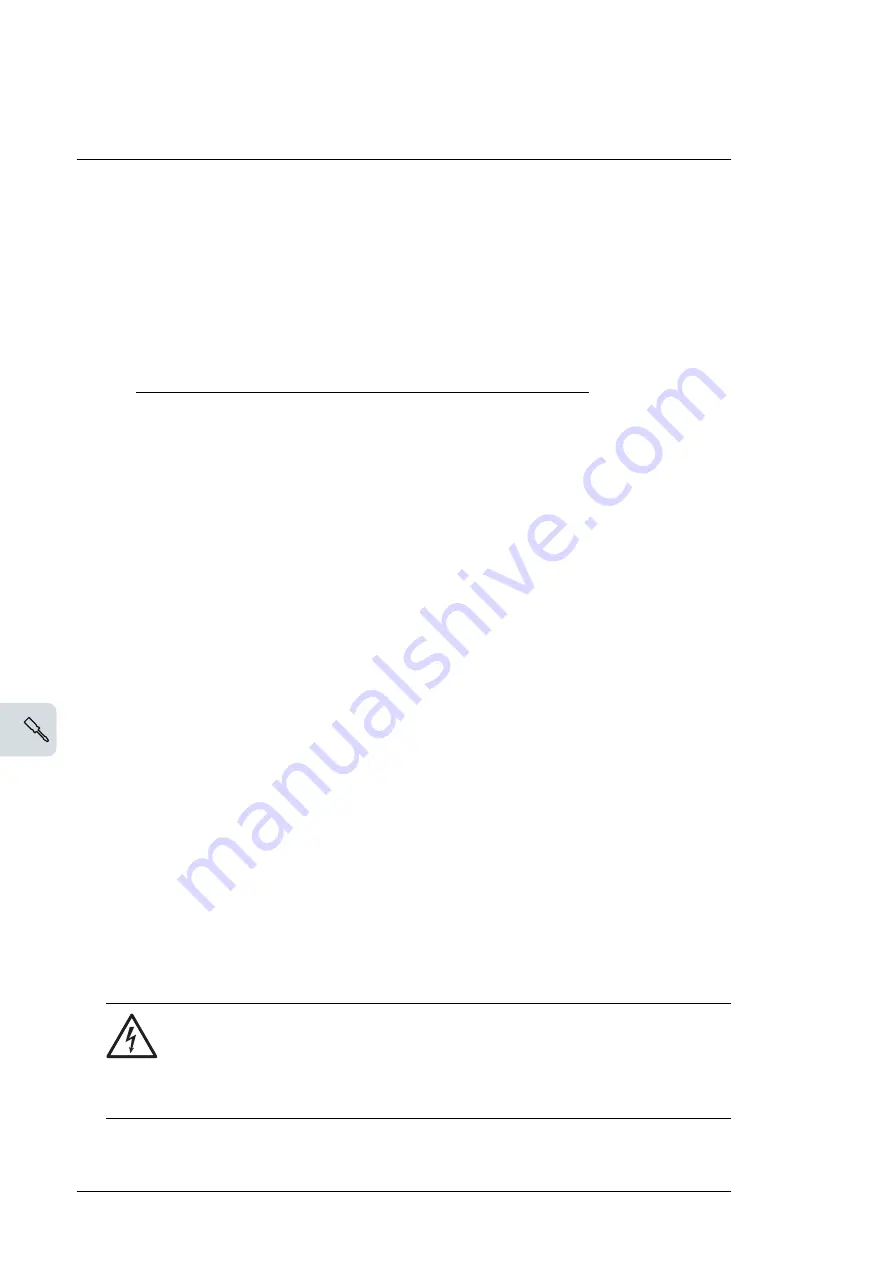
Go through these steps before you begin any installation or maintenance work.
1.
Keep the cabinet doors closed when the drive is powered. With the doors open, a risk
of a potentially fatal electric shock, arc flash or high-energy arc blast exists.
2.
Clearly identify the work location and equipment.
3.
Disconnect all possible voltage sources. Lock out and tag out.
•
Open the main disconnecting device of the drive.
•
Open the charging switch if present.
•
Open the disconnector of the supply transformer. (The main disconnecting device
in the drive cabinet does not disconnect the voltage from the AC input power busbars
of the drive cabinet.)
•
If the drive is equipped with a DC/DC converter unit (optional): Open the DC
switch/disconnector ([Q11], F286) of the DC/DC converter. Open the
disconnecting device of the energy storage connected to the DC/DC converter unit
(outside the drive cabinet).
•
Open the auxiliary voltage switch-disconnector (if present), and all other possible
disconnecting devices that isolate the drive from dangerous voltage sources.
•
In the liquid cooling unit (if present), open the motor protective circuit breaker(s) of
the cooling pumps.
•
If you have a permanent magnet motor connected to the drive, disconnect the motor
from the drive with a safety switch or by other means.
•
Make sure that re-connection is not possible. Lock out and tag out.
•
Disconnect any dangerous external voltages from the control circuits.
•
After you disconnect power from the drive, always wait 5 minutes to let the
intermediate circuit capacitors discharge before you continue.
4.
Protect any other energized parts in the work location against contact.
5.
Take special precautions when close to bare conductors.
6.
Measure that the installation is de-energized. If the measurement requires removal or
disassembly of shrouding or other cabinet structures, obey the local laws and regulations
applicable to live working (including – but not limited to – electric shock and arc
protection).
•
Use a multimeter with an impedance greater than 1 Mohm.
•
Make sure that the voltage between the drive input power terminals (L1, L2, L3)
and the grounding (PE) busbar is close to 0 V.
•
Make sure that the voltage between the drive DC busbars (+ and -) and the
grounding (PE) busbar is close to 0 V.
•
If you have a permanent magnet motor connected to the drive, make sure that the
voltage between the drive output terminals (T1/U, T2/V, T3/W) and the grounding
(PE) busbar is close to 0 V.
WARNING!
The busbars inside the cabinet are partially coated. Measurements made
through the coating are potentially unreliable, so only measure at uncoated
portions. Note that the coating does not constitute a safe or touch-proof
insulation.
7.
Install temporary grounding as required by the local regulations.
8.
Ask the person in control of the electrical installation work for a permit to work.
40 Electrical installation
Summary of Contents for ACS880-1607LC
Page 1: ... ABB INDUSTRIAL DRIVES ACS880 1607LC DC DC converter units Hardware manual ...
Page 2: ......
Page 4: ......
Page 12: ...12 ...
Page 32: ...32 ...
Page 38: ...38 ...
Page 60: ...60 ...
Page 80: ...80 ...
Page 90: ...90 ...
Page 102: ...Unit with 1 R8i converter module 102 Dimension drawings ...
Page 103: ...Dimension drawings 103 ...
Page 104: ...Location and size of energy storage connection terminals 104 Dimension drawings ...