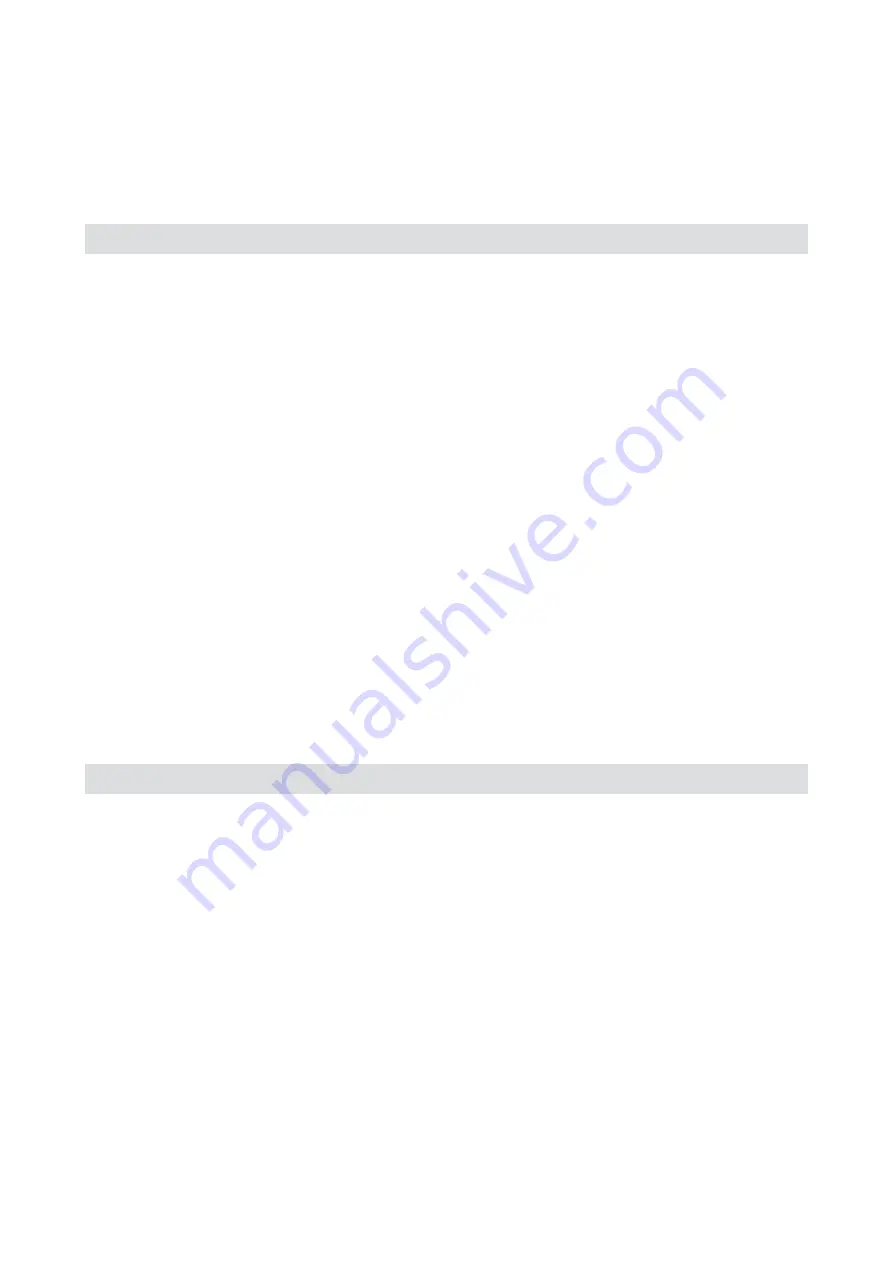
10
Protection
The actuators have external and internal protection terminal against electric shock voltage.
The terminals are identified in compliance with ČSN IEC 417
(34 5550).
