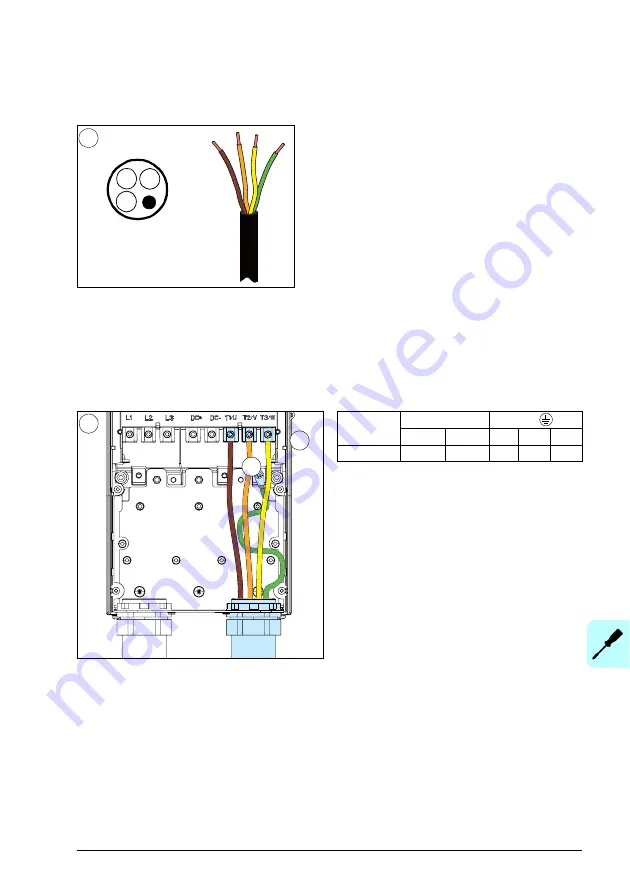
Electrical installation – North America 187
UL
NEC
Motor cabling
6. Strip the ends of the conductors.
7. Slide the conductors through the conduit.
8. Connect the conductors:
•
Connect the grounding conductor to the grounding terminal (8a).
•
Connect the phase conductors to the T1/U, T2/V and T3/W terminals (8b).
Tighten the screws to the torque given in the table.
Conduit
6
8a
8
8b
Frame size T1/U, T2/V, T3/W
PE,
N·m
lbf·ft
M
N·m lbf·ft
R5
5.6
4.1
M5
2.2
1.6
Summary of Contents for ACH580-01 Series
Page 1: ...ABB DRIVES FOR HVAC ACH580 01 drives 0 75 to 250 kW 1 to 350 hp Hardware manual...
Page 2: ...Related documents are listed on page 27...
Page 4: ......
Page 14: ...14 Table of contents...
Page 24: ...24 Safety instructions...
Page 34: ...34 Introduction to the manual...
Page 52: ...52 Operation principle and hardware description...
Page 112: ...112 Guidelines for planning the electrical installation...
Page 122: ...122 Electrical installation IEC IEC R6 R9 Screw A EMC DC B EMC AC C VAR 3 B 3 A 4 C...
Page 156: ...156 Electrical installation IEC IEC R4 0 5 0 6 N m 0 4 lbf ft 7 4 3 8 11 5 9 11 6 10 8 4...
Page 157: ...Electrical installation IEC 157 IEC R5 4 6 11 11 10 4 3 5 7 8 9 0 5 0 6 N m 0 4 lbf ft 4 8...
Page 160: ...160 Electrical installation IEC IEC R3 R5 R1 R2 3 2 3 4 6 6 7 7 4 5 5...
Page 210: ...210 Electrical installation North America UL NEC R4 4 lbf ft 7 4 3 11 5 9 11 6 10...
Page 211: ...Electrical installation North America 211 UL NEC 8 R5 4 6 11 11 10 3 5 7 9 0 4 lbf ft 4...
Page 214: ...214 Electrical installation North America UL NEC R3 R5 R1 R2 3 2 3 4 6 6 7 7 4 5 5...
Page 222: ...222 Electrical installation North America UL NEC...
Page 242: ...242 Maintenance and hardware diagnostics...
Page 245: ...Technical data 245 See definitions and notes on page 247...
Page 308: ...308 Technical data...
Page 310: ...310 Dimension drawings Frame R1 IP21 UL Type 1 3AXD10000601652...
Page 311: ...Dimension drawings 311 Frame R1 IP55 UL Type 12 3AXD10000601699...
Page 312: ...312 Dimension drawings Frame R1 IP55 F278 UL Type 12 3AXD10000649451...
Page 313: ...Dimension drawings 313 Frame R2 IP21 UL Type 1 3AXD10000602398...
Page 314: ...314 Dimension drawings Frame R2 IP55 UL Type 12 3AXD10000602401...
Page 315: ...Dimension drawings 315 Frame R2 IP55 F278 UL Type 12 3AXD10000649654...
Page 316: ...316 Dimension drawings Frame R3 IP21 UL Type 1 3AXD10000602466...
Page 317: ...Dimension drawings 317 Frame R3 IP55 UL Type 12 3AXD10000602519...
Page 318: ...318 Dimension drawings Frame R3 IP55 E223 UL Type 12 3AXD10000649130...
Page 319: ...Dimension drawings 319 Frame R3 IP55 F278 F316 UL Type 12 3AXD10000649130...
Page 320: ...320 Dimension drawings Frame R4 IP21 UL Type 1 3AXD10000332430...
Page 321: ...Dimension drawings 321 Frame R4 IP55 UL Type 12 3AXD10000427933...
Page 322: ...322 Dimension drawings Frame R4 IP55 E223 UL Type 12 3AXD10000649283...
Page 323: ...Dimension drawings 323 Frame R4 IP55 F278 F316 UL Type 12 3AXD10000649283...
Page 324: ...324 Dimension drawings Frame R5 IP21 UL Type 1 3AXD10000412280...
Page 325: ...Dimension drawings 325 Frame R5 IP55 UL Type 12 3AXD10000415964...
Page 326: ...326 Dimension drawings Frame R5 IP55 E223 UL Type 12 3AXD10000687928...
Page 327: ...Dimension drawings 327 Frame R5 IP55 F278 F316 UL Type 12 3AXD10000687928...
Page 328: ...328 Dimension drawings Frame R6 IP21 UL Type 1 3AXD10000258705...
Page 329: ...Dimension drawings 329 Frame R6 IP55 UL Type 12 3AXD10000330667...
Page 330: ...330 Dimension drawings Frame R7 IP21 UL Type 1 3AXD10000258995...
Page 331: ...Dimension drawings 331 Frame R7 IP55 UL Type 12 3AXD10000330932...
Page 332: ...332 Dimension drawings Frame R8 IP21 UL Type 1 3AXD10000287670...
Page 333: ...Dimension drawings 333 Frame R8 IP55 UL Type 12 3AXD10000332446...
Page 334: ...334 Dimension drawings Frame R9 IP21 UL Type 1 3AXD10000287428...
Page 335: ...Dimension drawings 335 Frame R9 IP55 UL Type 12 3AXD10000334310...
Page 336: ...336 Dimension drawings...
Page 362: ...362 Safe torque off function...
Page 388: ...388 Optional I O extension modules...