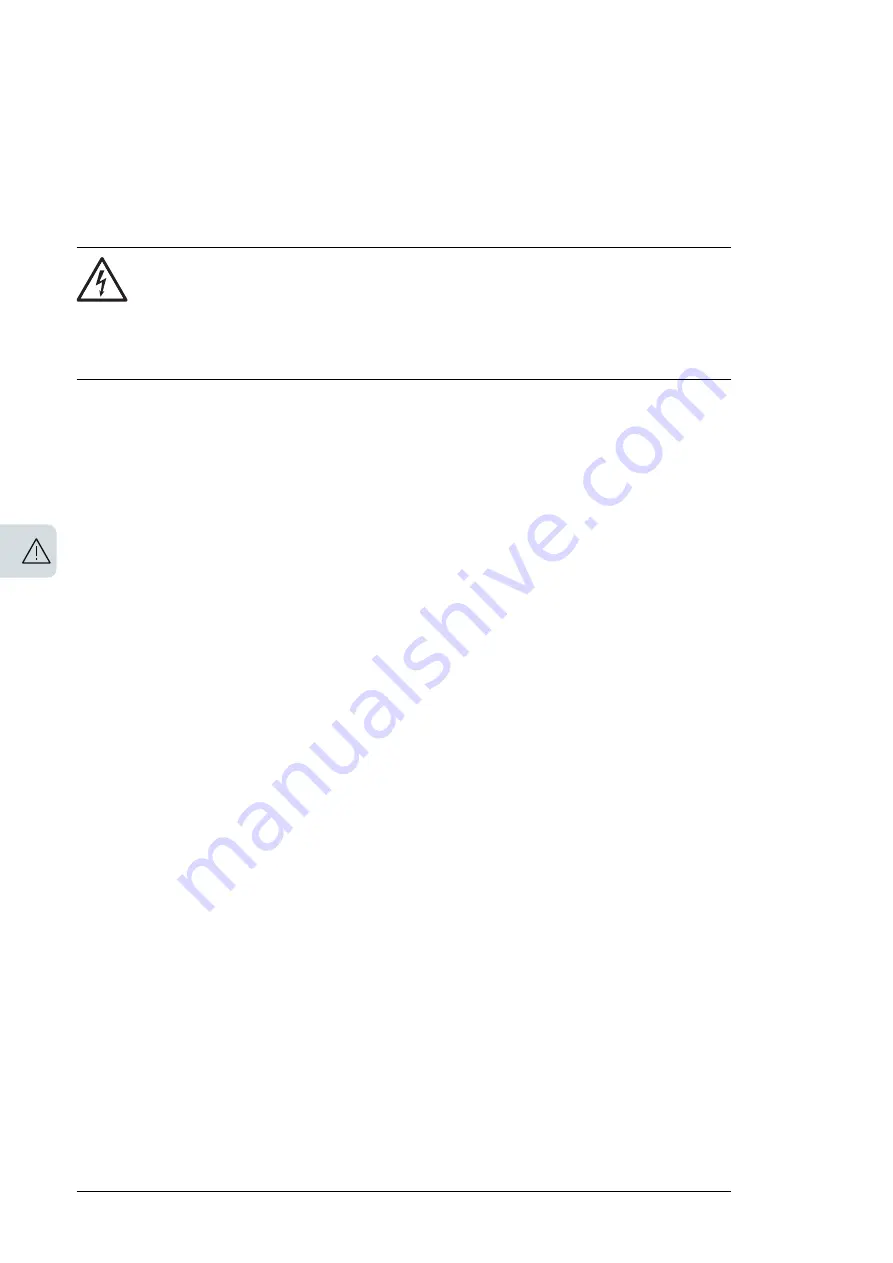
Electrical safety in installation, start-up and maintenance
■
Electrical safety precautions
These electrical safety precautions are for all personnel who do work on the drive, motor
cable or motor.
WARNING!
Obey these instructions. If you ignore them, injury or death, or damage to the
equipment can occur.
If you are not a qualified electrician, do not do installation or maintenance work.
Go through these steps before you begin any installation or maintenance work.
1.
Keep the cabinet doors closed when the drive is powered. With the doors open, a risk
of a potentially fatal electric shock, arc flash or high-energy arc blast exists.
2.
Clearly identify the work location and equipment.
3.
Disconnect all possible voltage sources. Make sure that re-connection is not possible.
Lock out and tag out.
•
Open the main disconnecting device of the drive.
•
Open the charging switch if present.
•
Open the disconnector of the supply transformer. (The main disconnecting device
in the drive cabinet does not disconnect the voltage from the AC input power busbars
of the drive cabinet.)
•
Open the auxiliary voltage switch-disconnector (if present), and all other possible
disconnecting devices that isolate the drive from dangerous voltage sources.
•
If you have a permanent magnet motor connected to the drive, disconnect the motor
from the drive with a safety switch or by other means.
•
Disconnect any dangerous external voltages from the control circuits.
•
After you disconnect power from the drive, always wait 5 minutes to let the
intermediate circuit capacitors discharge before you continue.
