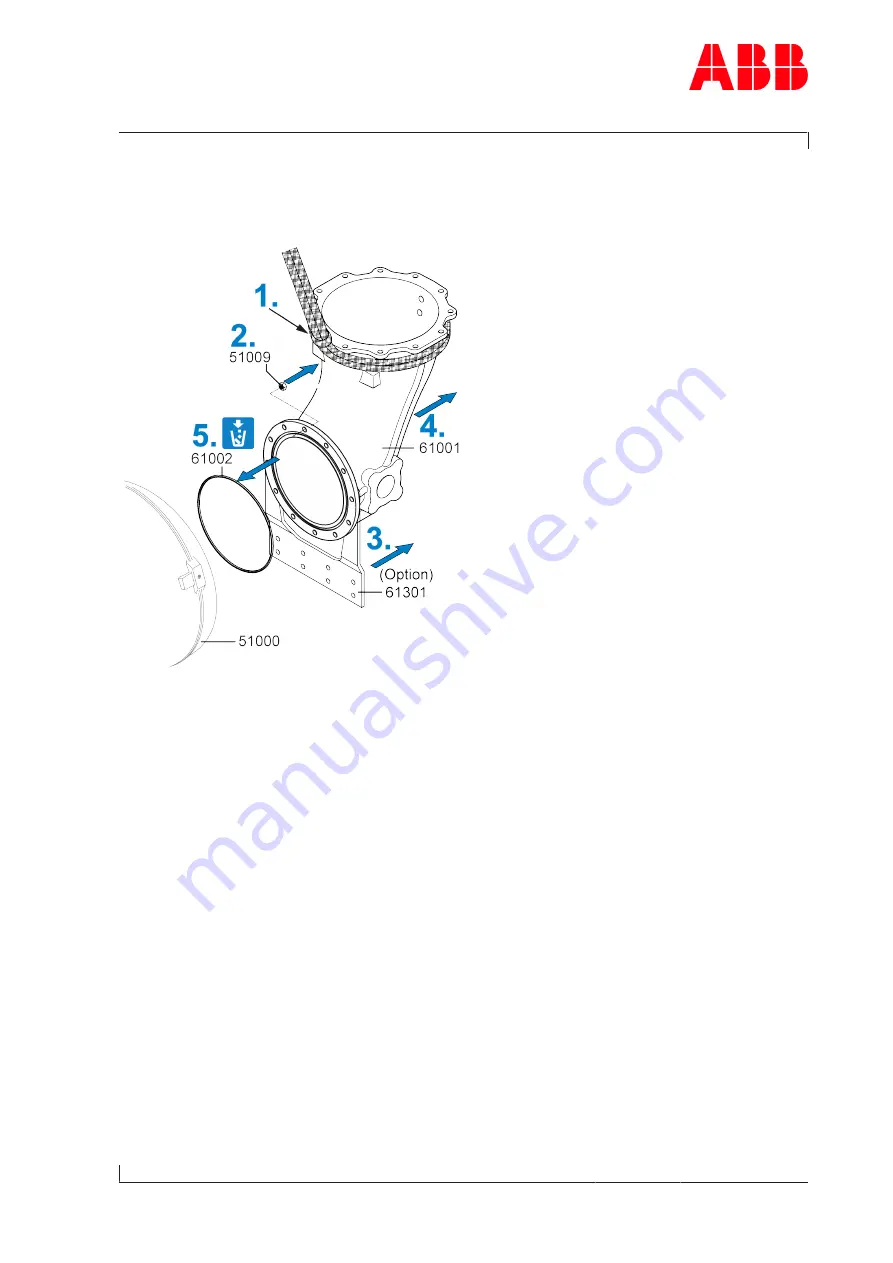
Operation Manual / 4 Product description / A130-H.. - A140-H
8 Dismantling and fitting / 8.4 Removing the gas outlet casing
© Copyright 2017 ABB. All rights reserved.
HZTL4030_EN
Revision D
May 2017
8.4
Removing the gas outlet casing
u
Mark the casing position for assembly.
Fig. 28: Removing the gas outlet casing
1. Attach lifting gear to the gas outlet casing (61001).
2. Loosen and remove nuts (51009).
3. If present: Loosen the support (61301) from the bracket.
4. Remove the gas outlet casing (61001), set it down properly in an appropriate place and
secure it.
5. Remove and dispose of the gasket (61002).
Page
61
/
91
All manuals and user guides at all-guides.com
all-guides.com