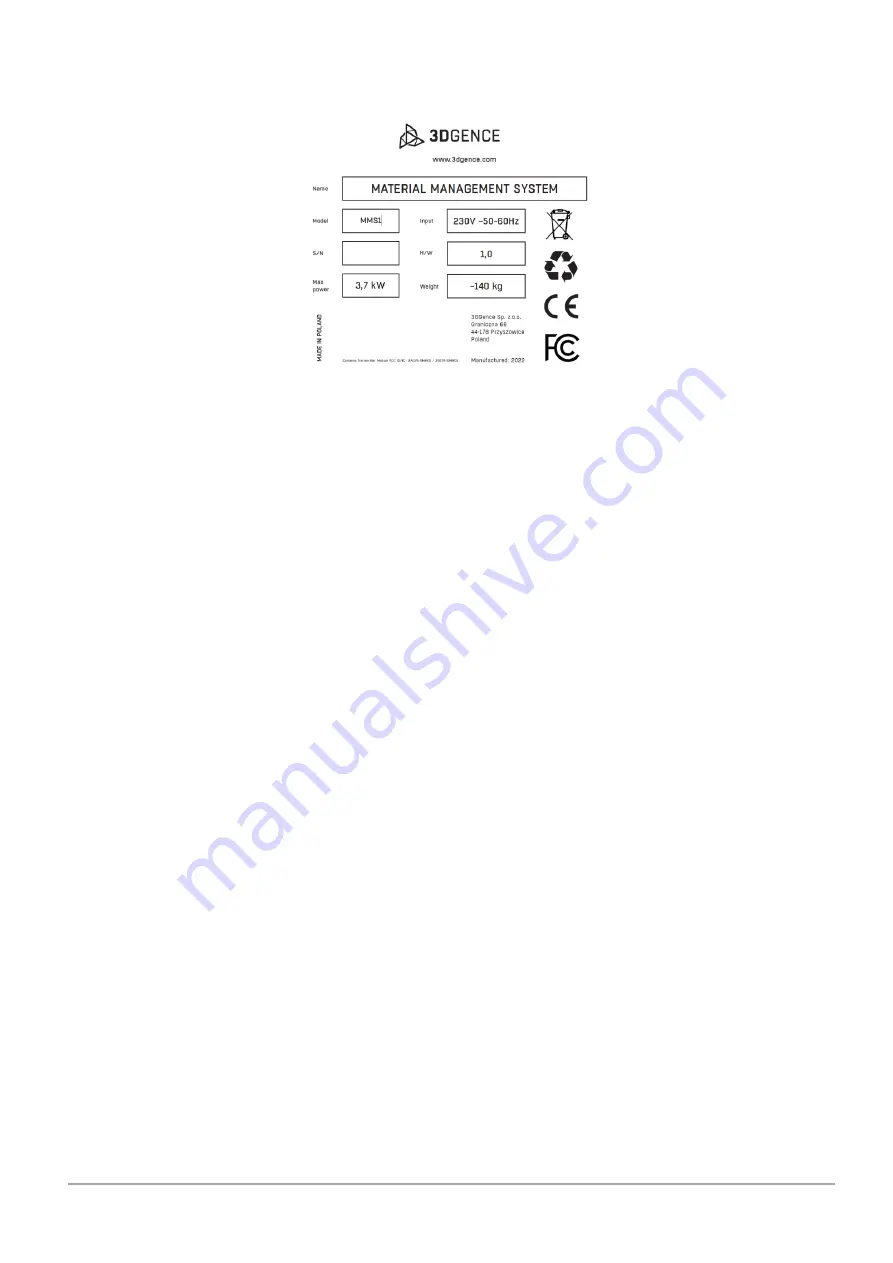
Page
6
of
44
3DGence Material Management System | version 1 | 03.2022
3DGence technical support department will automatically receive the serial number of your device in your request. The serial
number starts with a symbol: S/N MMS1 which should be specified when contacting 3DGence technical support.
Fig.
1
Nameplate of the device
4.
THE IMPORTANCE OF THE MATERIAL DRYING PROCESS FOR THE PRINTING PROCESS
Undesirable degradation processes occurring in plastics processing are well known and preventive steps are clearly defined in
the technical data sheets of the base resins. One type of thermoplastic degradation is degradation by hydrolysis - the separation
of a polymer chain caused by water molecules adhering to the chain. During printing, by heating the filament in the head to a
high temperature, water is removed from its volume. Excess water during the printing process can cause a number of visual
defects (air bubbles, cracking of elements, colour change) and a decrease in the strength properties of the print.
For 3D printing, the most important preparatory step for the printing process is to provide a build material with an optimal,
low water content. In conventional plastics processing (e.g. injection), the permissible water content in the material does not
exceed 0.5% of the weight of the material, and in most cases this value is below 0.08%.
A number of material conditioning methods are used to ensure a material with the correct water content. One of these is dry
air drying which is able to dry the material down to as little as 0.01%. The 3DGence Material Management System uses a similar
dry process air delivery technology. The air passing through the desiccant cartridge provides optimum conditions for effective
material preparation, eliminating the potential risk of the print defects described above.