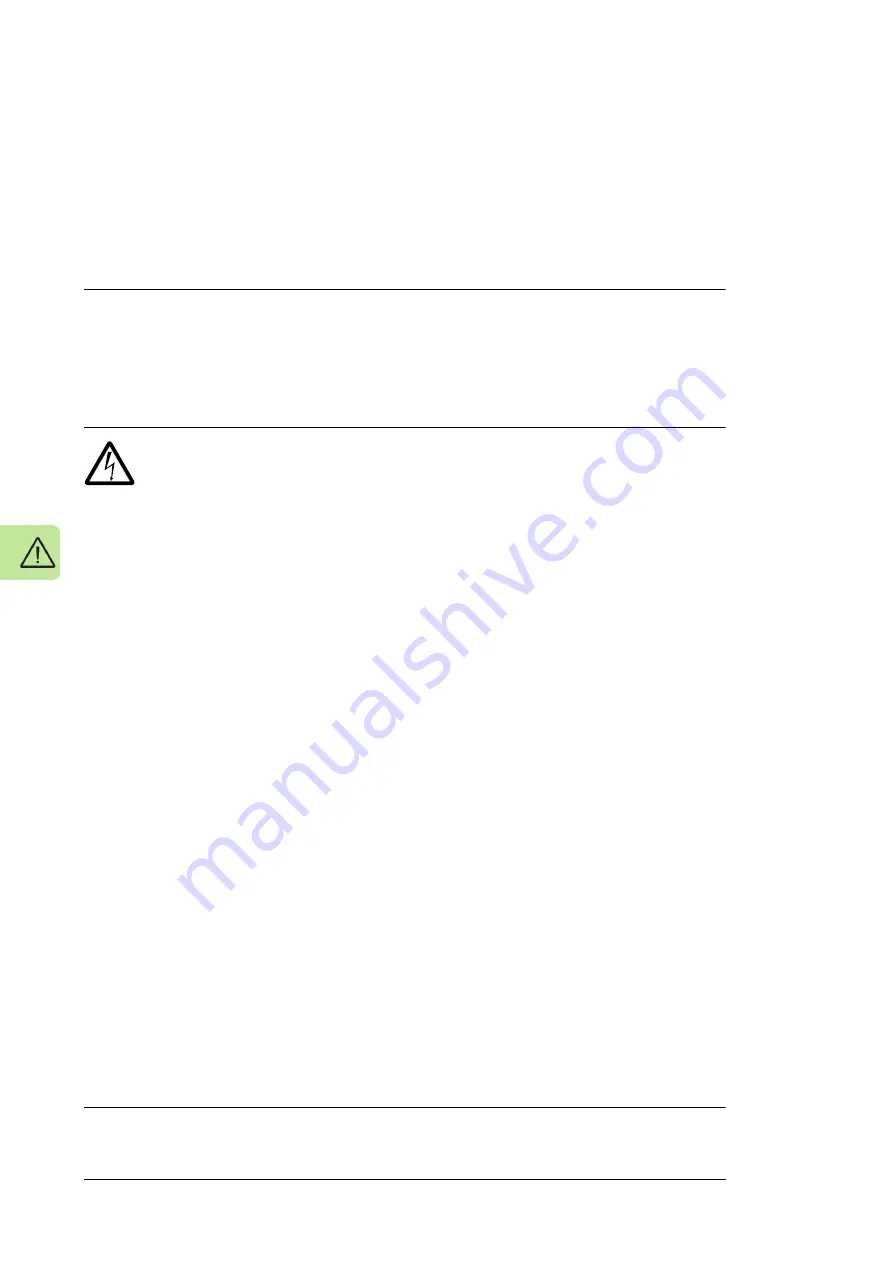
16 Safety instructions
Note:
•
If you select an external source for start command and it is on, the drive will start
immediately after fault reset unless you configure the drive for pulse start. See the
firmware manual.
•
When the control location is not set to Local, the stop key on the control panel will not
stop the drive.
•
Only authorized persons are allowed to repair a malfunctioning drive.
Electrical safety in installation, start-up and maintenance
Precautions before electrical work
These warnings are for all personnel who do work on the drive, motor cable or motor.
WARNING!
Obey these
instructions. If you ignore them, injury or death, or
damage to the equipment can occur. If you are not a qualified electrician, do not
do installation or maintenance work. Go through these steps before you begin any
installation or maintenance work.