4.
Protect any other energized parts in the work location against contact.
5.
Take special precautions when close to bare conductors.
6.
Measure that the installation is de-energized. If the measurement requires removal or
disassembly of shrouding or other cabinet structures, obey the local laws and regulations
applicable to live working (including – but not limited to – electric shock and arc
protection).
•
Use a multimeter with an impedance greater than 1 Mohm.
•
Make sure that the voltage between the drive input power terminals (L1, L2, L3)
and the grounding (PE) busbar is close to 0 V.
•
Make sure that the voltage between the drive DC busbars (+ and -) and the
grounding (PE) busbar is close to 0 V.
•
If you have a permanent magnet motor connected to the drive, make sure that the
voltage between the drive output terminals (T1/U, T2/V, T3/W) and the grounding
(PE) busbar is close to 0 V.
20 Safety instructions
3
Summary of Contents for ACS580-07
Page 1: ... ABB GENERAL PURPOSE DRIVES ACS580 07 Hardware manual ...
Page 2: ......
Page 4: ......
Page 14: ...14 ...
Page 21: ...Measuring points of frames R6 to R9 are shown below PE L1 L2 L3 Safety instructions 21 ...
Page 26: ...26 ...
Page 30: ...30 ...
Page 50: ...50 ...
Page 62: ...62 ...
Page 95: ...Electrical installation 95 11 ...
Page 101: ...Electrical installation 101 11 ...
Page 114: ...114 ...
Page 128: ...128 ...
Page 134: ...134 ...
Page 142: ...142 Maintenance ...
Page 155: ...3 4 5 Maintenance 155 ...
Page 157: ...8 Disconnect the drive module output busbars M12 70 N m 52 lbf ft 7 8 Maintenance 157 ...
Page 161: ...4 5 3 Maintenance 161 ...
Page 163: ...8 Disconnect the drive module output busbars M12 70 N m 52 lbf ft 7 8 Maintenance 163 ...
Page 169: ...1 2 3 5a 5b CR2032 Maintenance 169 ...
Page 170: ...170 ...
Page 186: ...Frame R6 Input and motor cable terminal dimensions option F289 DET A 186 Technical data ...
Page 201: ...Frame R9 Input and motor cable terminal dimensions option F289 Technical data 201 ...
Page 202: ...Frame R10 Input and motor cable terminal dimensions bottom entry and exit 202 Technical data ...
Page 204: ...Frame R10 Input and motor cable terminal dimensions top entry and exit 204 Technical data ...
Page 206: ...Frame R11 Input and motor cable terminal dimensions bottom entry and exit 206 Technical data ...
Page 208: ...Frame R11 Input and motor cable terminal dimensions top entry and exit 208 Technical data ...
Page 217: ...Declaration of Conformity Technical data 217 ...
Page 218: ...218 Technical data ...
Page 223: ...Dimension drawings Example dimension drawings are shown below 13 Dimension drawings 223 ...
Page 224: ...Frames R6 and R7 IP21 UL Type 1 224 Dimension drawings ...
Page 225: ...Frames R6 and R7 B054 IP42 UL Type 1 Dimension drawings 225 ...
Page 226: ...Frames R6 and R7 B055 IP54 UL Type 12 226 Dimension drawings ...
Page 227: ...Frames R6 and R7 H351 and H353 top entry and exit Dimension drawings 227 ...
Page 228: ...Frames R6 and R7 F289 228 Dimension drawings ...
Page 229: ...Frames R6 and R7 F289 H351 H353 Dimension drawings 229 ...
Page 230: ...Frames R8 and R9 IP21 230 Dimension drawings ...
Page 231: ...Frames R8 and R9 B054 IP42 UL Type 1 Dimension drawings 231 ...
Page 232: ...Frames R8 and R9 B055 IP54 UL Type 12 232 Dimension drawings ...
Page 233: ...Frames R8 and R9 H351 and H353 top entry and exit Dimension drawings 233 ...
Page 234: ...Frames R8 and R9 F289 234 Dimension drawings ...
Page 235: ...Frames R8 and R9 F289 H351 H353 Dimension drawings 235 ...
Page 236: ...Frames R10 and R11 IP21 236 Dimension drawings ...
Page 237: ...Frames R10 and R11 B054 IP42 UL Type 1 Dimension drawings 237 ...
Page 238: ...Frames R10 and R11 B055 IP54 UL Type 12 238 Dimension drawings ...
Page 239: ...Frames R10 and R11 F289 T Dimension drawings 239 ...
Page 240: ...Frames R10 and R11 H351 H353 240 Dimension drawings ...
Page 241: ...Frames R10 and R11 B054 IP42 UL type 1 H351 H353 T Dimension drawings 241 ...
Page 242: ...Frames R10 and R11 B055 IP54 UL type 12 H351 H353 T 242 Dimension drawings ...
Page 257: ... Declaration of conformity The Safe torque off function 257 ...
Page 269: ...Setting Parameter 1 s 15 09 RO4 OFF delay Optional I O extension modules 269 ...