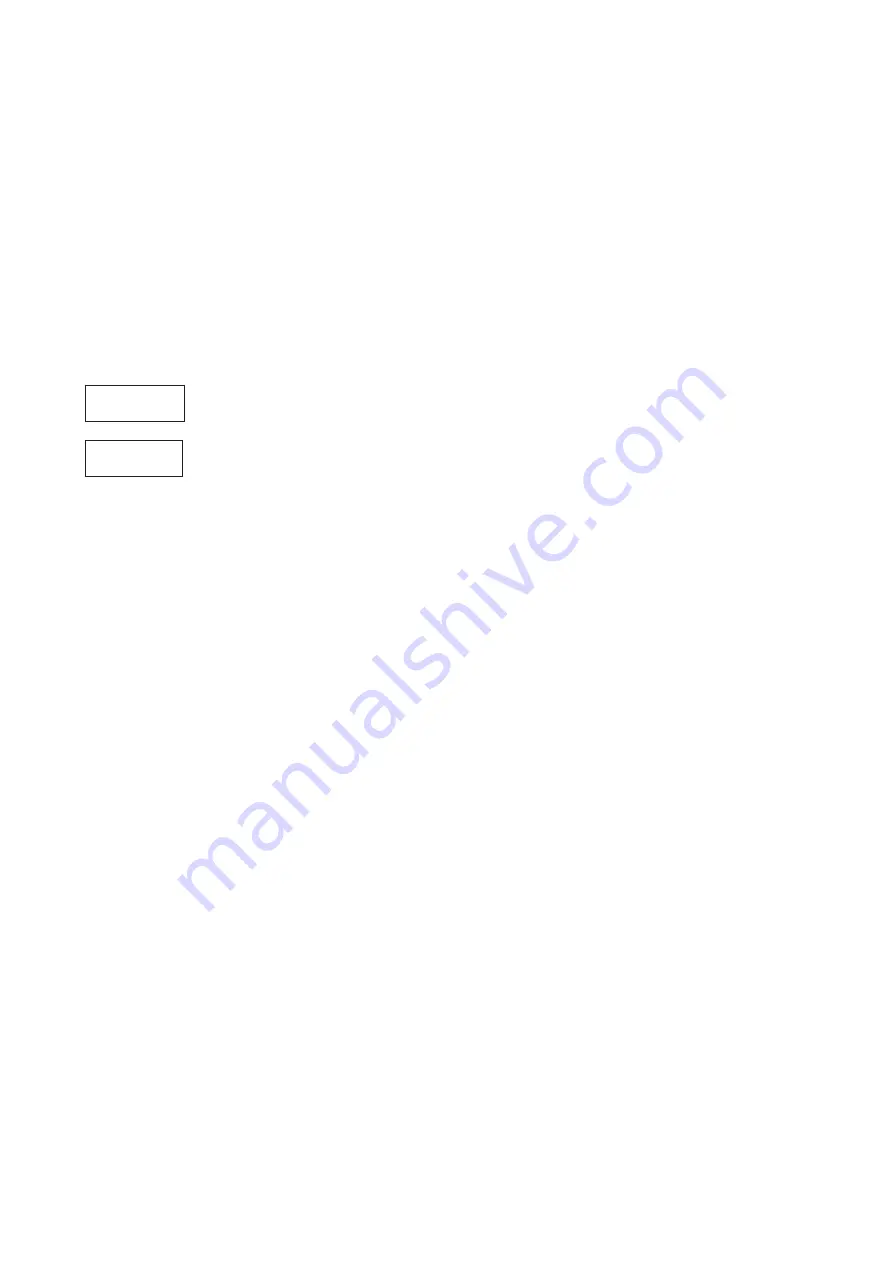
14
The control and feedback signals are lead to the A/D converters of the regulator. The regulator compares the value of
the control signal with the value of the feedback signal from the position transmitter. If a regulation deviation is found the
regulator activates one of the output signals FO, or FZ, until the output shaft of the actuator is shifted to a position
corresponding to the magnitude of the control signal.
The regulator sets the position but it does not influence the shifting speed. This is given by the type and version of
the actuator.
Parameters of the regulator are set by the push-buttons SW1 and SW2; the response is monitored on the pilot lights
D3 and D4
(see Fig.1).
During the operation, the pilot lights indicate the course of regulation and depict the type of
possible error.
Setting of parameters and monitoring of the actuator run can also be accomplished by the computer with service
program connected to the communication connector of the regulator. The computer can also continuously monitor the
magnitude of the control signal and the current position of the actuator, and read diagnostic data
(total operation time and
number of closing of the output relays)
which are stored by the regulator in its memory during the operation. Two plates
are fitted on the regulator. One indicates the date of production and serial number of the regulator and the other the
software version. In case of an inquiry or a comment on the regulator function, it is appropriate to state the version of
the software programmed in the given regulator:
The plate with the indicated type and version of the regulator:
“Sixth piece in the seventh month of 2008”.
The plate indicating the software version:
“Version 4.27 from 2005”.
b) Technical parameters
Supply voltage:
230 V + 10 % -15 %, 50 – 60 Hz
(different voltage on demand)
Protected:
160 mA regulator electronics
1.6
A
output
control
phase
Regulator linearity:
0.5 %
Regulator insensitivity:
1 – 10 %
(adjustable)
Input signals, two-parameter:
TEST
Connection to /disconnection from OV of direct supply voltage
MO, MZ
State of limit switches of actuator
(N / 230V)
TP
State of thermal relay
(N / 230V)
U
Inlet of control phase from BMO
(-/ 230V)
Input signals, analog:
Control signal:
0/4 – 20 mA
(input impedance 250
Ω
),
0 – 10 V
(input impedance 20 k
Ω
);
by
shielded
cable
Feedback signal:
Current transmitter 4 – 20 mA
(e.g. DICONT CPT1)
Output signals, two-parameter:
FO, FZ
Control phase via contacts of relay 5 A / 230 V; protected by fuse 1.6 A
Relay contact OK
Error message; contact 24 V / 2 W
Brake
control signal 2 mA
(for brake module ZP3-BR)
Actuator position
I
2
C bus bar
(signal for additional module)
Output signal, analog:
CPT
Current loop of feedback signal
(maximum loading resistance 100
Ω
)
Signalization:
D3 (yellow)
displayed menu / failure message
D4 (red)
displayed selection / failure message
D5 (green)
feeding
D7 (green/red)
drive opens / closes
Setting elements:
push-button SW1
parameter choice
push-button SW2
parameter value selection
Communication
connector for connecting the computer with service program ZP2RE4
Range of working temperatures:
-25 °C – +75 °C
Dimensions:
75 x 75 x 25 mm
ZP2.RE4
006/0708
EHL SERVO
V 4.27 (c) 2005
Содержание Modact MOKP 100 Ex Series
Страница 2: ......