1. Clearly identify the work location.
2. Disconnect all possible voltage sources.
•
Open the main switch-disconnector (Q1) of the drive.
•
Open the disconnector of the supply transformer as the main switch-disconnector
(Q1) of the drive does not remove the voltage from the input busbars of the drive.
•
Make sure that reconnection is not possible. Lock the disconnectors to open
position and attach a warning notice to them.
•
If the drive is connected to a permanent magnet motor, disconnect the motor from
the drive with safety switch or by other methods.
•
Disconnect any external power sources from the control circuits before you do
work on the control cables.
•
After you disconnect the drive, always wait 5 minutes to let the intermediate circuit
capacitors discharge before you continue.
3. Protect any other energized parts in the work location against contact.
4. Take special precautions when close to bare conductors.
5. Measure that the installation is de-energized.
•
Use a multimeter with an impedance of at least 1 Mohm.
•
Make sure that the voltage between the drive input power terminals (L1, L2, L3)
and the grounding (PE) busbar is close to 0 V.
•
Make sure that the voltage between the drive output power terminals
(T1/U,T2/V,T3/W) and the grounding (PE) busbar is close to 0 V.
•
Make sure that the voltage between the drive module UDC+ and UDC- terminals
and the grounding (PE) busbar is close to 0 V.
6. Install temporary grounding as required by the local regulations.
7. Ask for a permit to work from the person in control of the electrical installation work.
Summary of Contents for ACS880-07C
Page 1: ... ABB INDUSTRIAL DRIVES Hardware manual ACS880 07C drives 45 to 710 kW 50 to 700 hp ...
Page 4: ......
Page 12: ...12 ...
Page 74: ...74 Electrical installation PE PE 8 PE 13 11 7 8 12 13 ...
Page 88: ...88 Electrical installation ...
Page 98: ...98 Control unit of frames R6 to R9 ...
Page 110: ...110 Fault tracing ...
Page 125: ...Maintenance 125 7 Install the sliding rail ...
Page 132: ...132 Maintenance 9 Fasten the extraction ramp to the cabinet base with two screws 9b 9a ...
Page 136: ...136 Maintenance ...
Page 148: ...148 Technical data R6 Input and output cable terminal size incoming switch OT160 ...
Page 149: ...Technical data 149 R7 Input and output cable terminal size incoming switch OT160 OT250 ...
Page 150: ...150 Technical data R8 Input and output cable terminal size incoming switch OT160 OT250 ...
Page 151: ...Technical data 151 R7 Input and output cable terminal size incoming switch OT315 ...
Page 152: ...152 Technical data R8 Input and output cable terminal size incoming switch OT315 ...
Page 153: ...Technical data 153 R9 Input and output cable terminal size incoming switch OT315 OT400 ...
Page 154: ...154 Technical data R9 Input and output cable terminal size incoming switch OT630 ...
Page 155: ...Technical data 155 R6 R7 R8 Input cable terminal size incoming switch OT160 OT250 option F250 ...
Page 156: ...156 Technical data R7 R8 Input cable terminal size incoming switch OT315 option F250 ...
Page 157: ...Technical data 157 R9 Input cable terminal size incoming switch OT315 OT400 option F250 ...
Page 158: ...158 Technical data R9 Input cable terminal size incoming switch OT630 option F250 ...
Page 159: ...Technical data 159 R6 R7 R8 Output cable terminal size DU DT filter option E205 ...
Page 160: ...160 Technical data R9 Output cable terminal size DU DT filter option E205 ...
Page 161: ...Technical data 161 R10 Input and output cable terminal size ...
Page 162: ...162 Technical data ...
Page 163: ...Technical data 163 ...
Page 164: ...164 Technical data R11 Input and output cable terminal size ...
Page 165: ...Technical data 165 ...
Page 166: ...166 Technical data ...
Page 172: ...172 Technical data ...
Page 174: ...174 Dimension drawings Frame sizes R6 to R8 ...
Page 175: ...Dimension drawings 175 Frame size R9 ...
Page 176: ...176 Dimension drawings Frame size R10 ...
Page 177: ...Dimension drawings 177 Frame size R11 ...
Page 178: ...178 Dimension drawings ...
Page 180: ...180 Safe torque off function ...