If isn´t the actuator equipped with overcurrent protection when purchased is needed to ensure that the
protection is secured externally.
TECHNICAL DESCRIPTION
The entire servo drive consists of solid lock “d” marked Ex d IIC 80 °C
(T6)
. If the servo drive is with local control
system, the local control makes another solid lock “d”. Both solid locks are in such case separated by a bushing.
The electric actuators
MODACT MOKP Ex
consist of two parts:
– Power part -
is composed of a single- or three-phase asynchronous electric motor
(see table no. 1)
, countershaft gear
box, planet gear box with output shaft, device for manual control with a hand wheel and floating screw.
– Control part -
is identical for the electric actuators MODACT MOKP 250 and 600 Ex. For these types, it differs only in
partial turning of units on the main plate. For the electric actuators type no. 52320 the unit of position and signalling
switches is arranged according to Fig. 1. The control part is composed of the position unit 1, -transmitter of position 2,
moment unit 3, terminal board 4 and heating element 5. The position unit is fitted with four micro-switches, always two for
each direction of the output shaft rotation. The point of switching-over of each micro-switch can be separately adjusted
within the working stroke of the electric actuator. The moment unit has independently adjustable micro-switches - one for
each direction of rotation. The moment switches are not blocked against disconnecting at the engagement moment.
The position transmitter is fitted with a slipping clutch enabling its automatic adjustment with the output shaft. The heating
element 8
(Fig. 1)
prevents condensation of water vapour under the control part cover. The position unit and the position
transmitter derive their motion from the output shaft of the electric actuator via a drive wheel or a drive segment - 7.
The moment unit is driven by a “floating screw” of manual control wherein the screw displacement is directly proportional
to twisting moment on the output shaft of the electric actuator. In this way the electric motor can be switched off when
a value of twisting moment is reached to which the moment unit is adjusted.
Warning:
The micro-switches used are of a single-chamber type, i.e. they can operate as a single-position cut-out switch, contact
maker or change-over switch, the moment switches as cut-out switch only - see particular wiring scheme.
If isn´t the actuator equipped with overcurrent protection when purchased is needed to ensure that the protection is
secured externally.
ADJUSTMENT OF ELECTRIC ACTUATOR
a) Stop screws
The stop screws are used to limit the working stroke of the electric actuator to a required value in compliance with and
positions “Closed” or “Opened” of the piping fittings which do not have their own stops. The stop screws are located on
the external side of the electric motor where the external protective terminal is also fitted. When viewing the stop screws,
the right stop screw is intended for the position “Closed” and the left one for the position “Opened”. Herewith, it is assumed
that, when viewed in the direction to the local position indicator, the output shaft moves in the clockwise sense if it rotates in
the direction to “Closed”. Adjustment of the stop screws is carried out in such a way that the stop screws are first released,
the electric actuator with the piping fitting is moved to the position “Closed” and the particular stop screw is rotated until there
is a perceptible increased resistance as the screw strikes against the contact plate of the output shaft of the electric actuator.
The stop screw is secured by proper tightening of its safety nut. Then, the output shaft of the electric actuator is turned to
the position “Opened” and the stop screw is adjusted for the position “Opened” in a similar way.
When adjusting the stop screws of the type no. 52321 care should be taken that the geared segment of drive of
the position and signalling unit in the limit position “Closed” or “Opened” does not strike against the electric motor jacket.
If a tight closure is required in the end position of the piping fitting and, hence, cutting-out of the electric actuator by
means of the moment switches the cutting-out moment should be transferred to the piping fitting. In such case
the particular stop screw is set so that the piping fitting is properly tight when the trips of the output shaft strike against
the stop screw with cutting-out of the moment switch.
The particular moment switch is used for cutting-out the electric actuator. If the stops are to be used for securing
the electric actuator and the piping fitting against damage in case of the position switch failure the stop screws should be
Содержание Modact MOKP 100 Ex Series
Страница 2: ......