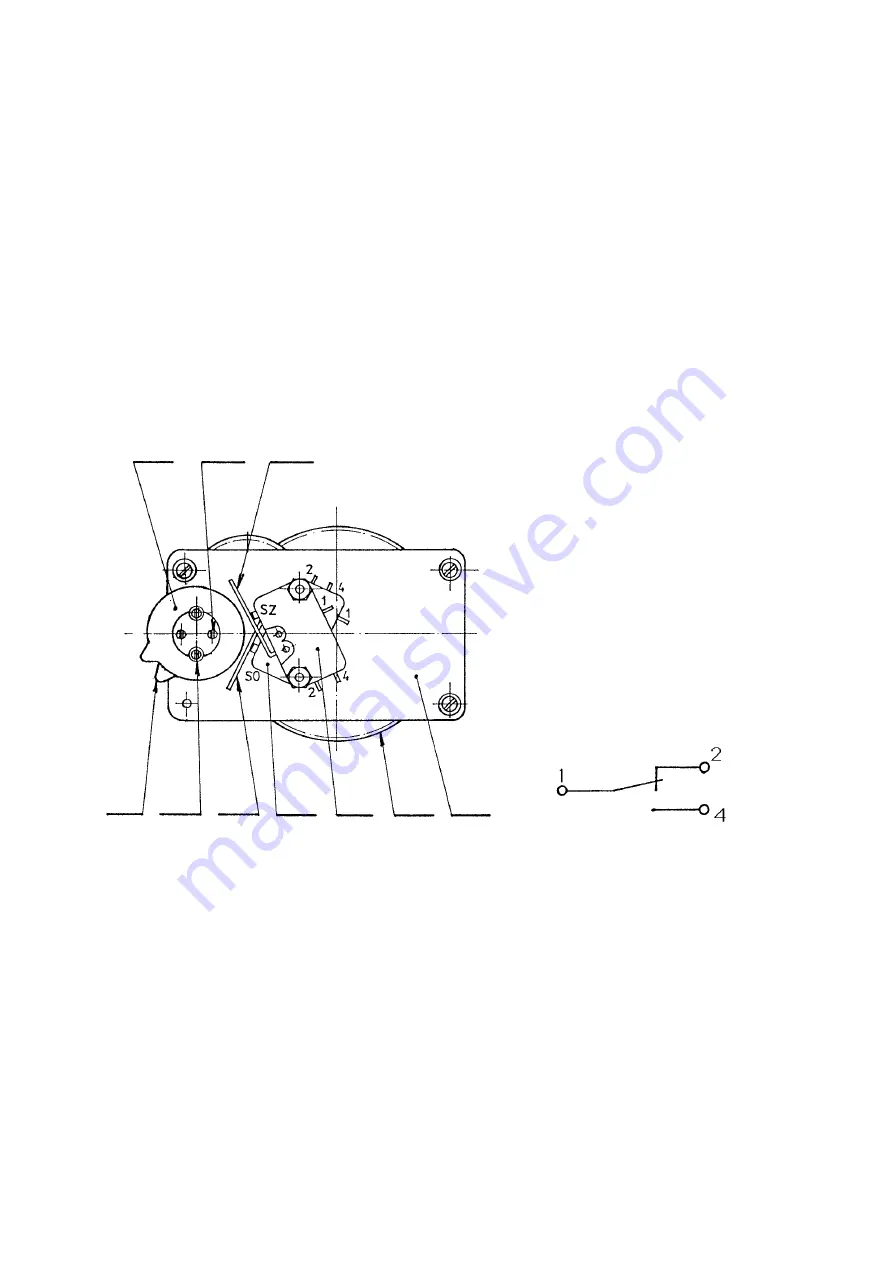
12
the minimum and maximum torques. In this way, the amount of tripping torque
(in Nm)
per scale division is obtained,
making it possible to determine by interpolation the scale division with which the slot in the segment 27 or 28 should
tally. The colour division line which is the nearest to number 10 marks the point of adjustment of the maximum tripping
torque, whereas the other division line shows the point of adjustment of the minimum tripping torque. The torque control
unit should be never adjusted so that the slot in the lower segment is outside the zone marked by the colour scale
division lines. After adjustment of the tripping torque, retighten the lock screw 25 or 26 and the lock nut 44.
b) Signalling unit (Fig. 4)
This unit transmits an electrical signal to indicate the position of the output shaft of the actuator, drive of the unit being
provided via gear wheel 38 by the output shaft through a multistage gearbox to the cams 30 and 31 which control the OPEN
signalling microswitch 36
(SO)
and the CLOSE signalling microswitch 37
(SZ).
The instant of operation of the signalling
switches can be selected at any point of the working stroke of the actuator except the narrow band about the end positions.
(The signalling switch should close before the position-limit switch while the output shaft is still moving).
The upper cam 37
operates in the CLOSE direction, whilst the lower cam 36 operates in the OPEN direction.
Designed as an independent assembly unit, the signalling unit has been assembled on the support 39 under which there are
gears arranged as shown in the kinematic diagram of the Fig. 5. This gearing has been assembled so that the adjusting
wheel K3 can be moved to different levels designated I, II and III after loosening of the lock screw 47. In this way, the range of
adjustment of the signalling switches and the position transmitter can be changed, depending on the working stroke of
the actuator. Fig.5 is a table showing the ranges of adjustment for the individual positions of the adjusting wheel K3.
Adjustment of the signalling unit
If the ranges of adjustment of the signalling switches and the transmitter are required to be changed the
position of adjusting wheel K3 should be changed. For this purpose, the signalling unit should be partially
withdrawn from the control box
(which is possible due to a sufficient length of lead-in wires of the microswitches).
This can be done after removal of the 3 screws 66
(Figs 2 and 2a)
used for mounting the unit onto the base
plate. After the signalling unit has been adjusted to the required range it should be brought back into its original
position. Before retightening the screws 66, the correct meshing of gears K1 and K2 should be checked
(see
Fig. 5).
Put on at the lower end of the camshaft 48
(Fig. 5)
is the pinion 49
(Fig. 5)
which is connected to the
shaft 46 by an adjustable friction clutch. On this pinion, the motion required for driving the potentiometer position
transmitter is sensed. The arrangement of cams and microswitches of the signalling unit is shown in Fig. 4.
Shoulders of the cams 30 or 31 deflect the levers 34 and 35, which in turn control the microswitches 36
(SO)
and 37
(SZ)
. When adjusting the signalling and position-limit switches and the position transmitter, the output
shaft of the actuator should be moved to the position in which changing-over of the microswitches should take
place or the required position of the position transmitter cursor should be reached. When adjusting the signalling
switches, the following procedure should be used: First, loosen the screws 32
(for the CLOSE signalling switch
SZ)
or 33
(for the OPEN signalling switch SO),
as shown in Fig. 4. Then, turn the cam 30 or 31 in the direction
of the arrowhead till the microswitch closes. In this position, hold the cams and retighten the lock screws.
Diagram of microswitches
Fig. 4 -
Signalling unit
30
33
35
31
32
34
36
37 38 39
Legend:
30 – CLOSE direction cams
31 – OPEN direction cams
32 – Screws of CLOSE direction cams
33 – Screws of OPEN direction cams
34 – OPEN direction lever
35 – CLOSE direction lever
36 – OPEN direction microswitch (lower)
37 – CLOSE direction microswitch (upper)
38 – Drive gear
39 – Supporting plate of signalling unit
The encircled numbers correspond to the numbers of termi-
nals on the terminal board of the actuator.
The microswitches can be used as one–circuit devices only.